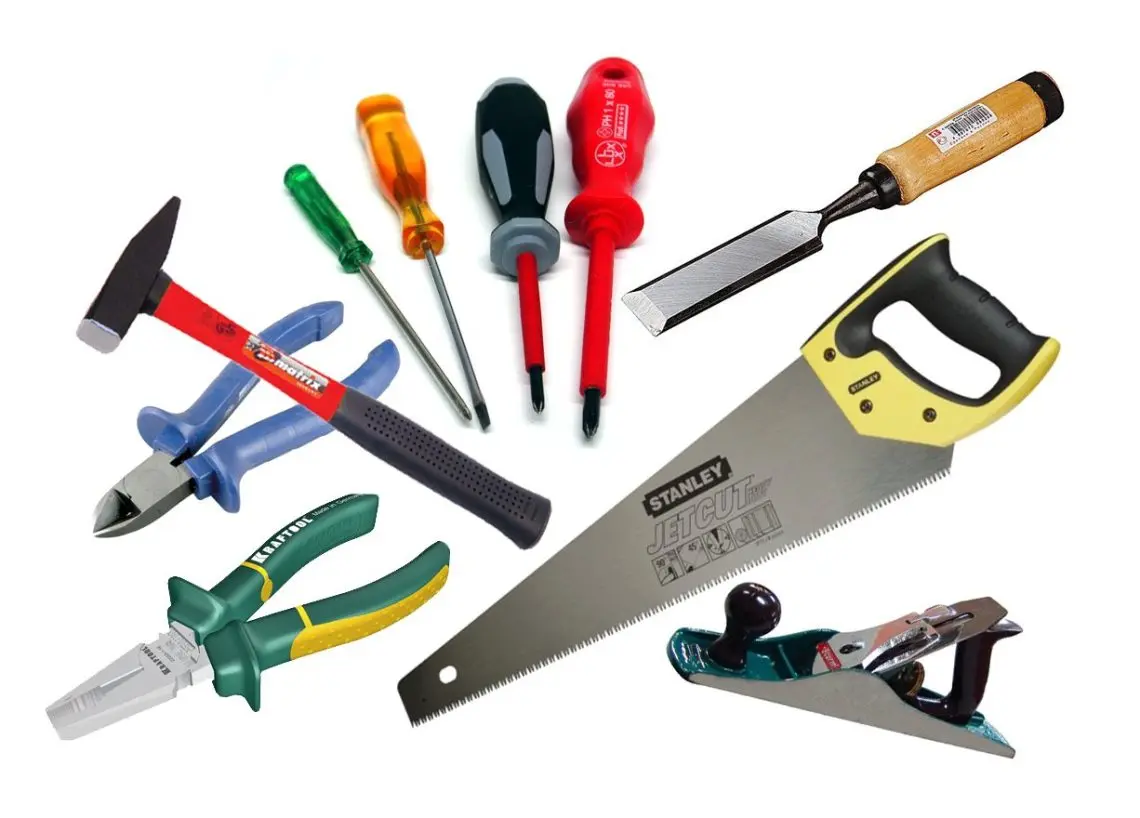
How to Use a Wire Feed Welder (Beginner's Guide)
Content
- How does a wire feed welding machine work?
- What You Need to Know Before Using a Wire Feed Welder
- 10 Step Guide to Using a Wire Feed Welder
- Step 1 - Connect to an electrical outlet
- Step 2: Turn on the gas supply
- Step 3 - Measure the Plate Thickness
- Step 4 - Ground the welding table
- Step 5 - Set Speed and Voltage
- Step 6 - Put on the necessary protective equipment
- Step 7 - Position the Torch at the Right Angle
- Step 8 - Push or Pull
- Step 9 - Press the Trigger Switch
- Step 10 - Finish Welding
- Safety Issues Related to Welding
- Summing up
By the end of this guide, you should know how to properly use a wire feed welder.
Wire feed welders are one of the best ways to join thin and thick steel, and knowing how to use them can help you achieve welding prowess. Learning how to use a wire feed welding machine is not that difficult. But there are certain things, such as the type of gas and the angle of rotation, which, if not studied properly, can cause a lot of problems.
Unfortunately, many people do not take the time to study in detail and end up injuring themselves or doing poor quality work.
In general, to properly use the wire feed welding machine, follow these steps.
- Connect the wire feed welding machine to a suitable electrical outlet.
- Turn on the gas cylinder and maintain the correct gas flow rate (CFH).
- Inspect the steel plate and determine the thickness of the material.
- Connect the ground clamp to the welding table and ground it.
- Set the correct speed and voltage on the welding machine.
- Wear all necessary protective equipment.
- Position the welding gun at the correct angle.
- Choose your welding technique.
- Press the start switch located on the welding gun.
- Properly start the burner on steel plates.
We'll go into more detail below.
How does a wire feed welding machine work?
Wire-fed welding machines produce welds using continuous-fed wire electrodes. These electrodes enter the machines with the help of an electrode holder. The following processes are started when the trigger switch on the burner is pressed.
- The power supply springs will start to work
- The cutscenes will also start at the same time.
- The arch spring will start working
- The gas will start flowing
- The rollers will feed the wire
So, with a burning arc, the wire electrode and the base metal will begin to melt. These two processes take place simultaneously. As a result of these processes, the two metals will melt and form a welded joint. The protection of metals from contamination performs the role of a protective gas.
If you are familiar with MIG welding, you will understand that the process is similar. However, the implementation of such welding requires appropriate skills and equipment.
What You Need to Know Before Using a Wire Feed Welder
Before we move on to cutting, it is important to learn about the technical process of the wire feed welding machine. A proper understanding of these techniques will greatly help you when welding.
Мanagement
When it comes to directions, you can choose from two options. You can either pull or push. Here is a simple explanation about them.
When you bring the welding gun towards you while welding, this process is known as the pull method. Pushing the welding gun away from you is known as the push technique.
The pull method is commonly used in flux-cored wire and electrode welding. Use the push technique for a wire feed welder.
Tip: For a MIG welder, you can use push or pull methods.
Working angle
The relationship between the welder's workpiece and the axis of the electrode is known as the working angle.
The working angle depends entirely on the connection and the type of metal. For example, the working angle may vary depending on the type of metal, its thickness, and the type of connection. When considering the above factors, we can distinguish four different welding positions.
- flat position
- Horizontal position
- Vertical position
- Overhead position
Angle for various types of connections
For a butt joint, a suitable angle is 90 degrees.
Maintain an angle of 60 to 70 degrees for a lap joint.
Maintain a 45 degree angle for T-joints. All three of these joints are in the horizontal position.
When it comes to horizontal position, gravity plays a major role. Thus, keep the working angle between 0 and 15 degrees.
Maintain an upright working angle of 5 to 15 degrees. The overhead positions are a little tricky to handle. There is no defined working angle for this position. So use your experience for this.
Travel angle
The angle between the welding torch and the weld in the plate is known as the travel angle. However, the plate must be parallel to the direction of travel. Most welders maintain this angle between 5 and 15 degrees. Here are some of the benefits of the correct angle of movement.
- Produce less spatter
- Increased arc stability
- Higher penetration
Angles over 20 degrees have less performance. They produce a high amount of spatter and less penetration.
Wire Selection
Choosing the right wire for your welding task is very important. There are two types of wire for wire feed welding machines. So it's not hard to choose something.
ER70C-3
The ER70S-3 is ideal for general purpose welding applications.
ER70C-6
It is the ideal choice for dirty or rusty steel. So use this wire for repair and maintenance work.
Wire size
For thicker metals, choose 0.035" or 0.045" wire. Use 0.030 inch wire for general purpose applications. 0.023" diameter wire is best for thinner wires. So, depending on your work, choose the appropriate size from the wire electrodes ER70S-3 and ER70S-6.
Choice of gas
As with wire electrodes, choosing the right type of shielding gas will determine the quality of your weld. The combination of 25% carbon dioxide and 75% argon is the ideal mixture for a high quality weld. Using this combination will reduce spatter. In addition, it will significantly prevent burn-through of the metal. Using the wrong gas can result in a porous weld and the release of toxic fumes.
Tip: Using 100% CO2 is an alternative to the above mixture. But CO2 produces a lot of spatter. So it's better with Ar and CO2 mixture.
Wire length
The length of the wire that sticks out of the welding gun is more important than you might think. This directly affects the stability of the arc. So, leave a 3/8 inch protruding length. This value is the standard used by most welders.
Keep in mind: A longer wire may make a hissing sound from the arc.
10 Step Guide to Using a Wire Feed Welder
Now you know about angles, wire and gas selection from the previous section. This basic knowledge is enough to continue working with our wire feed welding machine.
Step 1 - Connect to an electrical outlet
For a wire feed welding machine, you will need a special socket. Most welders come with a 13 amp outlet. So, find a 13 amp outlet and plug in your wire feed welding machine.
Tip: Depending on the power of the outlet of the welding machine, the current in the outlet may vary.
Step 2: Turn on the gas supply
Then go to the gas tank and release the valve. Turn the valve counterclockwise.
Set the CFH value to about 25. The CFH value refers to the gas flow rate.
Keep in mind: Select a gas according to the instructions in the previous section.
Step 3 - Measure the Plate Thickness
Then take the two plates you will be using for this welding job and measure their thickness.
To measure the thickness of this plate, you will need a gauge like the one shown in the image above. Sometimes you get this sensor with a welding machine. Or you can buy one from your local hardware store.
Place the gauge on the plate and determine the thickness of the plate. In our example, the plate thickness is 0.125 inches. Write down this value. You will need it later when you set the speed and voltage.
Step 4 - Ground the welding table
Most welding machines come with a ground clamp. Use this clamp to ground the welding table. This is a mandatory security measure. Otherwise, you may be electrocuted.
Step 5 - Set Speed and Voltage
Lift the cover located on the side of the welding machine.
On the lid you can find a chart that shows the speed and voltage of each material. To find these two values, you need the following information.
- Material type
- Gas type
- Wire thickness
- Plate diameter
For this demonstration, I used a 0.125" diameter steel plate and C25 gas. C25 gas includes Ar 75% and CO2 25%. In addition, the wire thickness is 0.03 inches.
According to these settings, you need to set the voltage to 4 and the speed to 45. Look at the image above to get a clear idea of this.
Now turn on the switch on the welding machine and set the voltage and speed on the gauges.
Step 6 - Put on the necessary protective equipment
The welding process is a dangerous activity. To do this, you will need a lot of protective equipment. So put on the following protective gear.
- Respirator
- Protective glass
- Protective gloves
- welding helmet
Note: Do not risk your health by wearing the above protective equipment before starting the welding process.
Step 7 - Position the Torch at the Right Angle
Consider the working angle and travel angle and install the welding torch at the correct angle.
For example, keep the travel angle between 5 and 15 degrees and decide the working angle depending on the type of metal, thickness and connection type. For this demonstration, I am butt welding two steel plates.
Step 8 - Push or Pull
Now decide on the welding technique for this task; pull or push. As you already know, push welding is the best option for wire feed welders. So, position the welding torch accordingly.
Step 9 - Press the Trigger Switch
Now press the trigger switch on the torch and start the welding process. Remember to hold the welding torch firmly during this step.
Step 10 - Finish Welding
Pass the welding torch through the steel plate welding line and complete the process properly.
Tip: Do not touch the welded plate immediately. Leave the plate on the welding table for 2-3 minutes and let it cool down. Touching the welded plate while it is still hot can burn your skin.
Safety Issues Related to Welding
Welding raises many safety concerns. Knowing these issues early can be quite helpful. So, here are some important security questions.
- Sometimes welding machines can emit harmful fumes.
- You may get electrocuted.
- Eye problems
- You may have to deal with radiation burns.
- Your clothes may catch fire.
- You can get metal smoke fever
- Exposure to metals such as nickel or chromium can lead to occupational asthma.
- Without proper ventilation, the noise level may be too much for you.
To prevent such safety issues, always wear suitable protective equipment. So, here are a few steps to protect yourself.
- Wearing gloves and boots will protect you from skin burns. (1)
- Wear a welding helmet to protect your eyes and face.
- Using a respirator will protect you from toxic gases.
- Maintaining proper ventilation in the welding area will reduce noise levels.
- Grounding the welding table will protect you from any impact.
- Keep a fire extinguisher in the workshop. It will come in handy during a fire.
- Wear flame resistant clothing while welding.
If you follow the above precautions, you will be able to complete the welding process without injury.
Summing up
Whenever you use a wire feed welder, follow the 10 step guide above. Remember that becoming an expert welder is a time-consuming task. So be patient and follow the correct welding technique.
The welding process depends on your skills, direction, travel angle, wire type and gas type. Consider all these factors when welding with wire feed. (2)
Take a look at some of our articles below.
- How to test an electrical outlet with a multimeter
- How to connect ground wires to each other
- How to disconnect a wire from a plug-in connector
Recommendations
(1) skin burns – https://www.mayoclinic.org/diseases-conditions/burns/symptoms-causes/syc-20370539
(2) gas type - https://www.eia.gov/energyexplained/gasoline/octane-in-depth.php
Video links


Watch this video on YouTube


Watch this video on YouTube


Watch this video on YouTube


Watch this video on YouTube

