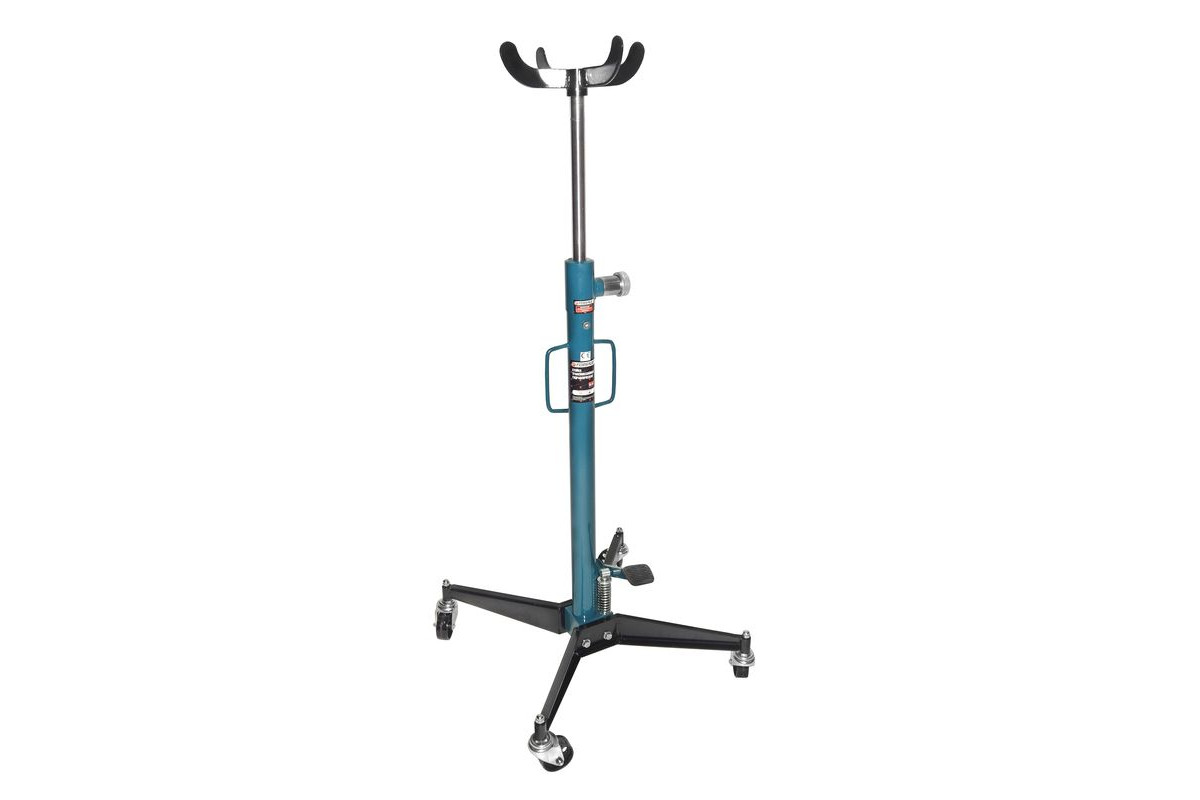
How to make a hydraulic transmission rack with your own hands: materials and drawings for manufacturing
Content
The principle of operation of the auxiliary repair device is as follows: pressing the pedal or lever starts the piston pump, pumping oil into the hydraulic cylinder. And creating pressure, the force of which raises the car. If the lever is released, the pump stops working, the position of the lifted object is automatically fixed.
During the repair of the engine, gearboxes, mechanics are faced with the problem of dismantling heavy units. It is impossible to cope with such work without assistants, and purchased devices are expensive. The way out is a do-it-yourself transmission rack. Homemade lifting equipment makes it possible to save a lot of money, to show their own engineering abilities, ingenuity.
Where is the transmission rack used?
The mechanism has found application in car services and home workshops for servicing nodes that cannot be crawled into in the normal position of a car. These are units located under the bottom: fuel tank, exhaust system, engine, gearbox and transmission elements.
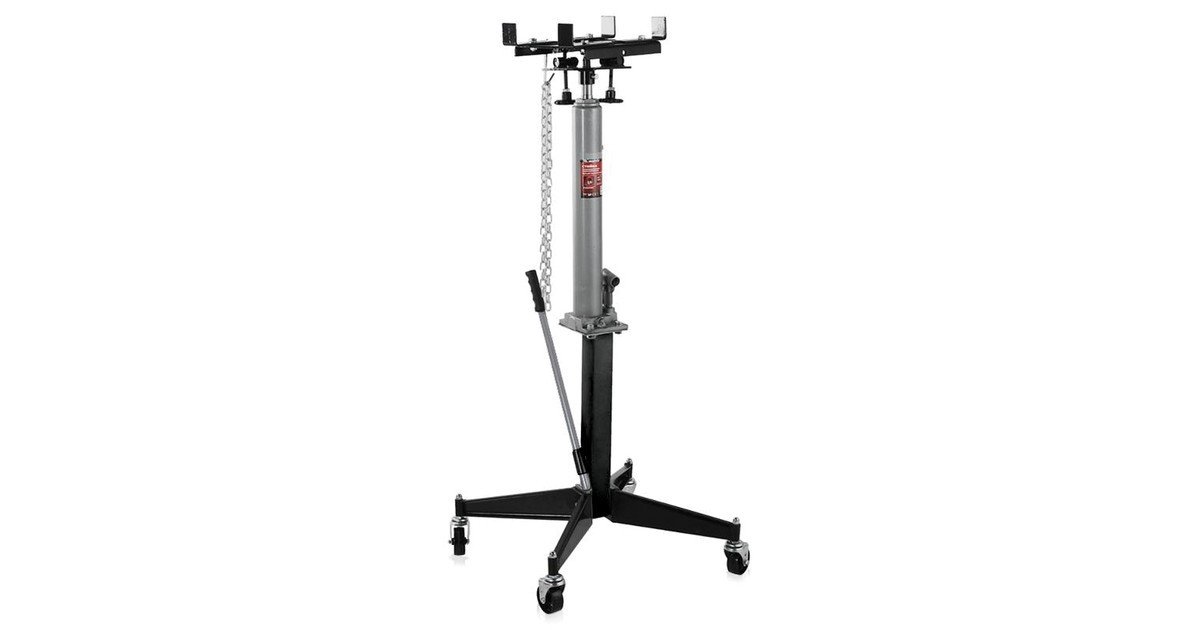
Transmission rack
Car engines weigh up to 100 kg, trucks - up to 500 kg. Removing heavy parts without auxiliary equipment is problematic. For diagnostics, prevention, restoration of nodes in professional services and garages, a hydraulic transmission rack is used, which is easy to do with your own hands. Another name for the device is a hydraulic jack.
Principle of operation
The mechanism is mounted on a platform with four support points. For the mobility of the structure, fixed or hinged transport wheels are installed at the ends of the supports. However, a do-it-yourself hydraulic transmission rack can be made without wheels at all.
A rod extends vertically from the platform. It is either single stage or two stage. The second, retractable option is called telescopic. It is preferable because it has a longer stroke and less bending load. There is only one condition - high-strength alloy steel should serve as the material of execution. The height of the stem of the master is chosen independently, based on the tasks of the device.
A table-nozzle (technological platform) of various configurations is mounted on the rod. Most often, these are “crabs”, on which the part removed from the machine is installed and rigidly fixed.
The principle of operation of the auxiliary repair device is as follows: pressing the pedal or lever starts the piston pump, pumping oil into the hydraulic cylinder. And creating pressure, the force of which raises the car. If the lever is released, the pump stops working, the position of the lifted object is automatically fixed.
To lower the unit, the mechanic presses the lever in the opposite direction. Here the law of gravity comes into force - the object under its own weight smoothly falls to its normal position.
How to make
There are many types of equipment. Most often, home craftsmen come from improvised material. The carrying capacity is calculated from the lift that will go into action.
What is required for this
Assume that the main part of the structure is a jack. It can be screw, linear, manual, pneumatic, but the hydraulic version is more reliable.
The stem is better to make retractable. It will require a metal profile of two sections: outer - 32 mm, inner - 30 mm. If pipes are found, then the outer one should be within 63 mm in diameter, the inner one - 58 mm.
Tools: grinder, welding machine, electric drill with drills of different diameters, bolts, nuts.
Stand drawings
There are many ready-made schemes and instructions on the Internet. But it is better to do the drawings of the transmission rack with your own hands. The platform takes on a lot of weight, so the sheet metal should be a square with sides of 800x800 mm, the thickness of the metal should be at least 5 mm. You can reinforce the site with a profile along the perimeter or diagonals.
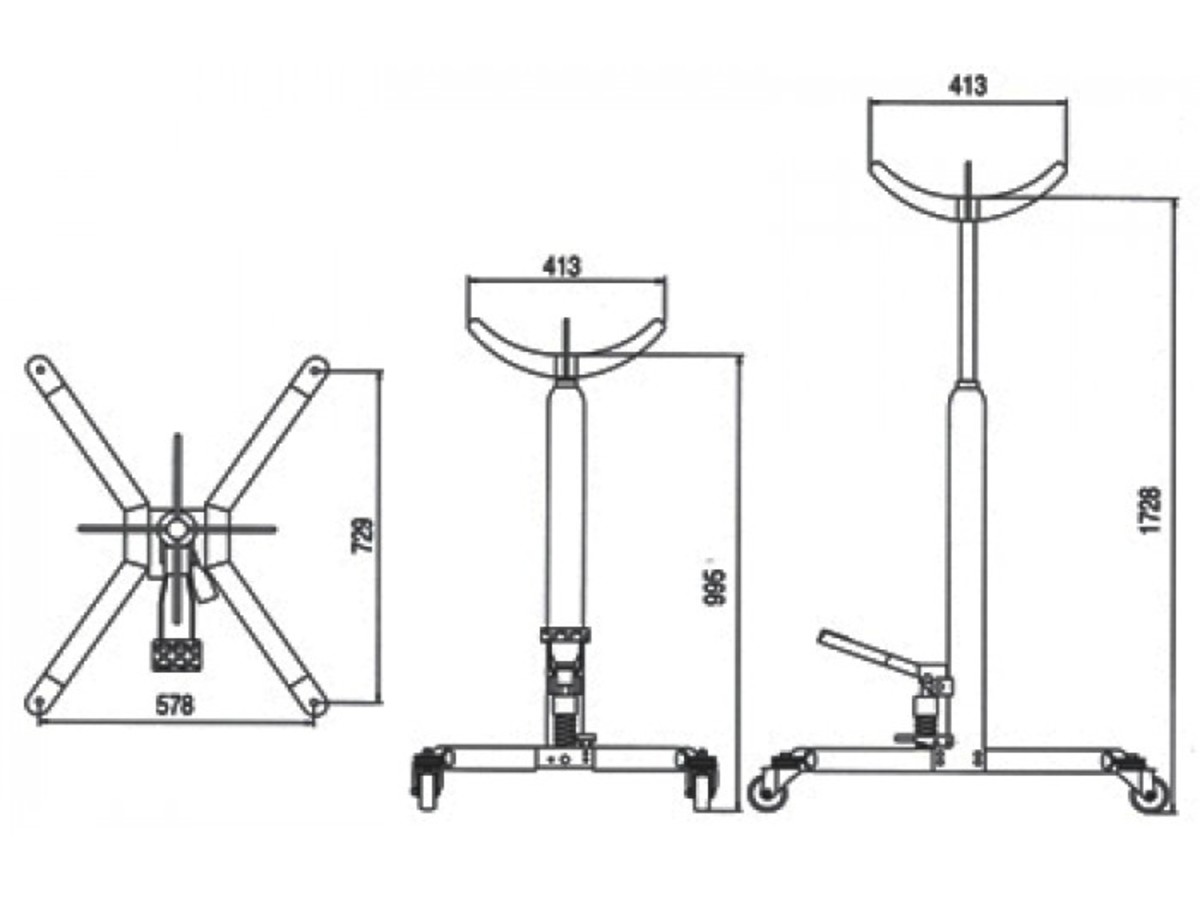
Rack drawing
The height of the rod is 1,2 m, it will extend to a maximum lift of 1,6 m. The extension is limited by the stroke of the jack. The optimal dimensions of the technological platform are 335x335 mm.
Step by step guide
Production takes place in two stages: preparatory work, then assembly. First, cut the metal profile of the required length, prepare the support platform.
You need to make a transmission rack with your own hands in the following order:
- In the center of the platform, weld a profile of a smaller section.
- Put an outer profile on it.
- Weld a plate to the top of the latter, against which the jack will rest.
- Try on the self-lifter, install and weld a support on the rod under it (a piece of sheet according to the size of the bottom of the jack). Secure the lift with metal stops.
- Install the extension table.
- Mount the wheels.
At the last stage, clean the welding spots, give the model an aesthetic appearance by sanding and painting the stand for the vehicle components and assemblies. Install the finished equipment in a viewing hole or on a flyover.
The cost of handicraft is minimal. If the main material is from the selections, then you only need to spend money on articulated wheels and consumables (electrodes, a disk for a grinder, a drill). The time spent on work is calculated in several hours.
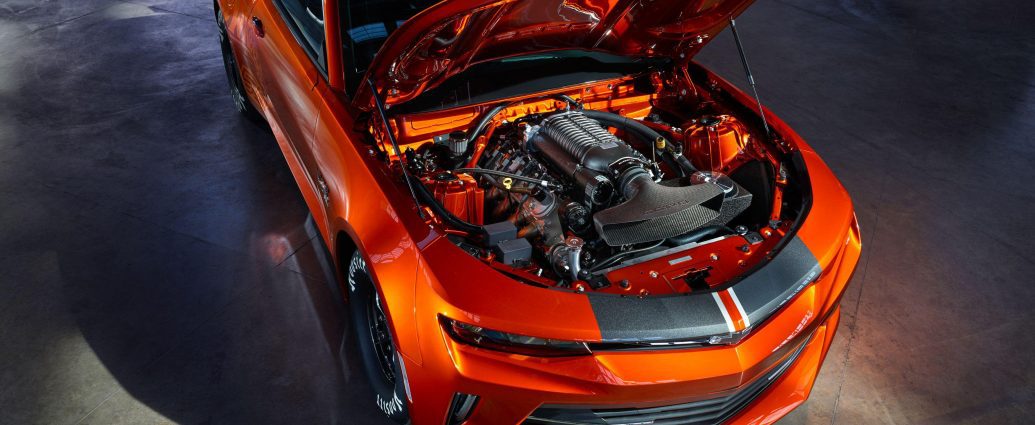
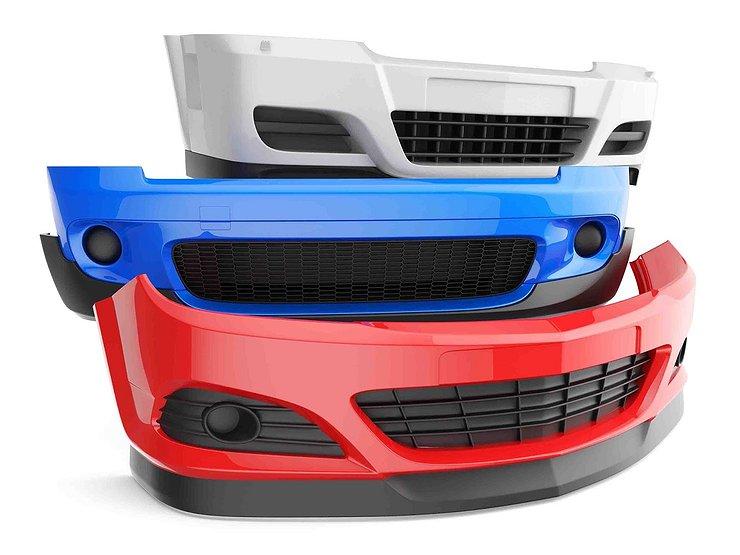