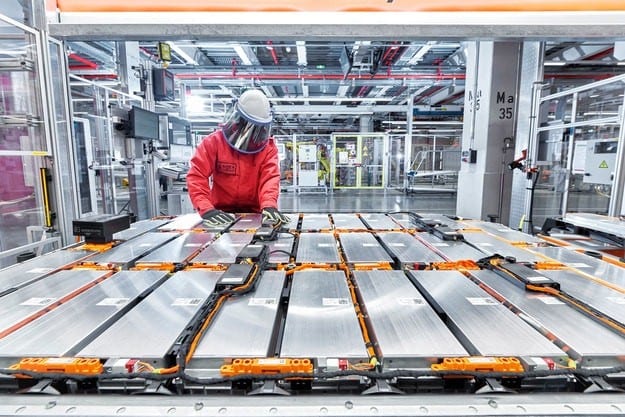
Electric car yesterday, today, tomorrow: part 3
Content
The term "lithium-ion batteries" hides a wide variety of technologies.
One thing is for sure – as long as lithium-ion electrochemistry remains unchanged in this regard. No other electrochemical energy storage technology can compete with lithium-ion. The point, however, is that there are different designs that use different materials for the cathode, anode and electrolyte, each of which has different advantages in terms of durability (the number of charge and discharge cycles up to an allowable residual capacity for electric vehicles of 80%), specific power kWh/kg, price euro/kg or power to power ratio.
Back in Time
The possibility of carrying out electrochemical processes in the so-called. Lithium-ion cells come from the separation of lithium protons and electrons from the lithium junction at the cathode during charging. The lithium atom easily donates one of its three electrons, but for the same reason it is highly reactive and must be isolated from air and water. In the voltage source, the electrons begin to move along their circuit, and the ions are directed to the carbon-lithium anode and, passing through the membrane, are connected to it. During the discharge, the reverse movement occurs - the ions return to the cathode, and the electrons, in turn, pass through the external electrical load. However, rapid high-current charging and full discharge results in the formation of new durable connections, which reduces or even stops the battery's function. The idea behind using lithium as a particle donor stems from the fact that it is the lightest metal and can easily release protons and electrons under the right conditions. However, scientists are rapidly abandoning the use of pure lithium due to its high volatility, its ability to bond with air, and for safety reasons.
The first lithium-ion battery was created in the 1970s by Michael Whittingham, who used pure lithium and titanium sulfide as electrodes. This electrochemistry is no longer used, but actually lays the foundation for lithium-ion batteries. In the 1970s, Samar Basu demonstrated the ability to absorb lithium ions from graphite, but, thanks to the experience of that time, batteries quickly self-destructed when charging and discharging. Intensive development began in the 1980s to find suitable lithium compounds for the cathode and anode of batteries, and a real breakthrough occurred in 1991.
NCA, NCM lithium cells ... what does it really mean?
After experimenting with various lithium compounds in 1991, the efforts of scientists were crowned with success - Sony began mass production of lithium-ion batteries. Currently, batteries of this type have the highest output power and energy density, and most importantly, a significant potential for development. Depending on battery requirements, companies are turning to various lithium compounds as the cathode material. These are lithium cobalt oxide (LCO), compounds with nickel, cobalt and aluminum (NCA) or with nickel, cobalt and manganese (NCM), lithium iron phosphate (LFP), lithium manganese spinel (LMS), lithium titanium oxide (LTO) and others. The electrolyte is a mixture of lithium salts and organic solvents and is especially important for the "mobility" of lithium ions, and the separator, which is responsible for preventing short circuits by being permeable to lithium ions, is usually polyethylene or polypropylene.
Output power, capacity, or both
The most important battery characteristics are specific energy, reliability and safety. Currently produced batteries cover a wide range of these qualities and, depending on the materials used, have a specific energy range from 100 to 265 W / kg (and an energy density of 400 to 700 W / l). The best in this regard are NCA batteries and the worst LFPs. However, the material is one side of the coin. To increase both specific energy and energy density, various nanostructures are used to absorb more material and provide a higher conductivity of the ion flux. A large number of ions "stored" in a stable compound, and conductivity are prerequisites for faster charging, and development is directed in these directions. At the same time, the design of the battery should provide the necessary ratio of power to capacity, depending on the type of drive. For example, plug-in hybrids must have a much higher power to capacity ratio for obvious reasons. Today's developments are focused on batteries of the type NCA (LiNiCoAlO2 with a cathode and a graphite anode) and NMC 811 (LiNiMnCoO2 with a cathode and a graphite anode). The former contain (outside lithium) about 80% nickel, 15% cobalt and 5% aluminum and have a specific energy of 200-250 W / kg, which means that they have a relatively limited use of critical cobalt and a service life of up to 1500 cycles. Such batteries will be produced by Tesla at its Gigafactory in Nevada. When it reaches the planned full capacity (in 2020 or 2021, depending on the situation), the plant will produce 35 GWh of batteries, which is enough to equip 500 cars. This will further reduce battery costs.
NMC 811 batteries have a slightly lower specific energy (140-200W/kg) but have a longer life, reaching 2000 full cycles, and are 80% nickel, 10% manganese and 10% cobalt. Currently, all battery manufacturers use one of these two types. The only exception is the Chinese company BYD, which makes LFP batteries. Cars equipped with them are heavier, but they do not need cobalt. NCA batteries are preferred for electric vehicles and NMC for plug-in hybrids due to their respective advantages in terms of energy density and power density. Examples are the electric e-Golf with a power/capacity ratio of 2,8 and the plug-in hybrid Golf GTE with a ratio of 8,5. In the name of lowering the price, VW intends to use the same cells for all types of batteries. And one more thing - the larger the capacity of the battery, the less the number of full discharges and charges, and this increases its service life, therefore - the larger the battery, the better. The second concerns hybrids as a problem.
Market trends
At present, the demand for batteries for transportation purposes already exceeds the demand for electronic products. It is still projected that 2020 million electric vehicles per year will be sold globally by 1,5, which will help drive down the cost of batteries. In 2010, the price of 1 kWh of a lithium-ion cell was about 900 euros, and now it is less than 200 euros. 25% of the cost of the entire battery is for the cathode, 8% for the anode, separator and electrolyte, 16% for all other battery cells and 35% for the overall battery design. In other words, lithium-ion cells contribute 65 percent to the cost of a battery. Estimated Tesla prices for 2020 when Gigafactory 1 enters service are around 300€/kWh for NCA batteries and the price includes the finished product with some average VAT and warranty. Still a fairly high price, which will continue to decline over time.
The main reserves of lithium are in Argentina, Bolivia, Chile, China, the USA, Australia, Canada, Russia, Congo and Serbia, with the vast majority currently being extracted from dried lakes. With the accumulation of an increasing number of batteries, the market for materials recycled from old batteries will increase. However, more important is the problem of cobalt, which, although present in large quantities, is mined as a by-product in the production of nickel and copper. Although cobalt is low in soil, it is mined in the Congo (which has the largest available reserves), but under conditions that challenge ethics, morality, and environmental protection.
Hi-tech
It should be borne in mind that the technologies adopted as a prospect for the near future, in fact, are not fundamentally new, but are lithium-ion options. Such, for example, are solid state batteries, in which a solid electrolyte (or gel in lithium polymer batteries) is used instead of liquid. This solution provides a more stable design of the electrodes, which violates their integrity when charging with high current, respectively. high temperature and high load. This can increase charging current, electrode density and capacitance. Solid state batteries are still at a very early stage of development, and they are unlikely to appear in mass production until the middle of the decade.
One of the award-winning startups at the 2017 BMW Innovation Technology Competition in Amsterdam was a battery-powered company whose silicon anode increases energy density. Engineers are working on various nanotechnologies to provide greater density and strength to the material of both the anode and cathode, and one solution is to use graphene. These microscopic layers of graphite with a single atom thickness and a hexagonal atomic structure are one of the most promising materials. The "graphene balls" developed by the battery cell manufacturer Samsung SDI, integrated into the cathode and anode structure, provide higher strength, permeability and density of the material and a corresponding increase in capacity of about 45% and five times faster charging time. These technologies can receive the strongest impulse from Formula E cars, which may be the first to be equipped with such batteries.
Players at this stage
The main players as Tier 123 and Tier 2020 suppliers, i.e. cell and battery manufacturers, are Japan (Panasonic, Sony, GS Yuasa and Hitachi Vehicle Energy), Korea (LG Chem, Samsung, Kokam and SK Innovation), China (BYD Company ). , ATL and Lishen) and the USA (Tesla, Johnson Controls, A30 Systems, EnerDel and Valence Technology). The main suppliers of cell phones are currently LG Chem, Panasonic, Samsung SDI (Korea), AESC (Japan), BYD (China) and CATL (China), which have a market share of two-thirds. At this stage in Europe, they are only opposed by BMZ Group from Germany and Northvolth from Sweden. With the launch of Tesla's Gigafactory in XNUMX, this proportion will change - the American company will account for XNUMX% of the world's production of lithium-ion cells. Companies such as Daimler and BMW have already signed contracts with some of these companies, such as CATL, which is building a plant in Europe.
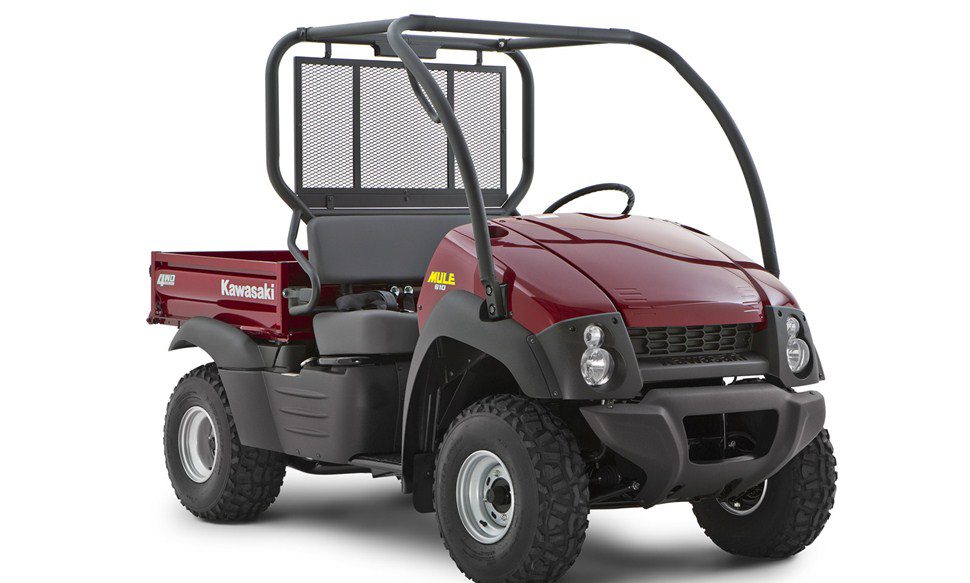
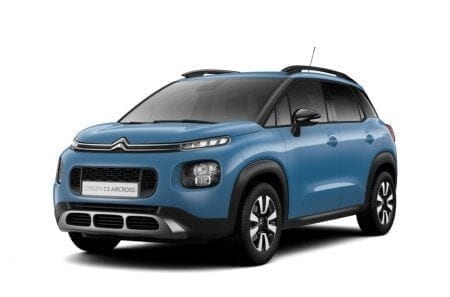