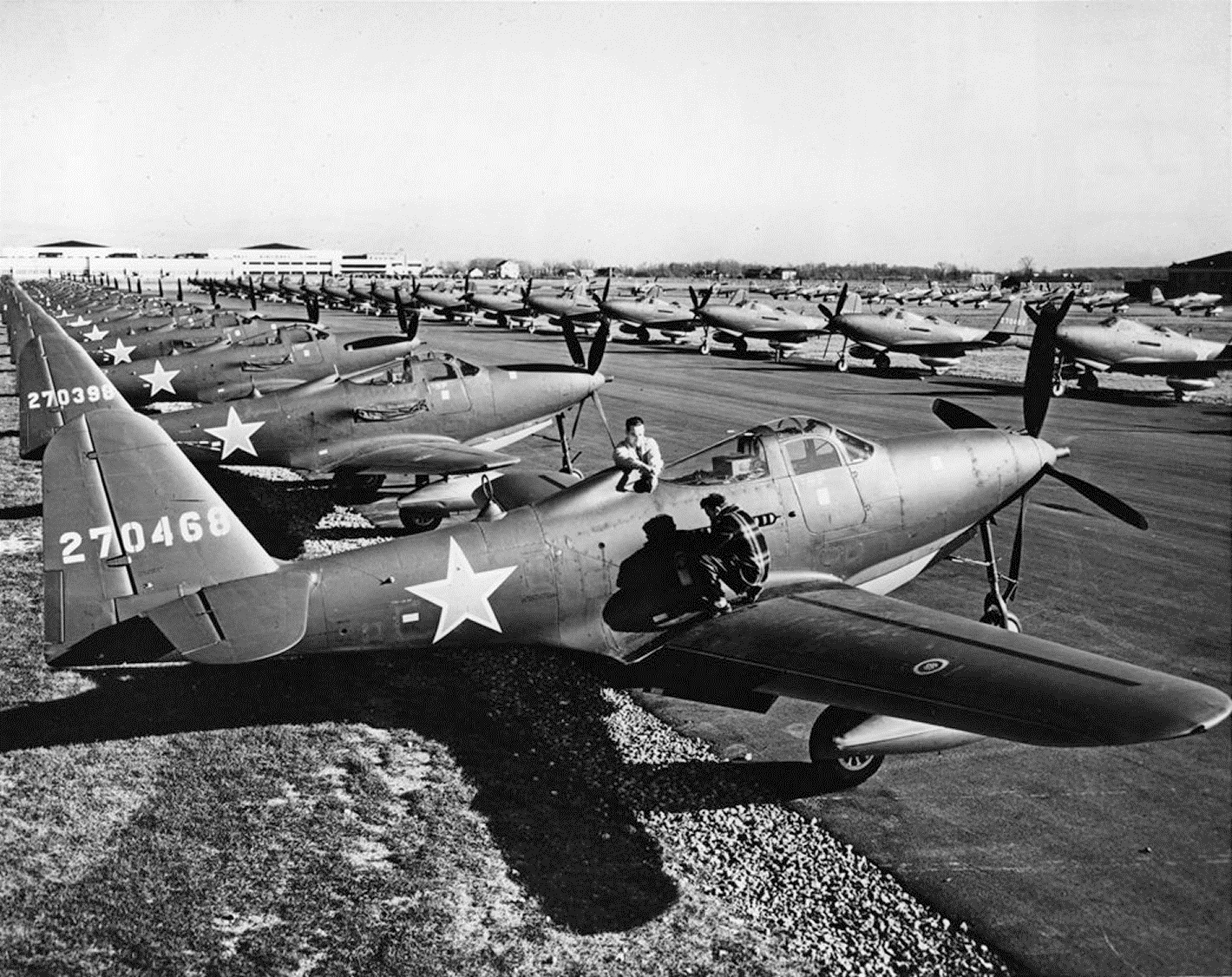
Fighter Bell P-63 Kingcobra
Bell P-63A-9 (42-69644) in one of the test flights. The king cobra attracted little interest from the US Air Force, but was produced in large numbers in the first place.
for the Soviet Union.
The Bell P-63 Kingcobra was the second American laminar wing fighter after the Mustang and the only American single-seat fighter aircraft to fly in prototype form after the Japanese attack on Pearl Harbor, and went into mass production during the war. Although the R-63 did not arouse much interest in the US Air Force, it was produced in large quantities for the needs of the allies, primarily the USSR. After World War II, Kingcobras were also used in combat by the French air force.
In late 1940, Air Corps logisticians in Wright Field, Ohio, began to believe that the P-39 Airacobra would not make a good high-altitude high-performance interceptor. A radical improvement in the situation could only bring the use of a more powerful engine and a reduction in aerodynamic drag. The choice fell on the Continental V-12-1430 1-cylinder in-line liquid-cooled V-engine with a maximum power of 1600-1700 hp. In previous years, the United States Air Force (USAAC) invested heavily in its development, seeing it as an alternative to the Allison V-1710 engine. That same year, the National Advisory Committee for Aeronautics (NACA) made a so-called laminar airfoil based on research done at the Langley Memorial Aviation Laboratory (LMAL) by UCLA graduate Eastman Nixon Jacobs. The new profile was characterized by the fact that its maximum thickness ranged from 40 to 60 percent. chords (conventional profiles have a maximum thickness of no more than 25% of the chord). This allowed for laminar (undisturbed) flow over a much larger wing area, which in turn resulted in much less aerodynamic drag. Designers and military personnel hoped that the combination of a powerful engine with an aerodynamically improved airframe would lead to the creation of a successful interceptor.
In mid-February 1941, the designers of the Bell Aircraft Corporation met with representatives of the materiel department to discuss the possibility of building a new fighter. Bell submitted two proposals, the Model 23, a modified P-39 with a V-1430-1 engine, and the Model 24, an entirely new laminar wing aircraft. The first one was faster to implement as long as the new engine was available on time. The second required much more time for the research and development phase, but the end result should have been much better. Both proposals caught the attention of the USAAC and led to the development of the XP-39E (mentioned in the P-39 Airacobra article) and the P-63 Kingcobra. On April 1, Bell submitted a detailed specification for the Model 24 to the Materials Department, along with a cost estimate. After almost two months of negotiations, on June 27, Bell was awarded contract number W535-ac-18966 for the construction of two flying Model 24 prototypes, designated XP-63 (serial numbers 41-19511 and 41-19512; XR-631-1) and static and fatigue testing of a ground airframe.
Project
Work on the preliminary design of the Model 24 began at the end of 1940. The technical design of the XP-63 was carried out by Eng. Daniel J. Fabrisi, Jr. The aircraft had a similar silhouette to the P-39, which was the result of maintaining the same design scheme - a cantilever low-wing with a retractable tricycle landing gear with a front wheel, a 37-mm cannon firing through the propeller shaft, an engine near the center of gravity of the structure and the cockpit between the gun and the engine. The design of the airframe was completely new. During the design process, almost all components and structural elements were finalized, so that in the end, the R-39 and R-63 did not have common parts. Compared to the R-39D, the length of the aircraft has increased from 9,19 to 9,97 m, the span of the horizontal tail from 3962 to 4039 mm, the track of the main landing gear from 3454 to 4343 mm, the base landing gear from 3042 mm. up to 3282 mm. Only the maximum width of the fuselage, determined by the width of the engine, remained unchanged and amounted to 883 mm. The cockpit canopy was modified to include a built-in 38 mm thick flat bulletproof glass in the windshield. The vertical tail also had a new shape. The elevators and rudders were covered with canvas, and the ailerons and flaps were covered with metal. Removable panels and access hatches have been enlarged to make it easier for mechanics to access weapons and equipment.
However, the most important innovation was the NACA 66(215)-116/216 laminar airfoil wings. Unlike the wings of the P-39, they had a design based on two beams - the main and auxiliary rear, which served to attach the ailerons and flaps. An increase in the root chord from 2506 to 2540 mm and a span from 10,36 to 11,68 m resulted in an increase in the bearing surface from 19,81 to 23,04 m2. The wings wedged to the fuselage at an angle of 1°18' and had a rise of 3°40'. Instead of crocodile sashes, flaps are used. The 1:2,5 and 1:12 scale models of the wings, tail and entire aircraft have been extensively tested in the NACA LMAL wind tunnels at Langley Field, Virginia and Wright Field. The tests confirmed the correctness of Jacobs' idea and at the same time allowed Bell's designers to refine the design of the ailerons and flaps, as well as the shape of the glycol and oil cooler air intakes.
The main disadvantage of laminar airfoil wings was that, in order to retain their aerodynamic properties, they had to have a very smooth surface, devoid of protrusions and bumps that could disturb the airflow. NACA specialists and designers were concerned about whether the mass production process could accurately reproduce the shape of the profile. To test this, Bell workers made a test pair of the new wings, not knowing what they were for. After testing in the LMAL wind tunnel, it turned out that the wings meet the established standard.
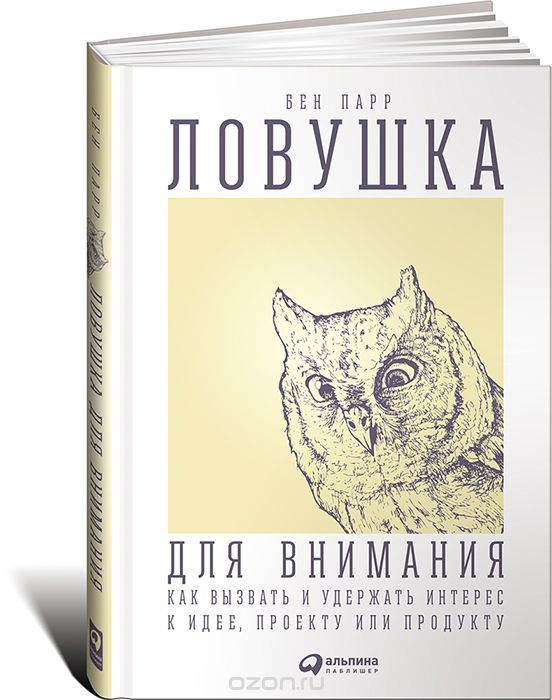
