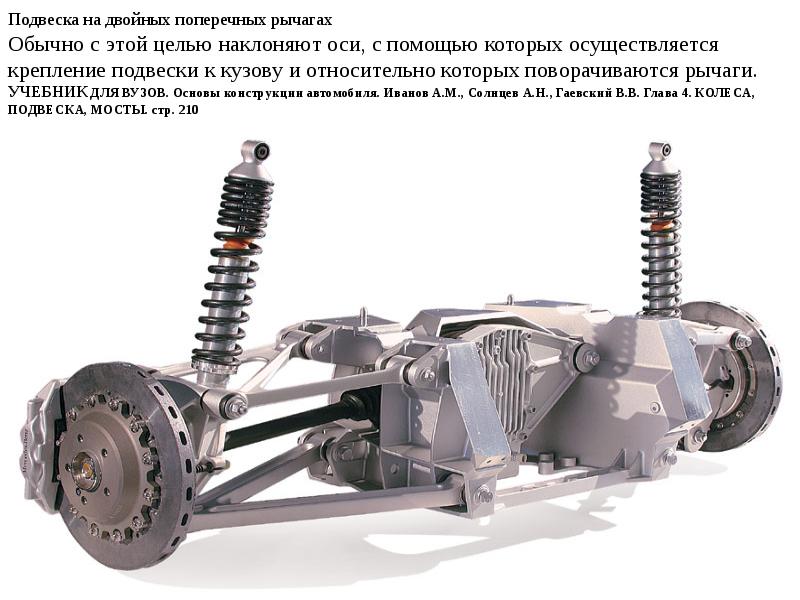
Axle / suspension architecture: MacPherson strut, torsion bar, multi-link ...
Content
How the car works> Axle / suspension architecture: MacPherson strut, torsion bar, multi-link ...
The methods of dealing with suspension deflections are varied and varied, and it is not always easy to navigate in them ... So, let's try to clarify the situation as much as possible by listing the different methods and existing technologies.
McPherson type
This is the most commonly used system on the train. before of our cars, but it can also be used at the back. This is considered a type of independent damping, as opposed to a rigid or semi-rigid axle (each wheel has a stroke that affects what is on the other side of the car).
It consists of arm, anti-roll bar и strong leg who is embodied the lower part of the shock absorber... It can be described as monobras as there is often only one arm (triangle or rod). But it can be made up of two arms to form a triangle. It is a process that brings together efficiency et moderate costwithout forgetting what he takes little space.
This system frees up a lot of space, which is an advantage for cross-engined vehicles that take up a lot of width.
When the suspension fails, the camber angle becomes negative, which is an advantage when cornering. However, this system severely limits the ability to correct geometry. Therefore, it is not something that will be chosen for high performance, even if more advanced versions of this system exist (see below). The orange joint indicates the ball joint between the arm (blue) and the hub (gray).
Difference between MacPherson and Nick MacPherson
The difference is simple, McPherson uses the hand "standard“While pseudo McPherson uses his hand in triangle shape... Good
nickname
MacPherson, which is the most common (well, almost everywhere, even). Note that Macpherson absolutely needs an anti-roll bar (here it is connected to the suspension arm, not to the strut rocket) to steer the front axle longitudinally and laterally. Once we have two independent trains on the same axle, we need an anti-roll bar, which provides the link between the latter two.
Here it is pseudo-MacPherson, because the hand is in the triangle. If it consisted of one bar, it would be MacPherson at all.
The middle "bar" is the cardan shaft (transmits the driving force to the wheels). Rubber is a gimbal cover that contains oil. Here, the anti-roll bar is connected to the suspension arm.
Several types of pseudo-MacPherson strings?
Pivot system?
There are more or less advanced front-end designs that use the MacPherson technique. For the most powerful rods, we use an independent steering system, which consists of improving the wheel steering system (a ball joint on the lever / triangle that allows you to turn left or right). This limits the torque effect, ie the steering pulls to one side during hard acceleration. In combination with a limited slip differential, this allows some pull-ups to approach the power plants in terms of efficiency. Thus, it allows them to place more power under the hood. Because when the front axle has to control direction, engine weight and traction, it needs to be improved.
Hand type?
This is the MacPherson strut BMW 3 Series E90. I have struggled to match the blue stripes with the arms, as his latter are rather curved. In addition, the photo angle was not optimal for highlighting the system. Note that the front axle is lightened because there is no propeller shaft in the case of the power plant.
Semi-rigid axle with torsion bar
(Rear only on middle-aged cars: 90s)
Whereas this system existed on the front axle in the past, since the 80s / 90s it has been limited to servicing the rear axle. This is an independent suspension if there are two torsion bars (or maybe only one), as opposed to a semi-rigid or one hundred percent rigid axle. It is an economical system, but its improvements are therefore limited and can be found on many economical vehicles such as the 100, 90, etc. of the 106s.
Perhaps it will surprise some, but with this device the suspension is entrusted to a straight metal rod, for example i ... And yes, not a spring, but a rod (often two sets) that helps keep the car in the air. (Therefore suspend) and therefore replaces the spring. However, it needs a shock absorber to control the ride and avoid rebound. This is why, looking under 106, you will probably only see a (piston-shaped) shock absorber without a spring.
The advantage of this system is that it is both economical, not cumbersome (leaves more room for habitability and trunk) and quite convenient, despite the "pedigree", much less profitable than multi-link (but heavy!).
This is the blue bar that serves as the source. Indeed, it is firmly attached to points 1 and 2. 1 is the lever (green "stretched lever") that holds the wheel, and 2 is the chassis of the car. Wrong length (a bit like wiping with a damp cloth) and therefore replaces the spring.
There are two torsion bars (orange). One deals with the right hand and the other with the left hand. Each one is the wrong length. Please note that there are several ways to design this system, so it can be different (mostly torsion bars) from car to car. This device can also cause different wheelbase between left and right sides.
And here's what it does in real life (Peugeot 106): A torsion bar suspends the car in the air, and a shock absorber limits travel speed to avoid a spring / rebound effect that would be fatal to the car's behavior.
Semi-rigid H-axis with helical spring
(most popular transverse motor drive system)
It is a type of H-axis that flexibly connects the left and right gears (like two elongated arms connected to each other for coordination). Thus, it looks like a rigid axle, but the rod that connects the two axle shafts is flexible so that the deflection of the wheels located on both sides does not have too much influence on each other (therefore it is neither dependent nor independent, but semiaxis). -hard or semi-independent).
So we need a spring here because we no longer use a torsion bar to suspend the car in the air like we saw with the torsion bar we saw earlier. It is the most common device in France (because it is used primarily for thrust) and replaces the old torsion bar system.
On some cars, the entry-level is offered with a semi-rigid rear axle, while the more upscale trim is served with multi-link suspension.
Here (Golf 4), in addition to the torsion bar, there is a helical spring. Thus, torsion bars are not the only ones that "take" weight (this is the case on many compact cars).
how the rear suspension, axle, spring, shock absorber and bent wheel work)
Here at the top is the entry-level Golf rear axle with torsion bar (the big black cross member that includes the torsion bar) + coil springs for the suspension and finally a damper piston for damping So ... -link to more powerful versions
Double triangulation
(Front or back, this is the noblest system in existence ... There is nothing better!)
Here is the Jaguar F-Pace's double wishbone.
This system is a bit like MacPherson's, but this time it uses two triangles. It is usually offered on very high performance vehicles. The shock absorber is now attached not to the wheel hub, but to the lower triangle (lower). This is the most effective system as it is used in competition. The advantage is to be able to make several adjustments to the way the build works, which is very useful, therefore in competition, as needs differ from one circuit to another. But keep in mind that this system is not just for racing, and that it is used on some cars by everyone. We can talk about multiarms, since there are several triangles (one shoulder = triangle), but you should know that in the language, however, they distinguish the multiarms of double triangulation. The disadvantage is that it takes up more space than some other systems, which usually reduces the boot capacity and interferes with the convenience of front control (the engine takes up a lot of space).
Note that there is also a clamp connecting rod (which prevents the wheels from parallel) and an anti-roll bar which is more or less flexible according to the desired settings.
Note that the diagram does not show the clamp rod (or steering if it is in front) or the anti-roll bar. Finally, as with all illustrations on this page, the location (and shape) of the booms and ball joints can differ from one vehicle to the next.
Here is a Ferrari 360 Modena double wishbone. At least the system is understandable compared to some more complex trains (several levers with different shapes).
Here's an illustration that's a little easier to understand. Here we notice that this is the front axle as we see the steering linkage.
Multibras
(Front or rear, but in general we are talking about multi-link suspension to talk about rear axle. A multi-link front axle is usually called a virtual / offset double triangle).
The system is very similar to a double wishbone, which allows for better performance (compared to a torsion axle) thanks to more precise and intelligent chassis control. In general, this involves connecting the wheel with multiple arms (4 or 5) rather than two triangles to optimize the size of the system (two whole triangles take up a lot of space!). Note that their appearance no longer necessarily has a precise shape, they look like a “headless” version of their tops for some versions, while others no longer look like triangles. The variety of designs is very large and it should be remembered mainly that the principle is based on the use of numerous levers (which can also be called connecting rods or, in short, “metal rods”) ideally positioned in general. four ou five (usually 5 for the rear axle and 4 for the front axle). Most of them are transverse, and another (possible fifth) is longitudinal, in the same direction as the car, that is, parallel. It is then viewed as arm outstretched.
Note that there is also a clamp connecting rod (which prevents the wheels from parallel) and an anti-roll bar which is more or less flexible according to the desired settings.
One disadvantage is that this type of system is difficult to design even for an experienced engineer. As a result, some vehicles with multi-link steering can disappoint pilots who expect more. In spite of everything, the computerized assistance greatly facilitates the work of the engineers, who can then check their results on the screen, without having to carry out tests on the track.
The "extra" fifth arm (this is the "extended arm") is usually present on the rear axle, but does not appear at the front. This prevents the rear of the vehicle from being lifted excessively during very hard braking. Again, the location, shape of the levers, and the location of the ball joints vary from one vehicle to the next (or rather, from one engineer to another). This is a simplified diagram that summarizes how it works.
Here at the front end, there is no typical fifth trailing arm of a multi-link rear axle. Please note that this double triangulation consisting of multiple hands. The upper triangle is formed by two stripes, and the lower one by a block, black arrows indicate these elements. We see this type of build on the A4 and Peugeot 407, showing that the lioness was very technically proficient!
Another view to better understand the essence
Rigid axle / rigid axle
A rustic system that limits comfort and roadholding is unlikely to ever have a car with this type of axle.
The latter connects the left and right wheels with a rigid beam (rear axle only). Therefore, when the left wheel hits a bump, it also affects the right wheel. They are normally connected! This arrangement is used on some large XNUMXxXNUMX vehicles, including pickups. Thus, it is not an independent suspension system.
There are two types: a regular rigid axle and a non-driving rigid axle (there is no built-in transmission to drive the rear wheels).
Parallel Watt
Not very common, this rear axle system is a bit like a mixture of a rigid axle and wishbone. It's best if you see the images yourself in the video below.
Opel Astra 2009: the secrets of its train ... on calls-auto
All comments and reactions
Dernier comment posted:
Fab’s (Date: 2021, 01:25:06)
Hello, I would like to know if there are compatible toyota rear trains to replace certain trains on the peugeot 206 ... thanks
Il I. 8 reaction (s) to this comment:
(Your post will be visible under the comment after verification)
Write a comment
What is the MAIN reason you would buy an electric car?
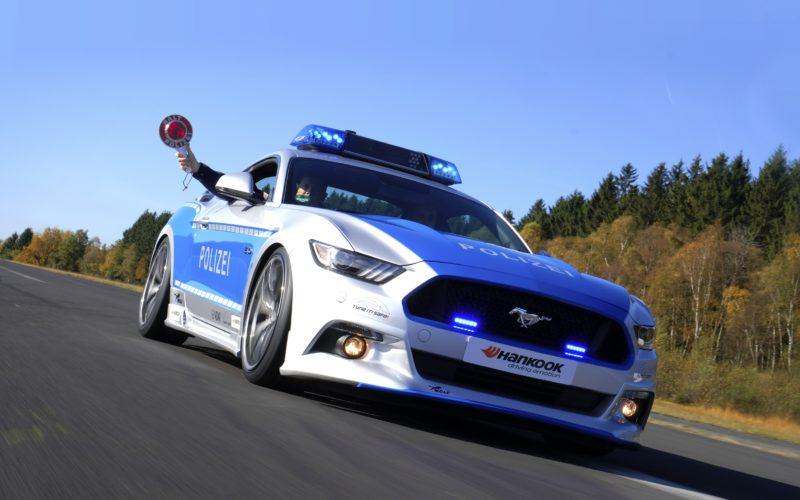
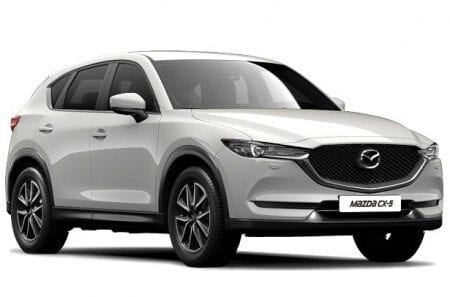