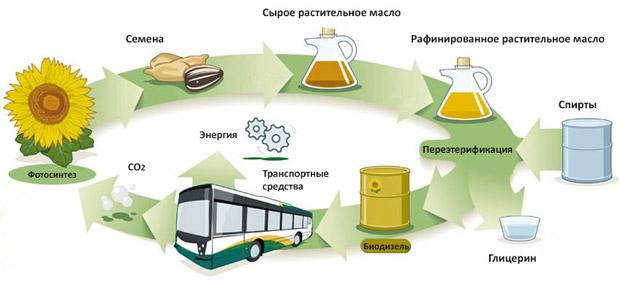
Biodiesel. A necessary step into the future
What is biodiesel made of?
Biodiesel is an environmentally friendly, alternative fuel that can be produced from domestic, renewable sources such as soybean, rapeseed or vegetable oil, as well as animal fats. Biodiesel does not contain petroleum, but it can be mixed with any brand of diesel fuel. Blends of 20% biodiesel and 80% diesel can be used in almost all types of diesel installations. These low-level blends usually do not require any engine modifications (with the exception of fuel filters, fuel hoses and seals on some older diesel engines), but blends containing a higher percentage of biofuels (including pure biodiesel) will already require minor modification.
Biodiesel is easy to use, biodegradable, environmentally friendly and contains virtually no sulfur or aromatics.
The European standard EN 14214 is considered the actual world standard for the type of fuel in question. According to him, the composition of biodiesel includes:
- Vegetable (corn, soybean, rapeseed, sunflower) or animal oil. The use of palm and peanut oils is unacceptable, since the biodiesel obtained from them is not suitable as a winter diesel fuel.
- Triglycerides.
- Monoalkyl esters or methyl esters of fatty acids.
- Alcohols (ethanol or isopropanol; in limited quantities, due to its toxicity, methanol is also used).
- Unavoidable additives in the form of preservatives - tertiary butylhydroquinone, dimethylpolysiloxane or citric acid, which are always found in animal fats. They do not affect the quality of biodiesel.
Production technology
Biodiesel can be made from new or used vegetable oils and animal fats. Biodiesel production technologies are different. Oils and fats are filtered and pretreated to remove water and contaminants. After the processed oils and fats are mixed with alcohol and a catalyst. The oil molecules break down and turn into methyl esters and glycerin, which are then separated from each other and purified.
The most difficult step in obtaining biofuels is the breakdown of long-chain fatty acid molecules linked by a glycerol molecule. During this process, a catalyst (alkali) is used, which breaks down the glycerol molecules and combines each of the fatty acid chains with an alcohol molecule. The result is the creation of monoalkyl or ethyl esters, or esters of fatty acids. During this process - interesterification - glycerol sinks to the bottom and is removed.
Approximately half of the production of biodiesel fuel can use any hydrocarbon feedstock containing fats, even processed lubricants with vegetable or organic components. The other half produces biodiesel exclusively from vegetable oils. Soybean oil is predominant in this series: there is an overproduction of it in the world, and excess production contributes to a decrease in the price of this fuel. The price of biodiesel per liter - from 50 to 100 rubles.
How to make biodiesel at home?
The easiest option is to mix some vegetable oil with regular diesel, thinner or gasoline. Various mixtures are used, ranging from 10% vegetable oil and 90% petroleum products to diametrically opposite proportions. Vegetable oil must be heated before mixing, then its viscosity will decrease, and mixing will be faster.
In the press and on specialized sites, you can read the advice of "craftsmen" on the addition of substances such as turpentine, naphthalene, xylene or unleaded gasoline. Little is known about the effect of these additives on the combustion characteristics of the fuel or their long-term effects on the engine.
A more acceptable option is the production of biodiesel through the necessary chemical reactions, especially since the main components - alcohol, alkali, glycerin - can be easily purchased in stores.
The procedure for producing biodiesel at home is as follows:
- Prepare a transparent container with a volume of 2 liters of chemically resistant plastic with a tight-fitting lid.
- Liter of fresh vegetable oil, heated to 550C, pour into a container and mix with 200 ml of alcohol using a blender. Mixing should be done within 20 minutes.
- Carefully pour in the catalyst - potassium hydroxide (better) or sodium, in an amount of 5 g. (for KOH) or 3,5 g (for NaOH) per 1 liter. You need to add alcohol and catalyst using different funnels.
- Close the container tightly and scroll it in a horizontal plane 5-6 times to speed up the reaction process. Alkali dissolution can last from 15 minutes (for KOH) to 8 hours (for NaOH).
- After the end of the reaction, you should wait another 12-20 hours until the sediment accumulates at the bottom of the container. It should be carefully removed.
Cooked in fresh oil biodiesel has a light yellow color. A certain amount of turbidity will not particularly affect the quality of the fuel.
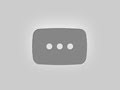
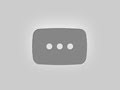
Watch this video on YouTube
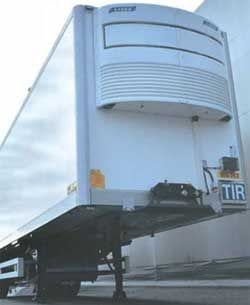
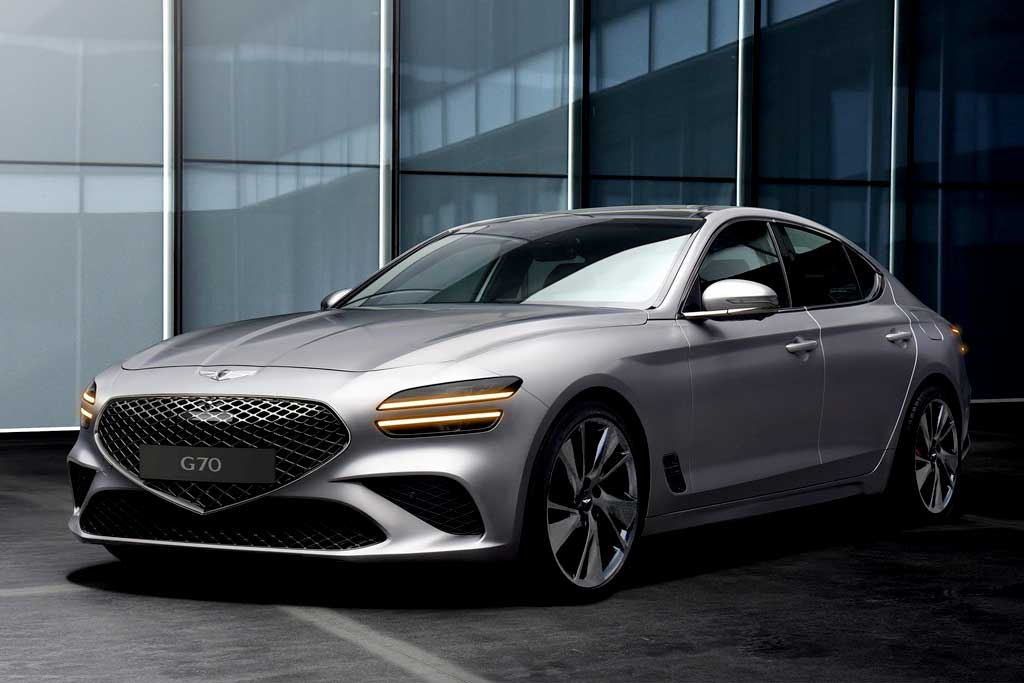