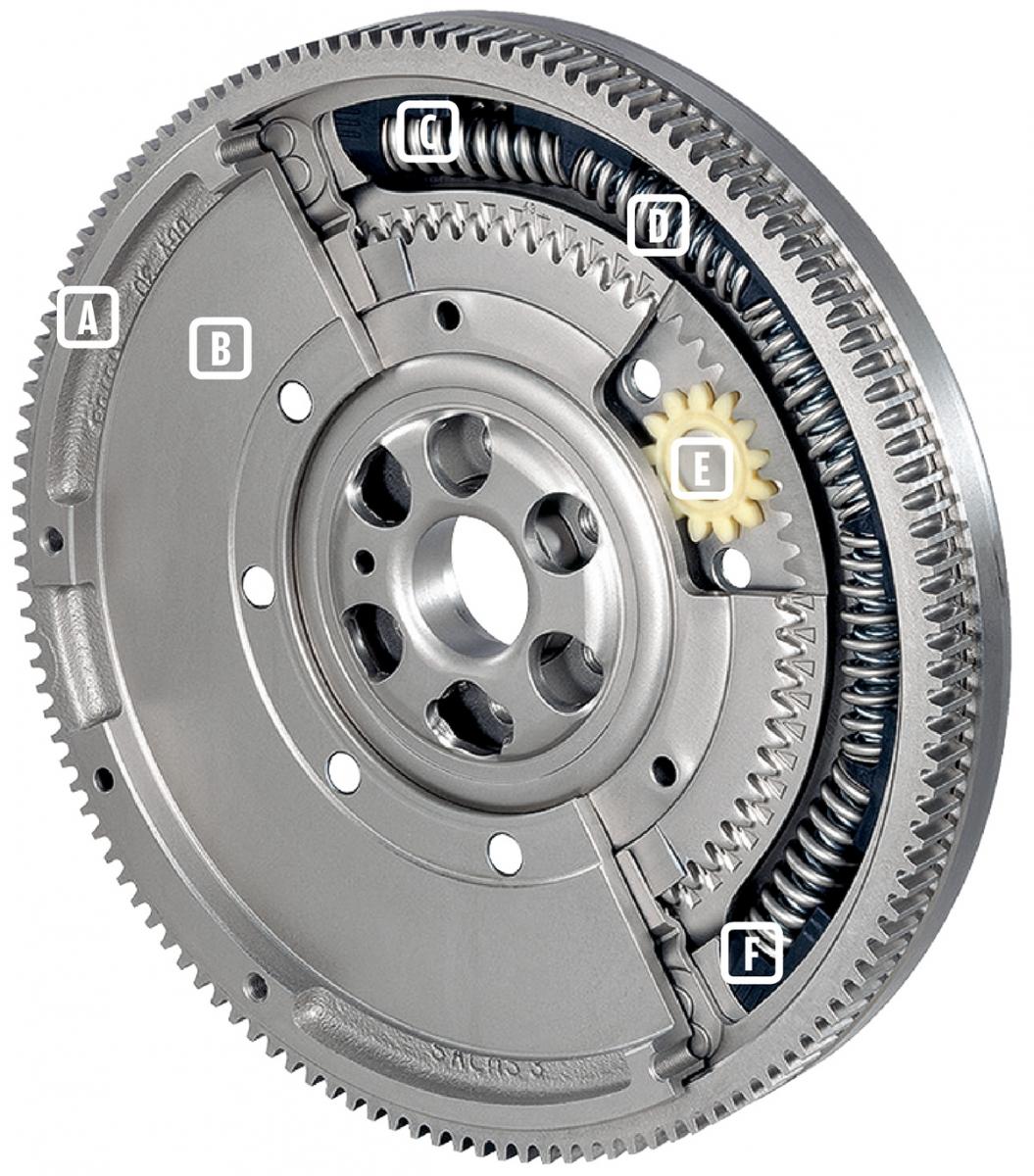
Two-mass flywheel
The internal combustion engine is far from perfect, and coupling it to the gearbox with a clutch creates additional problems that designers have been trying to solve for years. And it must be admitted that they are doing it more and more effectively.
Changes in the acceleration of the pistons, resulting from both the addition or admission of gas by the driver, and the misfire itself, as well as changes in the direction of movement of the pistons, cause changes in the engine speed. . This in turn causes vibrations that are transmitted from the crankshaft through the flywheel, clutch and shaft to the gearbox. There they contribute to the gear teeth. The noise that accompanies this is known as a rattling noise. Vibration from the engine also causes body shaking. All together reduces the comfort of travel.
The phenomenon of transmission of vibrations from the crankshaft to the successive elements of the drive system is resonant in nature. This means that the intensity of these oscillations occurs in a certain range of rotational speed. It all depends on the rotating masses of the motor and gearbox, or rather on their moments of inertia. The greater the moment of inertia of the rotating masses of the gearbox, the lower the speed at which an undesirable resonance phenomenon occurs. Unfortunately, in a classic transmission solution, a much larger proportion of the rotating masses is on the engine side.
Silencer in shield
Despite such difficulties, designers have long found a way to prevent the free transmission of vibrations from the engine to the transmission. To do this, the clutch disc is equipped with a torsional vibration damper. It consists of torsion and friction elements. The former include the drive disk and the counter disk, as well as helical springs located in the corresponding cutouts in the disk body. By varying the size of the cutouts and springs, different vibration damping characteristics can be achieved. The purpose of the friction elements is to prevent excessive swinging of the vibration damper. The required coefficient of friction between the working surfaces is achieved by using friction rings made, for example, from a suitable plastic.
The vibration damper in the clutch disc has undergone various upgrades over the years. At present, incl. two-stage vibration damper with separate pre-damper and two-stage vibration damper with integrated pre-damper and variable friction.
Vibration damping on the clutch disc is not fully effective. Resonance and accompanying noise occur in the idle speed range or slightly higher. To get rid of it, you should correspondingly increase the moment of inertia of the moving parts of the gearbox with the help of an additional flywheel placed on the gear shaft. However, such a solution would cause significant shifting problems as synchronization would be required due to the additional rotating mass of this high inertia wheel.
Two-mass flywheel
A much better solution would be to divide the mass of the flywheel into two parts. One is rigidly connected to the crankshaft, the other is connected to the rotating parts of the gearbox through the clutch disc. Thus, a dual-mass flywheel was created, thanks to which, without increasing the total mass of the flywheel, on the one hand, an increase in the moments of inertia of the rotating masses of the transmission was achieved, and on the other, a decrease in the moment of inertia of the rotating parts of the engine. As a result, this resulted in almost equal moments of inertia on both sides. The position of the vibration damper was also changed, which was moved from the clutch disc between the parts of the flywheel. This allows the damper to work at steering angles up to 60 degrees (at the clutch disc it is below 20 degrees).
The use of a dual-mass flywheel made it possible to shift the range of resonant oscillations below the idle speed, and therefore beyond the operating range of the engine. In addition to eliminating resonant vibrations and the accompanying characteristic transmission noise, the dual-mass flywheel also makes shifting easier and increases the life of the synchronizers. It also allows a few percent (about 5) to reduce fuel consumption.
For lower grades
The transverse mounting of the engine and limited space in the engine compartment make the use of a dual-mass flywheel instead of a traditional one either difficult or even impossible. DFC (Damped Flywheel Clutch), developed by LuK, allows you to use the advantages of a dual-mass flywheel in small and medium-sized vehicles. The combination of flywheel, pressure plate and clutch disc in one unit makes the DFC clutch as spacious as a classic clutch. In addition, DFC clutch assembly does not require centering of the clutch disc.
Requirements, durability and cost
A special dual-mass flywheel is designed for a specific engine and gearbox. For this reason, it cannot be installed on any other type of vehicle. If this happens, not only will the noise of the transmission increase, but the flywheel itself may also be destroyed. Manufacturers also prohibit disassembling the dual-mass flywheel into parts. Any treatment for the repair of rubbing surfaces, any "modification" of the wheel is also unacceptable.
When it comes to the durability of a dual mass flywheel, it's a tricky business, as how well it lasts depends on many factors, including engine condition, driving style and type. However, there are opinions that it should last at least as long as the clutch disc. There are also such technological recommendations that, along with the clutch kit, the dual-mass flywheel should also be replaced. This, of course, increases the cost of replacement, because a two-mass wheel is not cheap. For example, in a BMW E90 320d (163 km) the price of the original mass produced wheel is PLN 3738, while its replacement costs PLN 1423.
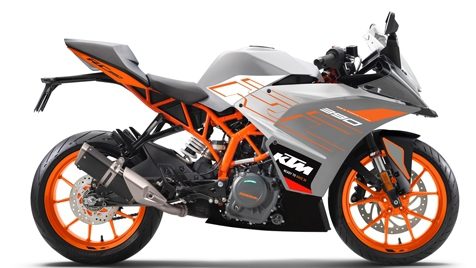
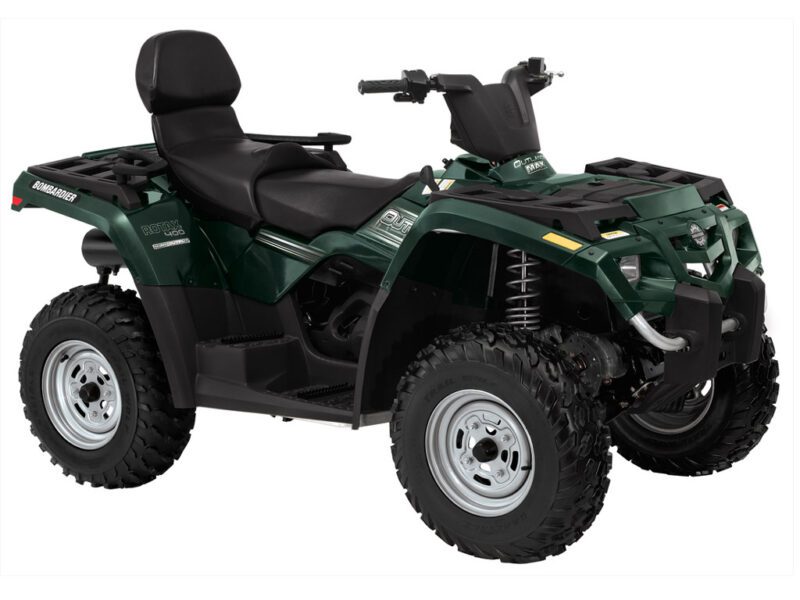