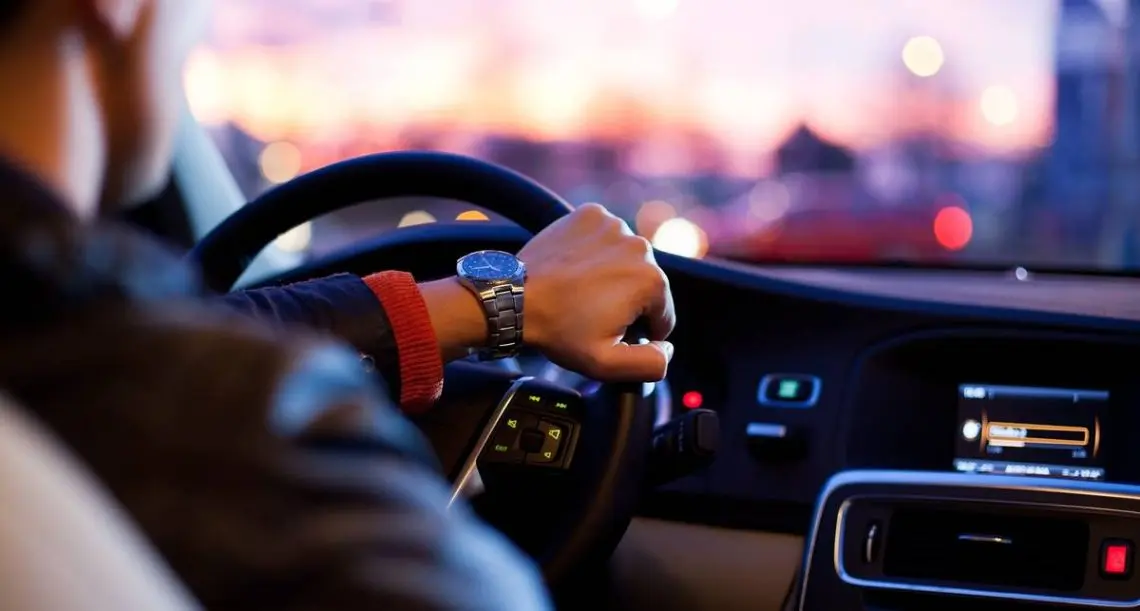
What is dependent and independent suspension of a car?
Content
What is dependent and independent suspension of a car?
The suspension is a system that connects the vehicle body to the wheels. It is designed to dampen shocks and shaking due to uneven roads and ensure the stability of the machine in various conditions.
The main parts of the suspension are elastic and damping elements (springs, springs, shock absorbers and rubber parts), guides (levers and beams connecting the body and wheels), support elements, stabilizers and various connecting parts.
There are two main types of suspension - dependent and independent. This refers to the dependence or independence of the wheels of the same axle while driving over uneven pavement.
dependent suspension. The wheels of one axle are rigidly connected to each other and the movement of one of them leads to a change in the position of the other. In the simplest case, it consists of a bridge and two longitudinal springs. A variant on guide levers is also possible.
Independent suspension. Wheels on the same axle are not connected to each other, and the displacement of one does not affect the position of the other.
The principle of operation of dependent suspension
If you look at the dependent suspension scheme, you can see that the connection affects the vertical movement of the wheels and their angular position relative to the road plane.
When one of the wheels moves up, the second will go down, since the elastic elements and the entire guide vane are located inside the vehicle track. Compressing the spring or spring on the left side of the car unloads the body, respectively, the right spring is partially straightened, the distance between the body and the road on the right increases. It is not always unambiguous, since the picture will be distorted by the resulting body rolls and much depends on the height of the center of mass of the car and the distance along the axis from the spring or levers to the wheel. Such effects, which cause the vehicle to roll and tend to sway, are taken into account when calculating the suspensions.
Since both wheels are in parallel planes, if we neglect the artificially created camber angles, then the tilt of one of them, for example, to the left will cause the second one to have a similar angle in the same direction. But in relation to the body, the instantaneous camber angle will change in the same way, but with the opposite sign. The changing camber at the wheel always worsens traction, and with this scheme, this happens immediately with both wheels on the axle. Hence the unsatisfactory operation of dependent suspensions at high speeds with lateral loads in corners. And the disadvantages of such a suspension are not limited to this.
The role of a spring in the general sense of the word can be directly typical spring structures made of different materials and with a different number of sheets in the set, including variable stiffness (with springs), as well as springs or air springs similar to them in layout.
Leaf suspension. Springs can be located longitudinally or transversely, form different arcs, from a quarter of an ellipse to a full one. The suspension on two semi-elliptical springs located along the body has long become a classic. Other designs were used in the first half of the last century.
The properties of the leaf spring are such that it has a normalized stiffness in the vertical plane, and in all others, its deformation can be neglected, so this design does not contain a separate guide vane. The entire bridge is attached to the frame or to the body exclusively through the springs.
This pendant includes:
- springs containing one or more flat metal sheets, sometimes composite materials are used;
- clamps fastening together the spring sheets of the typesetting structures;
- anti-creak washers, which reduce friction and improve acoustic comfort, are located between the sheets;
- suspension springs, which are additional smaller springs that come into action when a part of the suspension travel is selected and change its stiffness;
- ladders fastening the spring to the beam of the bridge;
- front and lower mounting brackets with bushings or silent blocks, which allow compensating for a change in the length of the spring during compression, sometimes they are called earrings;
- cushions-chippers that protect the sheets from irreversible deformation with maximum bending at the end of the working stroke.
All dependent suspensions are equipped with separately installed shock absorbers, the type and location of which does not depend on the type of the elastic element.
The springs are capable of transmitting pulling and braking forces from the axle beam to the body with a slight deformation, prevent the axle from twisting about its own axis and resist lateral forces in corners. But due to the inconsistency of requirements for rigidity in different directions, they do it all equally badly. But this is not essential everywhere.
On heavy multi-axle vehicles, balance-type suspensions can be used, when one pair of springs serves two adjacent axles, resting on their ends, and is fixed on the frame in the center. This is a typical truck suspension with its own advantages and disadvantages.
Spring dependent suspension. The role of the elastic element is performed by cylindrical springs or air springs, so this type requires a separate guide vane. It can be of different designs, most often a system of five jet rods is used, two upper, two lower and one transverse (Panhard rod).
There are other solutions, for example, from two longitudinal rods with one transverse one, or with the replacement of the Panhard rod with a Watt parallelogram mechanism, which better stabilizes the bridge in the transverse direction. In any case, the springs work only in compression, and all the moments from the bridge are transmitted through reactive thrusts with silent blocks at the ends.
The principle of operation of independent suspension
Independent suspensions are widely used in the front steered wheels of passenger cars, since their use significantly improves the layout of the engine compartment or trunk and reduces the possibility of self-oscillation of the wheels.
As an elastic element in an independent suspension, springs are usually used, somewhat less often - torsion bars and other elements. This expands the possibility of using pneumatic elastic elements. The elastic element, with the exception of the spring, has practically no effect on the function of the guide device.
For independent suspensions, there are many schemes of guide devices, which are classified according to the number of levers and the location of the swing plane of the levers.
In an independent front linkage suspension, the wheel hub is mounted with two angular contact tapered roller bearings on the trunnion of the steering knuckle, which is connected to the rack by a pivot. A thrust ball bearing is installed between the strut and the steering knuckle.
The rack is pivotally connected by threaded bushings to the upper and lower forked levers, which, in turn, are connected to axles fixed to the frame crossbars by means of rubber bushings. The elastic element of the suspension is a spring, resting with its upper end through a vibration-insulating gasket against the stamped head of the cross member, and with its lower end against the support cup, bolted to the lower arms. The vertical movement of the wheels is limited by the stop of the rubber buffers in the beam.
A double-acting telescopic hydraulic shock absorber is installed inside the spring and connected with the upper end to the transverse frame through rubber cushions, and with the lower end to the lower levers.
Recently, the "swinging candle" suspension has become widespread. McPherson. It consists of one lever and a telescopic strut, on the one hand rigidly connected to the steering knuckle, and on the other - fixed in the heel. The heel is a thrust bearing mounted in a pliable rubber block mounted on the body.
The rack has the ability to wiggle due to the deformation of the rubber block and rotate around an axis passing through the thrust bearing, the outer hinge of the lever.
The advantages of this suspension include a small number of parts, less weight and space in the engine compartment or trunk. Usually, the suspension strut is combined with a shock absorber, and the elastic element (spring, pneumatic element) is mounted on the strut. The disadvantages of the MacPherson suspension include increased wear of the strut guide elements with large suspension travels, limited possibilities for varying kinematic schemes and a higher noise level (compared to a suspension on two wishbones.
The device and operation of MacPherson suspensions are described in detail below.
The oscillating strut suspension has a forged arm to which the stabilizer arm is connected via rubber pads. The transverse part of the stabilizer is attached to the body cross member with rubber pads and steel brackets. Thus, the diagonal arm of the stabilizer transmits longitudinal forces from the wheel to the body and therefore forms part of the integrated suspension guide arm. Rubber cushions allow you to compensate for distortions that occur when such a composite arm swings, and also dampen longitudinal vibrations transmitted from the wheel to the body.
The rod of the telescopic strut is fixed on the lower base of the rubber block of the upper heel and does not rotate together with the strut and the spring installed on it. In this case, with any rotation of the steered wheels, the rack also rotates relative to the rod, removing the static friction between the rod and the cylinder, which improves the response of the suspension to small road irregularities.
The spring is not installed coaxially with the rack, but is inclined towards the wheel in order to reduce the transverse loads on the rod, its guide and piston, which occur under the influence of vertical force on the wheel.
A feature of the suspension of steered wheels is that it should allow the wheel to make turns regardless of the deflection of the elastic element. This is ensured by the so-called pivot assembly.
Suspensions can be pivot and pivotless:
- With a pivot suspension, the knuckle is fixed on a pivot, which is mounted with some inclination to the vertical on the suspension strut. To reduce the friction moment in this joint, needle, radial and thrust ball bearings can be used. The outer ends of the suspension arms are connected to the rack by cylindrical joints, usually made in the form of lubricated plain bearings. The main disadvantage of the pivot suspension is the large number of hinges. When swinging the levers of the guide device in the transverse plane, it is impossible to achieve the “anti-dive effect” due to the presence of the center of the longitudinal roll of the suspension, since the swing axes of the levers must be strictly parallel.
- Besshkvornevy independent suspension brackets where cylindrical hinges of a rack are replaced with spherical ones have become much more widespread. The design of this hinge includes a pin with a hemispherical head, it is fitted with a ceramic-metal support insert, which works on the spherical surface of the hinge body. The finger rests on a nylon-coated special rubber insert mounted in a special holder. The hinge housing is attached to the suspension arm. When the wheel is turned, the pin rotates around its axis in the liners. When the suspension deflects, the pin, together with the insert, swings relative to the center of the sphere - for this, there is an oval hole in the body. This hinge is load-bearing, since through it the vertical forces are transmitted from the wheel to the elastic element, the spring, which rests on the lower suspension arm. Suspension arms are attached to the body either by means of cylindrical plain bearings, or by means of rubber-metal hinges, which work due to the shear deformation of rubber bushings. The latter require lubrication and have a vibration-isolating property.
Which suspension is better?
Before answering this question, you should consider the pros and cons of both types of pendants.
Among the advantages Hung upиmy suspensions - high strength and reliability of the design, uniform grip with the roadway and increased cornering stability, as well as the invariance of clearance, track width and other wheel position indicators (very useful on off-road).
Among the disadvantages of dependent suspension:
- suspension stiffness can cause discomfort while driving on a bad road;
- reduced vehicle control;
- the complexity of the adjustment;
- heavy parts significantly increase the unsprung mass, which negatively affects the smoothness of the ride and the dynamic characteristics of the machine, and also increases fuel consumption.
Independent suspension and its benefits:
- increased ride comfort, since the collision of one of the wheels with an unevenness in no way affects the other;
- less risk of rolling over when hitting a serious hole;
- better handling, especially at high speed;
- reduced weight provides improved dynamic performance;
- wide range of adjustment options to achieve optimal parameters.
The disadvantages include:
- due to the complex design, the service will be expensive;
- increased vulnerability when driving off-road;
- track width and other parameters may change during operation.
So which is better? Suspension is one of the most frequently repaired machine components. This must be taken into account when choosing a car. Repair of an independent suspension will cost more than a dependent one. In addition, the independent, most likely, will have to be repaired more often. It will not be superfluous to inquire about the availability of spare parts. Genuine parts of proper quality for foreign cars may have to be ordered separately.
For driving mainly on asphalt, the best option is front independent suspension and rear dependent. For an SUV or other car that is supposed to be used off-road, dependent suspension is the best choice - on both axles or at least on the rear. The bridge won't hold most of the dirt. And soil and snow will stick very actively to the parts of the independent suspension. At the same time, even with a bridge bent on a mountain road, the car will remain on the move. But the breakdown of the independent suspension will not allow the car to continue moving. True, in urban conditions, handling with such a scheme will not be the best.
In recent years, manufacturers have begun to equip some cars with suspensions that can operate in several modes. Their electronics allow you to quickly, on the go, change the parameters depending on the traffic situation. If funds allow, it is worth looking at models that have such a system.

