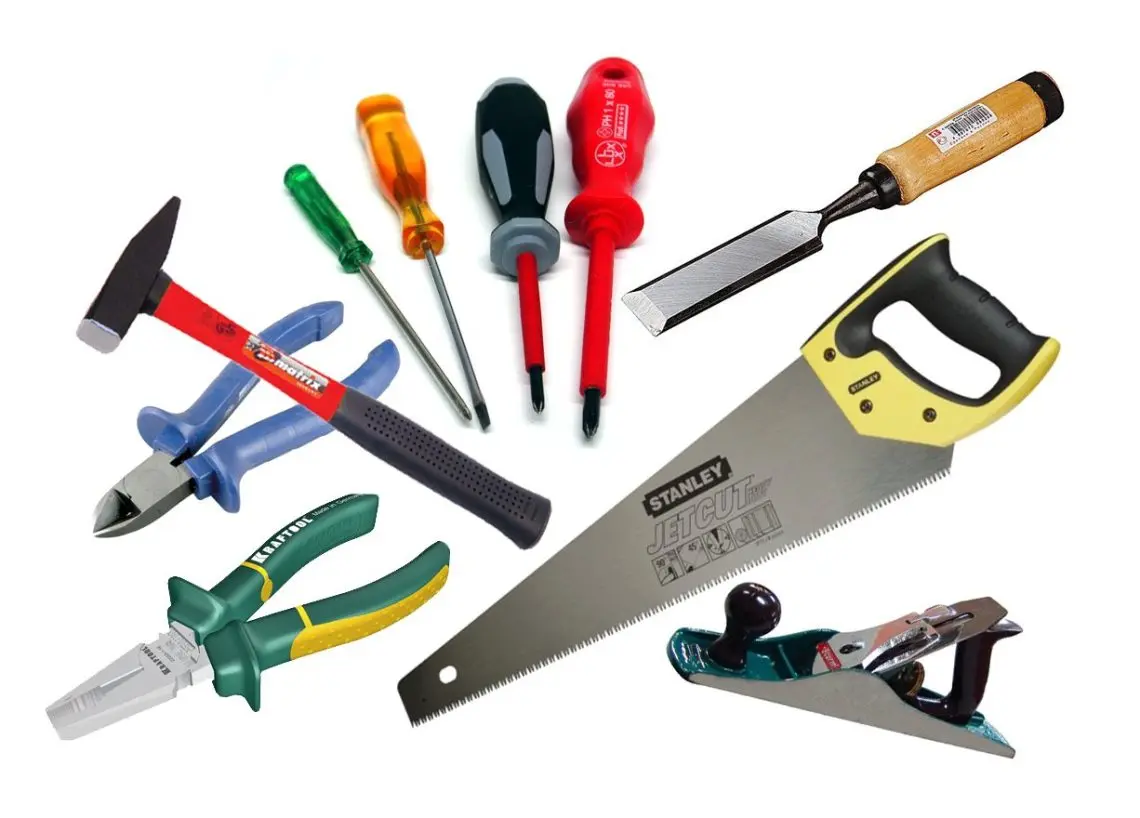
How to Disconnect Wires from a Harness (5 Step Guide)
Content
By the end of this article, you should know how to quickly and efficiently disconnect wires from a wiring harness.
A faulty wiring harness can lead to a broken line, which is a common cause of car breakdowns, which is why I tried to create this article to prevent any common problems people have when doing DIY repairs.
Over the years as an electrician, I have come across a lot of little things in this process, which I will share below.
What are the possible causes of engine wiring harness failure?
Prolonged use may cause rust, cracking, chipping, and other electrical problems. For example, the harness can bend when conditions change from hot to cold. Daily use can harden the tethers over time, causing the sections to soften and break. In the presence of severe weather conditions, degradation may occur.
User errors can lead to issues such as incorrect wiring, incorrect wiring harness connection to the chassis, or approximate dimensions that prevent the entire wiring harness from being properly installed due to lack of sufficient maintenance or adjustment. It can also lead to motor connection failure and problems with other electrical components.
Wire Harness Connector Removal Instructions
1. Remove the retaining latch
Before inserting or removing wires, you must open the locking latch at the bottom or top of the wire connection housing. Use a flat blade knife or screwdriver to create the lever.
There are tiny square holes on the back edge of the lock where you can insert a screwdriver. Smaller shells will only contain one slot. Larger shells have two or three. To open the latch, press it.
Do not attempt to fully open the latch; it will protrude about 1 mm. The latch in cross section resembles a harp, each terminal passes through one of the holes. You will damage the terminals if you push the latch too hard.
If the latch is dull, slowly pull it up through the holes on the left and right sides of the case. If you insert the screwdriver too far into the side holes, you risk damaging the outer terminals.
Even when the latch is released, spring clips remain on the body or terminal to hold the terminals in place (so they don't fall out).
2. Holes for pins
If you look closely at the pin slots on the back of the case, you will notice that they are all encoded (built as a "P" or "q" character for bottom latch surfaces, or "b" for top latch cases). The contact terminal has a small rib that must be pointing up or down to fit into the hole.
3. Disconnect the wiring harness.
There are two types of plastic plugs with socket terminals.
Each type requires a unique process to extract the wires. Looking at the front of the case, you can determine its type. The outside diameter of both plugs is the same, as is the relative spacing of the smaller square pin holes. As a result, both designs fit into the same socket on the back of the wiring harness.
"B" type shells are commonly used for opposite sex shells (female shells with male terminals).
Retrieval - Type "A" Enclosure
This type of plastic shell is most commonly found in factory seat belts or seat belts made by car manufacturers. I have never seen them in aftermarket cables.
Each terminal is held in place by a small plastic spring clip on the housing. In the image above (shell type "A"), the springs can be inside the larger hole above each pinhole. The spring clip is almost the same width as the huge hole.
Rotate the clip up and out of the hole on the nose of the metal terminal. This will release the terminal, allowing you to pull the wire out of the back of the case.
You will use a small screwdriver (yellow) to grab the comb on the front edge of the spring clip and pry up the spring.
Procedure
You may need another person to pull on the wire (after you unplug the plastic spring clip).
- Open the locking latch if you have not already done so (see instructions above).
- Hold the connector shell securely at the sides so as not to press on the lower retaining lock.
- Carefully insert the wire into the plug. This takes the load off the spring clip. Use a small flathead screwdriver (such as for eyeglasses) as a lever. Your screwdriver should be tiny and have a straight, chisel-shaped edge (not rounded, bent, or worn). Place the end of the screwdriver in the giant hole above the terminal you want to remove in front of the case. Nothing should be inserted into the smaller drilled hole.
- Adjust the tip of the screwdriver so that it slides over the top of the metal terminal. Slide it just enough to catch the tip of the plastic spring clip. Maintain slight internal pressure on the screwdriver (but not excessive).
- Turn the spring clip up. Use your fingers and thumb to apply upward force on the screwdriver, not on the plastic housing.
- Listen and feel when the spring snaps into place - the screwdriver will easily slip past it. If this happens, gently try again.
- The plastic spring clasp shouldn't wobble a lot - maybe less than 0.5mm or 1/32″.
- Once the connection is unlocked, you should be able to easily remove the wire.
If you start to damage the rubber spring latch that secures the terminal, you will have to abandon this method and solder or crimp the tail that goes into the connection. When deciding where to cut the wire, make the cut long enough to work with.
Don't forget to lock the retaining clasp on the bottom of the case once you've finished removing and inserting the wires. If you don't do this, you won't be able to fit electrical components into the head unit connection.
Retrieval - "B" body
This type of plastic casing is commonly found in aftermarket suspension straps. They can also be seen on OEM components (eg additional subwoofers, navigation modules, etc.).
Each terminal has a small metal spring clip that secures it to the plastic housing. You will need to find or make an extraction tool to release the spring clip.
The tool must have a section large enough to grip and a tiny tip large enough to fit into the housing screw removal hole.
The tip should be 1 mm wide, 0.5 mm high and 6 mm long. The point should not be too sharp (it can just pierce the plastic of the case).
Procedure
You may need the help of a second person to pull on the wire (after opening the plastic spring clasp).
- Open the locking latch if you have not already done so (see instructions above).
- Hold the connector shell securely at the sides so as not to press on the lower retaining lock.
- Carefully insert the wire into the plug. It takes the load off the metal spring clip.
- Insert the eject tool through the eject hole (the rectangular hole under the connector you want to remove). Nothing should be inserted into the square hole.
- You can hear a slight click where you inserted the 6mm tool. The tip of the tool presses against the spring clip.
- Insert the extraction tool into the hole with little force. You can then remove the wire by pulling on it. (1)
If the wire refuses to budge and you are pulling too hard, back the removal tool 1 or 2 mm and repeat.
I do not recommend pulling the wire with needle nose pliers. Using your fingertips will allow you to feel how hard you are tensing up and when to stop. It's also too easy to crush 20 gauge wires with pliers or even smaller. (2)
How to make an extraction tool
Some used huge staples. On the other hand, they don't give you anything to grab onto and tend to draw by hand.
Someone mentioned using the eye of a sewing needle. I tried a small one but it was too thick vertically. Using a hammer to flatten the future might help. You will also need to tweak the sharp end - remove the tip and bend it so you can press on it without having to swipe multiple times with your finger.
Making changes to the straight pin worked well for me. It would be helpful if you used sharp wire cutters to remove the pointed tip.
Then flatten the end by hitting it several times with a smooth-faced hammer on a hard, smooth surface. You can also insert the tip into a vise with smooth jaws. Continue smoothing the point until the last 6mm (from top to bottom) is thin enough to comfortably fit into the ejection hole. If the tip is too wide (from left to right), file it down to fit into the extraction holes.
Take a look at some of our articles below.
- How to disconnect a wire from a plug-in connector
- How to plug electrical wires
- How to check the wiring harness with a multimeter
Recommendations
(1) pressure - https://www.khanacademy.org/scienc
(2) fingertips – https://www.sciencedirect.com/topics/medicine-and-dentistry/fingertip
Video link

