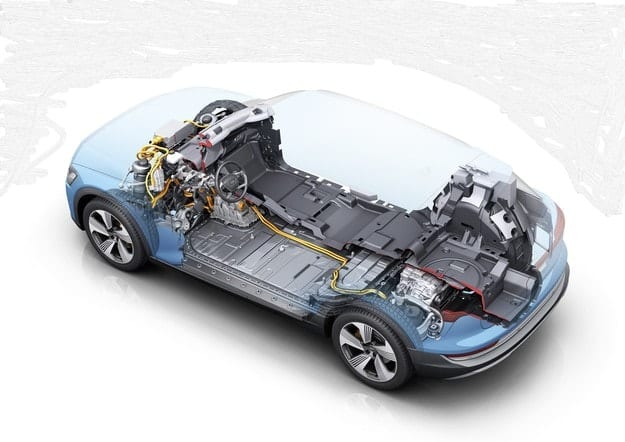
Electric car yesterday, today and tomorrow: part 2
Content
Separate platforms or retrofit solutions for electric vehicles
Is the creation and implementation of all-electric platforms economically viable? Answer: it depends. Back in 2010, the Chevrolet Volt (Opel Ampera) showed that there are ways to optimally cost-effectively convert the body structure for a conventional mover by integrating the battery pack into the central tunnel of the Delta II platform, where the exhaust system is located. ) and under the rear seat of the car. However, from today's point of view, Volt is a hybrid plug-in (despite a very sophisticated technology similar to that used in the Toyota Prius) with a 16 kWh battery and an internal combustion engine. Ten years ago, it was proposed by the company as an electric car with increased mileage, and this is very indicative of the way this type of car went over this decade.
For Volkswagen and its divisions, whose ambitious plans include the production of one million electric vehicles a year, by 2025 the creation of platforms specifically designed for electric vehicles is justified. However, for manufacturers such as BMW, the matter is much more complicated. After the badly scalded i3, which was at the forefront but created at a different time and therefore never became economically viable, the responsible factors at the Bavarian company decided that designers should look for a way to create flexible platforms that could maximize the efficiency of both drive types. Unfortunately, traditionally adapted electrical platforms are really a design compromise - the cells are packaged in separate packages and placed where there is room, and in newer designs these volumes are provided for such integrations.
However, this space is not used as efficiently as when using cells built into the floor, and the elements are connected by cables, which increase weight and resistance. The current electric models of most companies, such as the e-Golf and Mercedes' electric B-class, are just that. Therefore, BMW will use optimized versions of the CLAR platform on which the upcoming iX3 and i4 will be based. Mercedes will have a similar approach in the coming years, using modified versions of its current platforms before introducing (about two years later) the dedicated EVA II. For its first electric models, notably the e-Tron, Audi used a modified version of its regular MLB Evo that changed the entire wheelbase to integrate a full battery pack. However, Porsche and Audi are currently developing a Premium Platform Electric (PPE) specifically designed for electric propulsion that will also be used by Bentley. However, even the new generation of dedicated EV platforms will not seek the avant-garde approach of the i3, which will mainly use steel and aluminum for this purpose.
And so everyone is looking for their own new path in the jungle of the near future. Fiat sold the electric version of the Panda 30 years ago, but FiatChrysler is now lagging behind the trend. The Fiat 500e version and the Chrysler Pacifica plug-in version are currently on sale in the United States. The company's business plan calls for an investment of € 9 billion in electrified models by 2022, and will soon begin production of 500 electric vehicles in Europe using a new electrified platform. Maserati and Alfa Romeo will also have electrified models.
By 2022, Ford is to launch 16 electric vehicles on the MEB platform in Europe; Honda will use electrified powertrains to bring two-thirds of its models in Europe by 2025; Hyundai has been selling electric versions of the Kona and Ioniq well, but is now ready with an all-new EV platform. Toyota will base its future electric models on an e-TNGA built specifically for electric vehicles, which will also be used by Mazda, and while the name is the same as a number of new TNGA solutions, it is strictly specific. Toyota has a lot of experience with electric cars and power management, but not with lithium-ion batteries because, in the name of reliability, it has used nickel-metal hydride batteries to the end. Renault-Nissan-Mitsubishi is using adapted existing designs for most of its electric models, but will soon also launch a new electric platform, the CMF-EV. The CMF name shouldn't fool you - as with Toyota and TNGA, the CMF-EV has almost nothing to do with the CMF. PSA models will use versions of the CMP and EMP2 platforms. The platform of one of the pioneers of new electric mobility Jaguar I-Pace is also fully electric.
How will the production go?
Assembling a car at a factory is 15 percent of the total production process. The remaining 85 percent includes the production of each of more than ten thousand parts and their pre-assembly in approximately 100 of the most important production units, which are then sent to the production line. Today, cars are characterized by an extremely high degree of complexity, and the specificity of their components does not allow them to be fully produced in an automobile company. This applies even to manufacturers such as Daimler, who have a higher degree of integration and self-production of components such as gearboxes. The days in which the company was manufactured to the smallest detail, such as the Ford Model T, are long gone. Maybe because there are not many details in the model T ...
However, the strong impetus for the development of electric vehicles in recent years poses completely new challenges for manufacturers of conventional cars. No matter how flexible the production process, it mainly includes models of assembly systems with conventional bodies, powertrains and powertrains. These include plug-in hybrid models that do not differ significantly in layout, with the exception of adding a battery and power electronics to a convenient place on the case. This is true even for electric vehicles based on traditional designs.
The construction of cars, including electric ones, occurs simultaneously with the design of production processes in which each of the automobile companies chooses its own approach to action. This is not about Tesla, whose production is built almost from scratch on the basis of electric vehicles, but about recognized manufacturers, which, depending on needs, must combine the production of cars with conventional and electric drives. And since no one knows exactly what will happen in the short term, everything should be flexible enough.
New production systems ...
For most manufacturers, the solution is to adapt the production lines to the installation of electric vehicles. GM, for example, produces a hybrid volt and an electric bolt in existing plants. Their former PSA friends say they will design their cars so that they can use the same approach.
Daimler’s work to develop electric vehicles under the new EQ brand and adapt plants is based on an estimate of 15 to 25 percent of Mercedes-Benz sales by 2025. To be ready for such With the development of the market, including taking into account this rather wide range of forecasts, the company expands its factory in Sindelfingen with a factory called Factory 56. Mercedes defines this factory as “the first factory of the future” and it will include all technological solutions . Anya and systems are called. Industry 4.0. Like the PSA factory in Tremere, this factory and the Daimler Full-Flex factory in Kecskemét will be able to produce electric cars along with conventional ones. The production is also flexible at Toyota, which will produce its electric cars in Motomachi, Toyota City. For decades, the company has raised the efficiency of production processes to a cult, but in the short term does not have excessively ambitious intentions as a competitor and VW on purely electric cars.
... Or brand new factories
Not all manufacturers choose this flexible approach. Volkswagen, for example, is investing one billion euros in its plant in Zwickau, designing it only for the production of electric vehicles. The company is preparing a number of them, including models of various brands in the concern, which will be based on the completely new modular architecture MEB (Modularer E-Antriebs-Baukasten). The production plant that VW is preparing will be able to handle large volumes, and the company's ambitious large-scale plans are at the heart of this decision.
The slow movement in this direction has its own logical explanation - established car manufacturers follow well-established, consistent patterns of car building and production processes. Growth must be steady, without crashes, like Tesla. In addition, high quality criteria require many procedures and this takes time. Electric mobility is a chance for Chinese companies to expand into international markets more broadly, but they also need to start producing reliable and, above all, safe vehicles first.
In fact, building platforms and organizing production processes are less of a problem for automakers. In this regard, they have much more experience than Tesla. The design and manufacture of a purely electrically driven platform is less complex than conventionally driven vehicles - for example, the latter's lower structure has many more bends and connections that require a more complex and costly manufacturing process. Companies have a lot of experience in adapting such products and this will not be a problem for them, especially since they have gained a lot of experience with multi-material construction. It is true that the adaptation of processes takes time, but the most modern production lines are very flexible in this regard. A significant problem of electric vehicles remains the way of storing energy, that is, the battery.
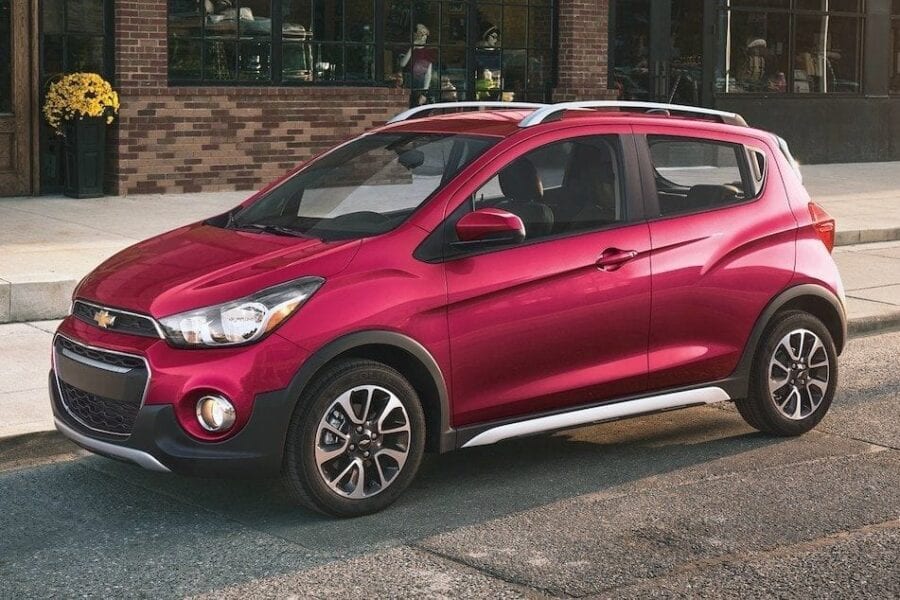
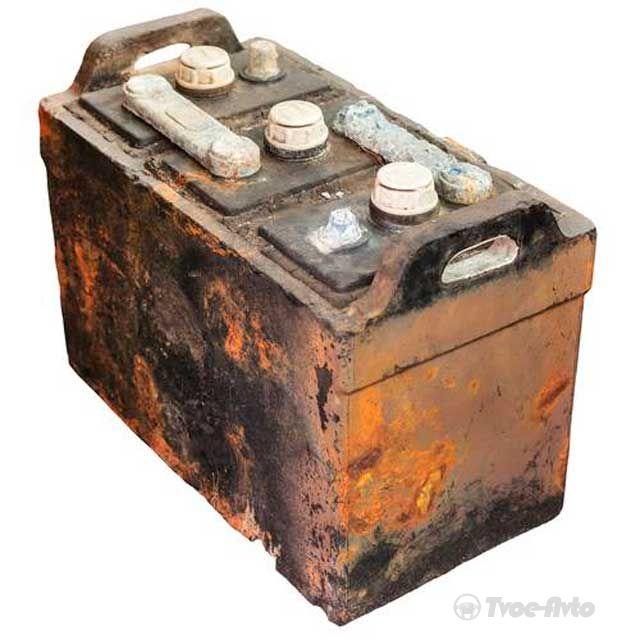