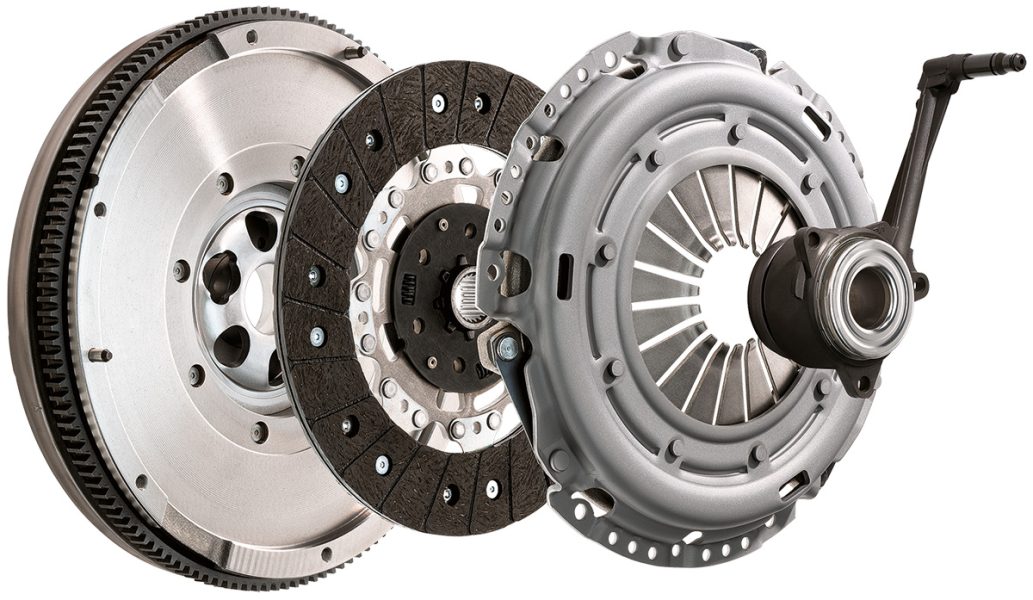
Dual-mass (dual-mass) flywheel - principle, design, series
Content
By the slang term for a dual-mass or dual-mass fly, there is a device called a dual-mass flywheel. This device allows the transmission of torque from the engine to the transmission and further to the wheels of the vehicle. The dual-mass flywheel has attracted public attention due to its often limited lifespan. The exchange is not only laborious, but also requires financial costs, since the wallet contains from several hundred to a thousand euros. Among motorists, you can often hear the question of what two-wheeled cars are used for when there were once no problems with cars.
A bit of theory and history
The reciprocating internal combustion engine is a relatively complex machine, the operation of which is interrupted in phase. For this reason, a flywheel is connected to the crankshaft, the task of which is to accumulate sufficient kinetic energy to overcome passive resistances during compression strokes (non-working). This achieves, among other things, the required uniformity of the engine. The engine runs more balanced the more cylinders the engine has or the larger (heavier) flywheel. However, a heavier flywheel reduces the engine's survivability and reduces its readiness to spin quickly. This phenomenon can be observed, for example, with a 1,4 TDi or 1,2 HTP engine. With a more powerful flywheel, these three-cylinder engines run slower and slow down as well. The disadvantage of this behavior is, for example, slower gear changes. The size of the flywheel is additionally influenced by the composition of the cylinders (in-line, fork or boxer). An opposed-roller opposed-roller engine is in principle much more balanced than, for example, an in-line four-cylinder engine. Therefore, it also has a smaller flywheel than a comparable inline four-cylinder engine. The size of the flywheel also affects the principle of combustion, for example, modern diesel engines almost always need a flywheel. Compared to gasoline counterparts, diesel engines typically have a much higher compression ratio, above which they consume significantly more work - the kinetic energy of a rotating flywheel.
The kinetic energy Ek associated with a rotating flywheel is calculated using the following formula:
Ec = 1/2·J ω2
(where J is the moment of inertia of the body about the axis of rotation, ω is the angular velocity of rotation of the body).
Balance shafts also help eliminate uneven operation, but they require a certain amount of mechanical work to propel them. In addition to unevenness, the periodic repetition of the four periods also leads to torsional vibration, which adversely affects the drive and transmission. The normal inertial mass of an internal combustion engine consists of the inertial masses of the parts of the crank mechanism (balance shafts), flywheel and clutch. However, this is not enough to eliminate unwanted vibrations in the case of powerful and especially less cylindrical diesel engines. Consequently, the transmission and the entire drive system must be protected from these adverse effects, as excessive resonance can occur at certain speeds, resulting in excessive stress on the crankshaft and transmission, unpleasant body vibrations, and the hum of the vehicle interior. This can be clearly seen in the diagram below, which shows the vibration amplitude of the engine and transmission with conventional and dual-mass flywheels. Vibrations of the crankshaft at the exit from the engine and oscillations at the entrance of the transmission have practically the same amplitude and frequency. At certain speeds, these fluctuations overlap, which leads to the indicated undesirable risks and manifestations.
It is common knowledge that diesel engines are significantly stronger than gasoline engines, so their parts are heavier (crank mechanism, connecting rods, etc.). Sizing and balancing such an engine is a really complex problem, the solution of which consists of a series of integrals and derivatives. Briefly, an internal combustion engine is made up of a number of components, each with its own weight and stiffness, which together form a system of torsion springs. Such a system of material bodies, connected by springs, tends to oscillate at different frequencies during operation (under load). The first significant band of oscillation frequencies lies in the range of 2-10 Hz. This frequency can be considered natural and is practically not perceived by a person. The second frequency band is in the range of 40-80 Hz, and we perceive these vibrations as vibrations, and the noise as a roar. The task of designers is to eliminate this resonance (40-80 Hz), which in practice means moving to a place where a person is much less unpleasant (about 10-15 Hz).
The car contains several mechanisms that eliminate unpleasant vibrations and noise (silent blocks, pulleys, noise insulation), and at the core is a classic conventional disc friction clutch. In addition to transmitting torque, its task is also to dampen torsional vibrations. It contains springs which, in the event of an unwanted vibration, compress and absorb most of its energy. In the case of most gasoline engines, the absorption capacity of one clutch is sufficient. A similar rule applied to diesel engines until the mid-90s, when the legendary 1,9 TDi with Bosch VP rotary pump was sufficient with a conventional clutch and a classic single-mass flywheel.
However, over time, diesel engines began to provide more and more power due to less and less volume (number of cylinders), the culture of their operation came to the fore, and, last but not least, the pressure on the "saw flywheel" was also developed more and more stringent environmental standards. In general, the damping of torsional vibrations could no longer be provided by classical technology, and therefore the need for a two-mass flywheel became a necessity. The first company to introduce the ZMS (Zweimassenschwungrad) dual-mass flywheel was LuK. Its mass production began in 1985, and the German BMW was the first automaker to show interest in the new device. The dual-mass flywheel has undergone a number of improvements since then, with the ZF-Sachs planetary gear train currently considered the most advanced.
Dual mass flywheel – design and function
A dual-mass flywheel practically functions like a conventional flywheel, which also performs the function of damping torsional vibrations and thus largely eliminates unwanted vibrations and noise. The dual-mass flywheel differs from the classic one in that its main part - the flywheel - is flexibly connected to the crankshaft. Therefore, in the critical phase (up to the peak of compression) it allows some deceleration of the crankshaft, and then again (during expansion) some acceleration. However, the speed of the flywheel itself remains constant, so the speed at the output of the gearbox also remains constant and without vibration. The dual mass flywheel transfers its kinetic energy linearly to the crankshaft, the reaction forces acting on the engine itself are smoother, and the peaks of these forces are much lower, so the engine also vibrates and shakes the rest of the engine less. body. The division into primary inertia on the motor side and secondary inertia on the gearbox side increases the moment of inertia of the rotating parts of the gearbox. This moves the resonant range to a lower frequency (rpm) range than the idle speed and thus is out of the range of the engine's operating speeds. In this way, the torsional vibrations generated by the engine are separated from the transmission, and transmission noise and body roar no longer occur. Due to the fact that the primary and secondary parts are connected by a torsional vibration damper, it is possible to use a clutch disc without a torsional suspension.
The dual-mass flywheel also serves as a so-called shock absorber. This means it helps dampen clutch hits during gear shifts (when engine speed needs to be balanced with wheel speed) and also helps smoother starts. However, the resilient elements (springs) in a dual-mass flywheel constantly tire and allow the flywheel to move wider and easier relative to the crankshaft. The problem arises when they are already tired - they are pulled out completely. In addition to stretching the springs, flywheel wear also means pushing out the holes on the locking pins. Thus, the flywheel not only does not dampen oscillations (oscillations), but, on the contrary, creates them. Stops at the extreme limits of flywheel rotation begin to appear, most often as bumps when shifting gears, starting, just in all situations when the clutch is engaged or disengaged, or when changing speed. Wear will also show up as jerky start-ups, excessive vibration and noise around 2000 rpm, or excessive vibration at idle. In general, dual mass flywheels experience much greater stress in less cylindrical engines (e.g. three/four cylinders) where the unevenness is much greater than in six cylinder engines.
Structurally, a dual-mass flywheel consists of a primary flywheel, a secondary flywheel, an internal damper and an external damper.
How to Affect / Extend the Life of a Dual Mass Flywheel?
Flywheel life is influenced by its design as well as the properties of the engine in which it is installed. The same flywheel from the same manufacturer runs 300 km on some engines, and on some it will take only half a portion. The original intention was to develop dual-mass flywheels that would survive to the same age (km) as the entire car. Unfortunately, in reality, the flywheel often needs to be replaced much earlier, many times before the clutch disc. In addition to the design of the engine and the dual-mass flywheel itself, the conductor has a significant impact on its service life. All situations leading to the transmission of a blow in one direction or another reduce its service life.
In order to prolong the life of the Dual Mass Flywheel, it is not recommended to frequently drive the engine understeer (especially below 1500 rpm), depress the clutch hard (preferably without shifting when changing gears), and not downshift the engine (i.e. brake the engine ). only at a reasonable speed). It often happens that at a speed of 80 km / h you turn on not second gear, but third or fourth and gradually shift to a lower gear). Some manufacturers recommend (in this case VW) that if the car is parked with a stationary car on a gentle bank, the handbrake must first be applied and then a gear (reverse or XNUMXth gear) must be engaged. Otherwise, the vehicle will move slightly and the dual-mass flywheel will get into a so-called permanent engagement, causing tension (stretching of the springs). Therefore, it is recommended not to use uphill speed, and if so, only after braking the vehicle with a handbrake, so as not to cause a small movement and subsequent long-term load - closing the transmission system, i.e. a dual-mass flywheel. An increase in the temperature of the clutch disc is also directly related to a reduction in the life of the dual-mass flywheel. The clutch overheats, especially when towing a heavy trailer or other vehicle, driving off-road, etc. The clutch will unlock itself even if the engine is broken. It should be noted that radiant heat from the clutch disc leads to overheating of various flywheel components (especially if it is a lubricant leak), which further negatively affects the service life.
Repair - replacement of the dual-mass flywheel and replacement with a conventional flywheel
There is no such thing as repairing an excessively worn flywheel. Repair involves replacing the flywheel together with the clutch assembly (lamellae, compression spring, bearings). The entire repair is quite laborious (about 8-10 hours), when it is necessary to dismantle the gearbox, and sometimes even the engine. Of course, we must not forget about finance, where the cheapest flywheels are sold for about 400 euros, the most expensive - more than 2000 euros. Why change a clutch disc that is still in good condition? But simply because when servicing a clutch disc, it is only a matter of time before it goes away, and this time-consuming process, which is several times more expensive than the clutch disc, will have to be repeated. When replacing a flywheel, it is a good idea to see if there is a more sophisticated version that can handle more miles - supported and approved by the vehicle manufacturer, of course.
Very often you can find information about replacing a two-mass flywheel with a classic one, in which lamellas with a torsion damper are used. As already mentioned in previous articles, a dual-mass flywheel, in addition to its convenient functions, also performs the function of a torsional vibration damper, which negatively affects the condition of the moving parts of the engine (crankshaft) or gearbox. To a certain extent, vibration damping can also be eliminated by the sprung plate itself, but it cannot provide the same performance as the much more powerful and complex dual-mass flywheel. Plus, if it were that simple, it would have long been practiced by car manufacturers and their financial owners, who are constantly working to cut costs. Therefore, it is generally not recommended to replace the dual mass flywheel with a single mass flywheel.
Don't underestimate replacing a worn flywheel
It is strongly not recommended to postpone the replacement of an excessively worn flywheel. In addition to the above manifestations, there is a risk of loosening (separation) of any part of the flywheel. In addition to destroying the flywheel itself, the engine or transmission can also be fatally damaged. Excessive flywheel wear also affects the correct operation of the engine speed sensor. As the spring elements gradually wear out, the two flywheel parts deflect more and more until they are outside the tolerances set in the control unit. Sometimes this leads to an error message, and sometimes, on the contrary, the control unit tries to adapt and control the engine based on incorrect data. This leads to poor performance and, in the worst case, start-up problems. This problem is especially common with older engines where a crankshaft sensor detects movement on the output side of the dual-mass flywheel. Manufacturers have eliminated this problem by changing the sensor mounting, so in newer engines it detects the crankshaft speed at the flywheel inlet.
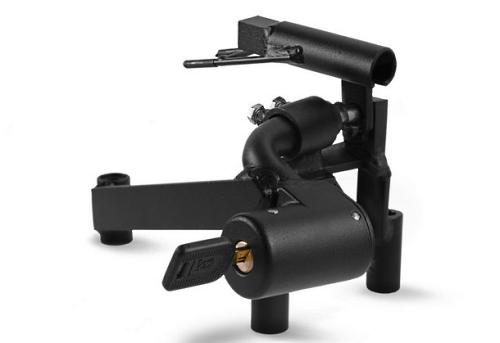
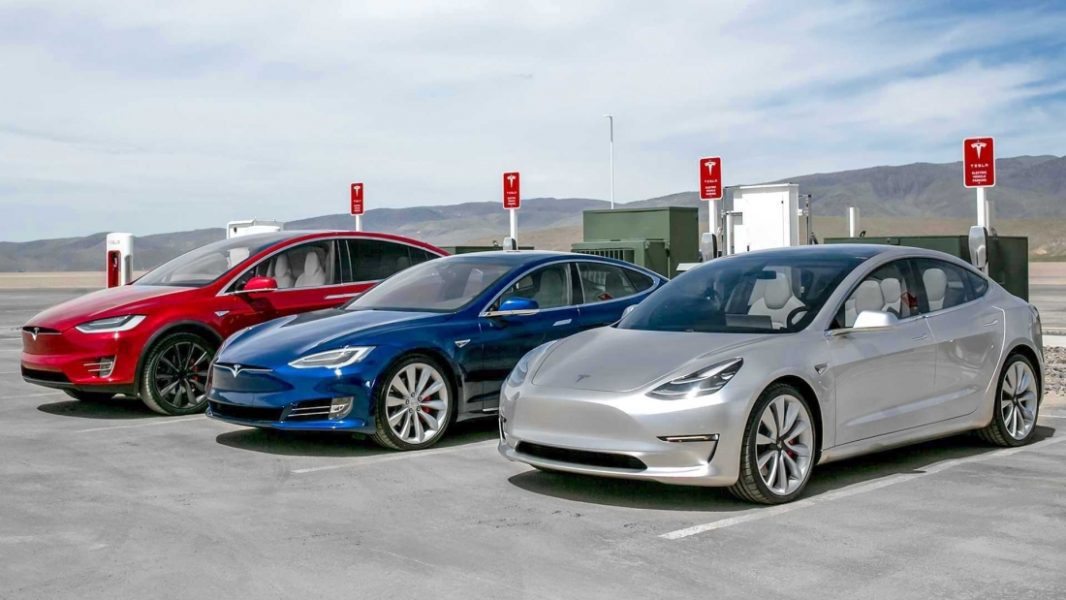