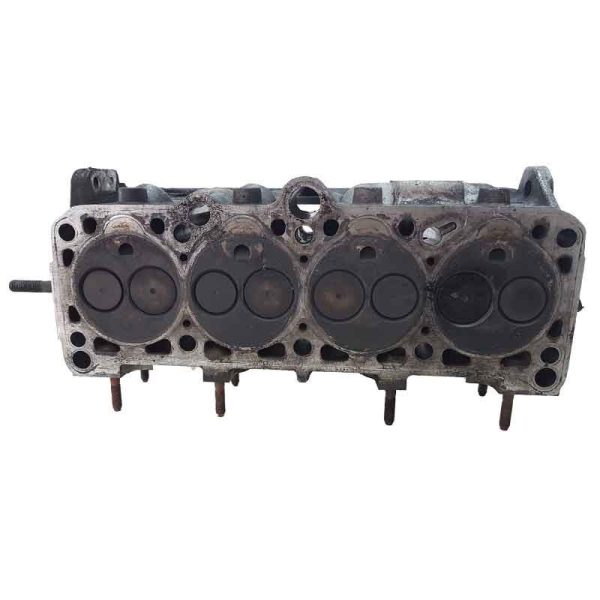
Internal combustion engine cylinder head
Content
- Cylinder head functions
- Division of cylinder heads
- Cylinder head gasket
- Cylinder head cover
- The main characteristics of the cylinder head of a two-stroke engine
- Main characteristics of the cylinder head of a four-stroke engine
- The combustion chamber
- Inlet and outlet
- Valve guides
- Valves in the cylinder head of the engine
- Two-valve cylinder head
- Three-valve cylinder head
- Four-valve cylinder head
- Five-valve cylinder head
The term "cylinder head" did not come about by chance. As in the human head, the most complex and important actions of an internal combustion engine take place in the cylinder head. The cylinder head is thus part of the internal combustion engine, located in its upper (upper) part. It is intertwined with the air ducts of the intake and exhaust tracts, contains parts of the valve mechanism, injectors and spark plugs or glow plugs. The cylinder head covers the top of the cylinder block. The head can be one for the entire engine, separately for each cylinder or separately for a separate row of cylinders (V-shaped engine). Fastened to the cylinder block with screws or bolts.
Cylinder head functions
- It forms the combustion space - it forms the compression space or part of it.
- Provides cylinder charge replacement (4-stroke engine).
- Provides cooling for the combustion chamber, spark plugs and valves.
- Closes the combustion chamber gas-tight and waterproof.
- Provides for the placement of the spark plug or injector.
- Captures and directs combustion pressure - high voltage.
Division of cylinder heads
- Cylinder heads for two-stroke and four-stroke engines.
- Cylinder heads for spark ignition and compression ignition engines.
- Air cooled or water cooled heads.
- Separate heads for one cylinder, head for in-line or V-shaped engine.
- Cylinder head and valve timing.
Cylinder head gasket
There is a seal between the cylinder head and the cylinder block that seals the combustion chamber hermetically and prevents oil and coolant from escaping (mixing). We divide seals into the so-called metal and combined.
Metal, ie copper or aluminum seals, are used in small, high-speed, air-cooled engines (scooters, two-stroke motorcycles up to 250 cc). Water-cooled engines use a seal that consists of graphite-rich organic fibers bonded on a plastics base supported on a metal support.
Cylinder head cover
An important part of the cylinder head is also a cover that covers the valve train and prevents oil from leaking into the engine environment.
The main characteristics of the cylinder head of a two-stroke engine
The cylinder head for two-stroke engines is usually simple, air-cooled (finned on the surface) or liquid. The combustion chamber can be symmetrical, biconvex or round, often with an anti-knock gap. The spark plug thread is located on the cylinder axis. It can be made from gray cast iron (old engine designs) or aluminum alloy (currently used). The connection of the two-stroke engine head to the cylinder block can be threaded, flanged, coupled with tightening screws, or even a one-piece head.
Main characteristics of the cylinder head of a four-stroke engine
The design of the head for four-stroke engines must also provide a change in the displacement of the engine cylinders. It contains inlet and outlet channels, parts of the gas distribution mechanism that control the valves, the valves themselves, together with their seats and guides, threads for fixing the spark plug and nozzles, channels for the flow of lubricating and cooling media. It is also part of the combustion chamber. Therefore, it is disproportionately more complex in design and shape compared to the cylinder head of a two-stroke engine. The cylinder head of a four-stroke engine is made from either gray fine-grained cast iron, or alloyed cast iron, or forged steel - so-called cast steel or aluminum alloys for liquid-cooled engines. Air-cooled engines use aluminum alloys or cast iron. Cast iron is almost never used as a head material and has been replaced by aluminum alloy. The decisive aspect of the production of light metals is not so much the low weight as the excellent thermal conductivity. Since the combustion process takes place in the cylinder head, resulting in intense heat in this part of the engine, the heat must be transferred to the coolant as soon as possible. And then aluminum alloy is a very suitable material.
The combustion chamber
The combustion chamber is also a very important part of the cylinder head. It must be of the correct shape. The main requirements for a combustion chamber are:
- Compactness that limits heat loss.
- Allow the use of the maximum number of valves or a sufficient valve size.
- Optimal opening of the cylinder filling.
- Place the candle in the richest place at the end of the squeeze.
- Prevention of detonation ignition.
- Suppression of hotspots.
These requirements are very important because the combustion chamber influences the formation of hydrocarbons, determines the course of combustion, fuel consumption, combustion noise and torque. The combustion chamber also determines the maximum compression ratio and influences the heat loss.
Combustion chamber shapes
a - bath, b - hemispherical, c – wedge, d – Asymmetric hemispherical, e - Herons in the piston
Inlet and outlet
Both the inlet and outlet ports end with a valve seat either directly in the cylinder head or with an inserted seat. A straight valve seat is formed directly in the head material or can be so called. in-line saddle made of high quality alloy materials. The contact surfaces are precisely ground to size. The bevel angle of the valve seat is most often 45 °, since this value achieves good tightness when the valve is closed and the seat is self-cleaning. Suction valves are sometimes tilted at 30 ° for better flow in the seat area.
Valve guides
The valves move in the valve guides. The valve guides can be made from cast iron, aluminum-bronze alloy, or made directly in the cylinder head material.
Valves in the cylinder head of the engine
They move in guides, and the valves themselves rest on the seats. The valve as part of the control valve for reciprocating internal combustion engines is subjected to mechanical and thermal stress during operation. From a mechanical point of view, it is most of all loaded with the pressure of the flue gases in the combustion chamber, as well as the control force directed from the cam (jack), the inertial force during the reciprocating movement, as well as mechanical friction. myself. Thermal stress is equally important, since the valve is mainly influenced by the temperature in the combustion chamber as well as the temperature around the flowing hot flue gases (exhaust valves). It is the exhaust valves, especially in supercharged engines, that are exposed to extreme thermal loads, and the local temperature can reach 900 ° C. Heat can be transferred to the seat with the valve closed and to the valve stem. Heat transfer from the head to the stem can be increased by filling the cavity inside the valve with a suitable material. Most often, liquefied sodium gas is used, which fills the stem cavity only halfway, so that when the valve moves, the inner part is intensively flushed with liquid. The stem cavity in smaller (passenger) engines is made by drilling a hole; in the case of larger engines, part of the valve head may also be hollow. The valve stem is usually chrome plated. Thus, the heat load is not the same for different valves, it also depends on the combustion process itself and causes thermal stresses in the valve.
Inlet valve heads are usually larger in diameter than exhaust valves. With an odd number of valves (3, 5), there are more intake valves per cylinder than exhaust valves. This is due to the requirement to achieve the maximum possible - optimal specific power and, therefore, the best possible filling of the cylinder with a combustible mixture of fuel and air.
For the production of suction valves, steels with a pearlite structure, alloyed with silicon, nickel, tungsten, etc. are mainly used. Sometimes a titanium alloy is used. Exhaust valves exposed to thermal stress are made from high alloyed (chromium-nickel) steels with austenitic structure. Hardened tool steel or other special material is welded to the seat of the seat. stellite (malleable alloy of cobalt with chromium, carbon, tungsten or other elements).
Two-valve cylinder head
Three-valve cylinder head
Four-valve cylinder head
Five-valve cylinder head
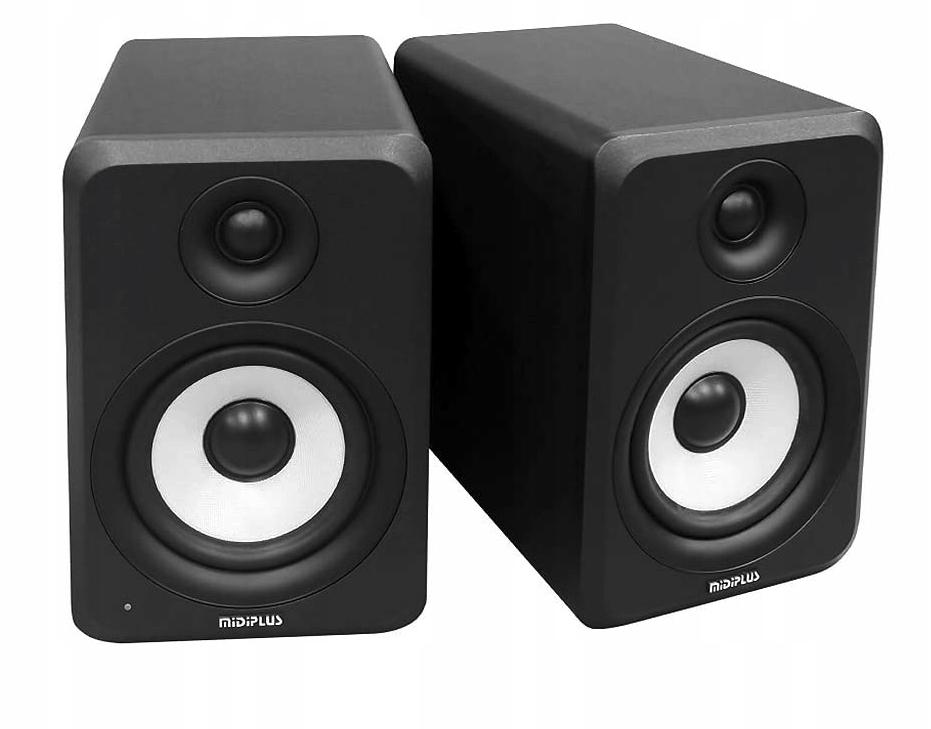
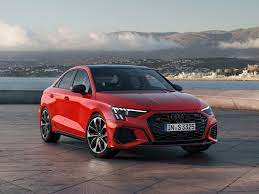