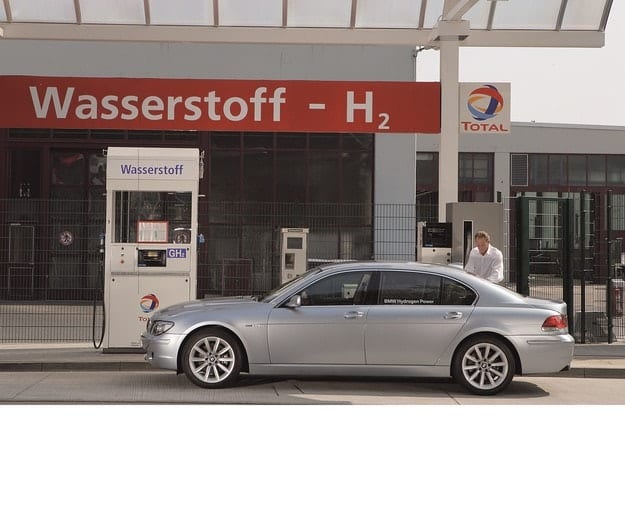
BMW and hydrogen: internal combustion engine
Content
The company's projects began 40 years ago with the hydrogen version of the 5 series
BMW has long believed in electric mobility. Today, Tesla can be considered the benchmark in this area, but ten years ago, when the American company demonstrated the concept of a customized aluminum platform, which was then realized in the form of the Tesla Model S, BMW was actively working on the Megacity Vehicle project. 2013 is marketed as the BMW i3. The avant-garde German car uses not only an aluminum support structure with integrated batteries, but also a body made of carbon-reinforced polymers. However, what Tesla is undeniably ahead of its competitors is its exceptional methodology, especially on the scale of developing batteries for electric vehicles – from relationships with lithium-ion cell manufacturers to building huge battery factories, including those with non-electric applications. mobility.
But let's get back to BMW because, unlike Tesla and many of its competitors, the German company still believes in the mobility of hydrogen. Recently, a team led by the company's Vice President of Hydrogen Fuel Cells, Dr. Jürgen Gouldner, unveiled the I-Hydrogen Next fuel cell, a self-propelled genset powered by a low-temperature chemical reaction. This moment marks the 10th anniversary of the launch of BMW's fuel cell vehicle development and the 7th anniversary of the collaboration with Toyota on fuel cells. However, BMW's reliance on hydrogen goes back 40 years and is a much more "hot temperature".
This is more than a quarter of a century of developments by the company, in which hydrogen is used as a fuel for internal combustion engines. For much of that period, the company believed that a hydrogen-powered internal combustion engine was closer to the consumer than a fuel cell. With an efficiency of about 60% and a combination of an electric motor with an efficiency of more than 90%, a fuel cell engine is much more efficient than an internal combustion engine running on hydrogen. As we will see in the following lines, with their direct injection and turbocharging, today's downsized engines will be extremely suitable for delivering hydrogen—provided the proper injection and combustion control systems are in place. But while hydrogen-powered internal combustion engines are typically much cheaper than a fuel cell combined with a lithium-ion battery, they are no longer on the agenda. In addition, the problems of hydrogen mobility in both cases go far beyond the scope of the propulsion system.
And yet, why hydrogen?
Hydrogen is an important element in the desire of mankind to use more and more alternative energy sources, such as a bridge to accumulate energy from the sun, wind, water and biomass by converting it into chemical energy. Simply put, this means that the electricity produced by these natural sources cannot be stored in large volumes, but can be used to produce hydrogen by decomposing water into oxygen and hydrogen.
Of course, hydrogen can also be extracted from non-renewable hydrocarbon sources, but this has long been unacceptable when it comes to using it as an energy source. It is an undeniable fact that the technological problems of production, storage and transportation of hydrogen are solvable - in practice, even now, huge amounts of this gas are produced and used as raw materials in the chemical and petrochemical industries. In these cases, however, the high cost of hydrogen is not lethal, since it "melts" at the high cost of the products in which it is involved.
However, the problem of using light gas as an energy source and in large quantities is a bit more complicated. Scientists have been shaking their heads for a long time in search of a possible strategic alternative to fuel oil, and the increase in electric mobility and hydrogen may be in close symbiosis. At the heart of all this is a simple but very important fact – the extraction and use of hydrogen revolves around the natural cycle of combining and decomposing water … If humanity improves and expands production methods using natural sources such as solar energy, wind and water, hydrogen can be produced and use in unlimited quantities without emitting harmful emissions.
production
Currently, more than 70 million tons of pure hydrogen are produced in the world. The main raw material for its production is natural gas, which is processed in a process known as “reforming” (half of the total). Smaller quantities of hydrogen are produced by other processes, such as electrolysis of chlorine compounds, partial oxidation of heavy oil, coal gasification, pyrolysis of coal for coke production and gasoline reforming. About half of the world's hydrogen production is used for the synthesis of ammonia (which is used as raw material in the production of fertilizers), in oil refining and in the synthesis of methanol.
These production schemes burden the environment to varying degrees and, unfortunately, none of them offer a meaningful alternative to the current energy status quo – firstly because they use non-renewable sources, and secondly because production emits unwanted substances such as carbon dioxide. The most promising method for the production of hydrogen in the future remains the decomposition of water with the help of electricity, known in elementary school. However, closing the clean energy cycle is currently only possible by using natural and especially solar and wind energy to generate the electricity needed to decompose water. According to Dr. Gouldner, modern technologies "connected" to wind and solar systems, including small hydrogen stations, where the latter are produced on site, are a big new step in this direction.
Storage
Hydrogen can be stored in large quantities in both gaseous and liquid phases. The largest reservoirs in which hydrogen is located at relatively low pressure are called "gas meters." Medium and smaller tanks are designed to store hydrogen at a pressure of 30 bar, while the smallest special tanks (expensive devices made of special steel or carbon fiber reinforced composite materials) maintain a constant pressure of 400 bar.
Hydrogen can also be stored in a liquid phase at -253°C per unit volume containing 1,78 times more energy than when stored at 700 bar – to achieve the equivalent amount of energy in liquefied hydrogen per unit volume, the gas must be compressed up to 1250 bar. Due to the higher energy efficiency of chilled hydrogen, BMW is partnering with the German refrigeration group Linde for its first systems, which has developed state-of-the-art cryogenic devices to liquefy and store hydrogen. Scientists also offer other, but less applicable at the moment, alternatives for storing hydrogen - for example, storage under pressure in special metal flour, in the form of metal hydrides, and others.
Hydrogen transmission networks already exist in areas with a high concentration of chemical plants and oil refineries. In general, the technique is similar to that for the transfer of natural gas, but the use of the latter for the needs of hydrogen is not always possible. However, back in the last century, many houses in European cities were lit by pipeline light gas, which contains up to 50% hydrogen and which is used as fuel for the first stationary internal combustion engines. Today's level of technology already allows transcontinental transportation of liquefied hydrogen through existing cryogenic tankers, similar to those used for natural gas.
BMW and internal combustion engine
"Water. The only end product of clean BMW engines that uses liquid hydrogen instead of petroleum fuel and allows everyone to enjoy new technologies with a clear conscience.”
These words are a quote from an advertising campaign of a German company at the beginning of the 745st century. It should promote a rather exotic XNUMX-hour hydrogen version of the flagship Bavarian automaker. Exotic, because, according to BMW, the transition to alternatives to hydrocarbon fuels, which the auto industry has been feeding from the very beginning, will require a change in the entire industrial infrastructure. At that time, the Bavarians found a promising development path not in the widely advertised fuel cells, but in the conversion of internal combustion engines to hydrogen. BMW believes that the retrofit in question is a solvable problem, and is already making significant progress in solving the main problem of ensuring reliable engine performance and eliminating its tendency to uncontrolled combustion processes using pure hydrogen. The success in this direction is due to competence in the field of electronic control of engine processes and the ability to use the BMW patented patented systems for the flexible gas distribution of Valvetronic and Vanos, without which it is impossible to guarantee the normal operation of "hydrogen engines".
However, the first steps in this direction date back to 1820, when designer William Cecil created a hydrogen-fueled engine operating on the so-called "vacuum principle" - a scheme completely different from that later invented with an internal engine. burning. In his first development of internal combustion engines 60 years later, the pioneer Otto used the already mentioned and coal-derived synthetic gas with a hydrogen content of about 50%. However, with the invention of the carburetor, the use of gasoline has become much more practical and safer, and liquid fuel has replaced all other alternatives that have existed until now. The properties of hydrogen as a fuel were discovered many years later by the space industry, which quickly discovered that hydrogen had the best energy/mass ratio of any fuel known to mankind.
In July 1998, the European Automobile Industry Association (ACEA) pledged to reduce the CO2 emissions of newly registered cars in the Union to an average of 140 grams per kilometer by 2008. In practice, this means a 25% reduction in emissions compared to 1995 and is equivalent to an average fuel consumption in the new fleet of about 6,0 l / 100 km. This makes the task for automotive companies extremely difficult and, according to BMW experts, can be solved either using low-carbon fuel or by completely removing carbon from the fuel composition. According to this theory, hydrogen appears in the automotive scene in all its glory.
The Bavarian company is becoming the first car manufacturer to set about mass production of hydrogen-powered cars. The optimistic and confident statements by BMW Burkhard Göschel, a member of the BMW board of directors responsible for new developments, that "the company will sell hydrogen cars before the expiration of the 7th series", do come true. With the Hydrogen 7 version of the seventh series introduced in 2006, it has a 12-cylinder engine with 260 hp. This message is becoming a reality.
The intention seems rather ambitious, but not without reason. BMW has been experimenting with hydrogen internal combustion engines since 1978, with the 5th series (E12), the 1984-hour version of the E 745 was introduced in 23, and on May 11, 2000, it demonstrated the unique capabilities of this alternative. An impressive fleet of 15 hp The E 750 of the “week” with 38-cylinder hydrogen-powered engines ran a marathon of 12 km, demonstrating particularly vividly the success of the company and the prospects for new technology. In 170 and 000, some of these cars continued to participate in various demonstrations to promote the idea of hydrogen. Then comes a new development, based on the next 2001 series, using a modern 2002-liter eight-cylinder engine and capable of a top speed of 7 km / h, followed by the latest development with a 4,4-cylinder six-liter engine.
According to the official opinion of the company, the reasons why BMW then preferred this technology to fuel cells have both a commercial and a psychological basis. First, this method will require significantly less investment if industrial infrastructure changes. Secondly, because people are accustomed to the good old internal combustion engine, they love it, and it will be difficult to part with it. And thirdly, because at the same time this technology is developing faster than fuel cell technology.
In BMW cars, hydrogen is stored in an over-insulated cryogenic vessel, sort of like a high-tech thermos bottle developed by the German refrigeration group Linde. At low storage temperatures, the fuel is in the liquid phase and enters the engine as normal fuel.
The designers of the Munich company use fuel injection in the intake manifolds, and the quality of the mixture depends on the engine operating mode. In partial load mode, the engine runs on lean mixtures similar to diesel - only the amount of fuel injected is changed. This is the so-called “quality control” of the mixture, in which the engine runs with excess air, but due to the low load, the formation of nitrogen emissions is minimized. When there is a need for significant power, the engine starts to work like a gasoline engine, moving to the so-called "quantitative regulation" of the mixture and to normal (not lean) mixtures. These changes are possible, on the one hand, thanks to the speed of the electronic process control in the engine, and on the other hand, thanks to the flexible operation of the gas distribution control systems - the “double” Vanos, working in conjunction with the Valvetronic intake control system without throttle. It should be borne in mind that, according to BMW engineers, the working scheme of this development is only an intermediate stage in the development of technology and that in the future engines will have to move to direct hydrogen injection into the cylinders and turbocharger. It is expected that the application of these methods will lead to an improvement in the dynamic performance of the car compared to a similar gasoline engine and to an increase in the overall efficiency of the internal combustion engine by more than 50%.
An interesting development fact is that with the latest developments in “hydrogen” internal combustion engines, the designers in Munich are entering the field of fuel cells. They use such devices to power the on-board electrical network in cars, completely eliminating the conventional battery. Thanks to this step, additional fuel savings are possible, since the hydrogen engine does not have to drive the alternator, and the onboard electrical system becomes completely autonomous and independent of the drive path - it can generate electricity even when the engine is not running, and production and consumption energy can be fully optimized. The fact that as much electricity as needed to power the water pump, oil pumps, brake booster and wiring systems can now be generated also translates into further savings. However, in parallel with all these innovations, the fuel injection system (gasoline) has practically not undergone any costly design changes.
In order to promote hydrogen technologies in June 2002, BMW Group, Aral, BVG, DaimlerChrysler, Ford, GHW, Linde, Opel, MAN created the CleanEnergy partnership program, which began its activity with the development of filling stations with liquefied gas. and compressed hydrogen. In them, part of the hydrogen is produced on site using solar electricity, and then compressed, and large liquefied quantities come from special production stations, and all vapors from the liquid phase are automatically transferred to the gas reservoir.
BMW initiated a number of other joint projects, including with oil companies, among which the most active participants are Aral, BP, Shell, Total.
However, why BMW refuses these technological solutions and still focuses on fuel cells, we will tell you in another article in this series.
Hydrogen in internal combustion engines
It is interesting to note that due to the physical and chemical properties of hydrogen, it is much more flammable than gasoline. In practice, this means that much less initial energy is required to initiate the combustion process in hydrogen. On the other hand, hydrogen engines can easily use very "bad" mixtures - something that modern gasoline engines achieve through complex and expensive technologies.
The heat between the particles of the hydrogen-air mixture is less dissipated, and at the same time, the auto-ignition temperature is much higher, as is the rate of combustion processes compared to gasoline. Hydrogen has a low density and a strong diffusivity (the possibility of particles entering another gas - in this case, air).
It is the low activation energy necessary for self-ignition that is one of the biggest problems in controlling combustion processes in hydrogen engines, because the mixture can easily ignite spontaneously due to contact with hotter areas in the combustion chamber and resistance following a chain of completely uncontrolled processes. Avoiding this risk is one of the biggest problems in the design of hydrogen engines, but it is not so easy to eliminate the consequences of the fact that a highly dispersed burning mixture moves very close to the walls of the cylinder and can penetrate into extremely narrow gaps. for example, along closed valves ... All this must be taken into account when designing these engines.
The high temperature of self-ignition and a high octane number (about 130) can increase the degree of compression of the engine and, therefore, its efficiency, but again there is a danger of self-ignition of hydrogen in contact with the hotter part. in the cylinder. The advantage of the high diffusion ability of hydrogen is the possibility of easy mixing with air, which in the event of a tank breakage guarantees quick and safe dispersion of fuel.
The ideal air-hydrogen mixture for combustion has a ratio of about 34:1 (for gasoline this ratio is 14,7:1). This means that when combining the same mass of hydrogen and gasoline in the first case, more than twice as much air is required. At the same time, the hydrogen-air mixture takes up significantly more space, which explains why hydrogen engines have less power. A purely digital illustration of ratios and volumes is quite eloquent - the density of hydrogen ready for combustion is 56 times less than the density of gasoline vapor ... However, it should be noted that, in general, hydrogen engines can operate on air mixtures. hydrogen in ratios up to 180:1 (i.e. with very "bad" mixtures), which in turn means that the engine can run without a throttle and use the principle of diesel engines. It should also be mentioned that hydrogen is the undisputed leader in the comparison between hydrogen and gasoline as a mass energy source - a kilogram of hydrogen has almost three times more energy per kilogram of gasoline.
As with gasoline engines, liquefied hydrogen can be injected directly ahead of the valves in the manifolds, but the best solution is injection directly during the compression stroke - in this case, the power can exceed that of a comparable gasoline engine by 25%. This is because the fuel (hydrogen) does not displace air as with a gasoline or diesel engine, allowing the combustion chamber to fill with only (significantly more than usual) air. In addition, unlike gasoline engines, hydrogen does not need structural swirling, since hydrogen without this measure diffuses quite well with air. Due to the different burning rates in different parts of the cylinder, it is better to install two spark plugs, and in hydrogen engines, the use of platinum electrodes is not suitable, since platinum becomes a catalyst that leads to fuel oxidation even at low temperatures.
Mazda option
The Japanese company Mazda is also showing off its version of the hydrogen engine, in the form of a rotary block in the RX-8 sports car. This is not surprising, since the design features of the Wankel engine are extremely suitable for using hydrogen as a fuel.
Gas is stored under high pressure in a special tank, and fuel is injected directly into the combustion chambers. Due to the fact that in the case of rotary engines, the zones in which injection and combustion take place are separate, and the temperature in the inlet part is lower, the problem with the possibility of uncontrolled ignition is significantly reduced. The Wankel engine also offers ample space for two injectors, which is crucial for injecting the optimum amount of hydrogen.
H2R
The H2R is a working supersport prototype built by BMW engineers and powered by a 12-cylinder engine that reaches a maximum output of 285 hp. when working with hydrogen. Thanks to them, the experimental model accelerates from 0 to 100 km / h in six seconds and reaches a top speed of 300 km / h. The H2R engine is based on the standard top used in the 760i gasoline and took only ten months to develop.
To prevent spontaneous combustion, the Bavarian specialists have developed a special strategy for the flow and injection cycles into the combustion chamber, using the possibilities provided by the engine's variable valve timing system. Before the mixture enters the cylinders, the latter are cooled by air, and ignition is carried out only at top dead center - due to the high combustion rate with hydrogen fuel, ignition advance is not required.
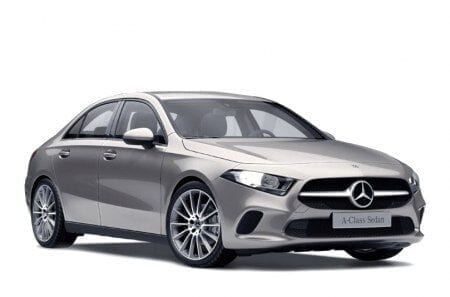