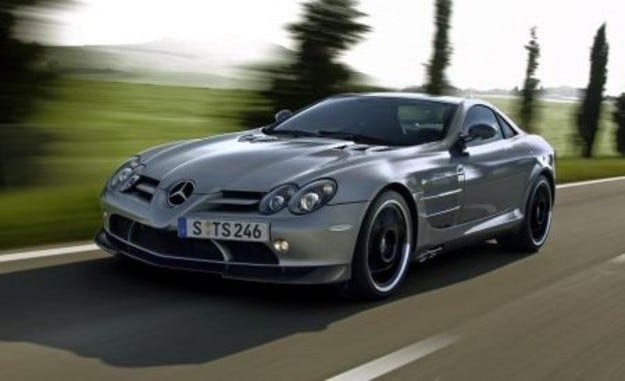
Test drive racing cars made of carbon
Carbon can decide the fate of a car because, by keeping the vehicle low, the extremely lightweight material indirectly reduces fuel consumption. In the future, even bestsellers such as the Golf and Astra will benefit from its use. Currently, however, carbon remains the privilege of only the “rich and the beautiful”.
Paul McKenzie predicts a "black" future for sports cars. In fact, the friendly Briton is not against the racing faction among motorists, but on the contrary - he leads the Mercedes SLR project at McLaren. For him, black is the color of fabric that guarantees the survival of sports cars: woven from thousands of tiny carbon fibers, impregnated with resins and baked in huge ovens, carbon is lighter and at the same time more stable than most other substances and compounds used in the automotive industry. .
Black fibers are increasingly being used in the most luxurious vehicles. Mercedes development engineer Clemens Belle explains why: "In terms of weight, carbon is four to five times better at absorbing energy than conventional materials." That's why the SLR roadster is 10% lighter than the SL for comparable engine size and power. McKenzie adds that if the car is made entirely of carbon fiber when changing generations, at least 20% of the weight can be saved - whether it is a sports car or a compact car.
Carbon is still too expensive
Of course, all manufacturers recognize the importance of light weight. But according to Mackenzie, "Manufacturing a car from carbon is extremely difficult and time-consuming because this material requires a particularly long and special processing." Speaking of Formula 1 cars, the SLR project manager continues: “In this race, the whole team works without stopping to catch their breath, and finally manages to finish only six cars a year.”
Production of the SLR does not go so slowly, but is limited to two and a half copies per day. McLaren and Mercedes have even managed to simplify the tailgate manufacturing process to the point where it now takes as much time as it does steel. However, other components must be cut with surgical precision and then modeled from 20 layers before baking under high pressure and 150 degrees Celsius. autoclave. Often, the product is processed in this way for 10-20 hours.
Hopes for a revolutionary discovery
Still, Mackenzie believes in the future of fine fibers: “More and more carbon elements will be incorporated into cars. Maybe not as widely as the SLR, but if we start with body parts such as spoilers, hoods or doors, the proportion of carbon elements will continue to grow. "
Wolfgang Dürheimer, head of research and development at Porsche, is also convinced that carbon can make cars more efficient. However, this requires a revolution in processing technology, says Dürheimer. The challenge is to produce carbon components in large quantities in a short time to achieve reasonable costs and a reasonable product value.
BMW and Lamborghini also use carbon elements
The new M3 saves five kilograms thanks to the carbon roof. While this achievement may not seem particularly impressive at first glance, it makes a huge contribution to the stability of the car, as it lightens the structure in a particularly important area of gravity. Plus, it doesn't delay installation: BMW will definitely complete more M3 units in one week than McLaren with their SLRs in a full year.
“The Gallardo Superleggera is also a model for greater use of carbon fibre,” proudly declares Lamborghini Development Director Maurizio Reggiano. With carbon fiber spoilers, side mirror housings and other components, the model is “lighter” by as much as 100 kilograms, without losing traditionally heavy systems such as air conditioning. Regini remains an optimist to the last: "If we go down this path and improve the engines enough, I personally see no reason for the demise of supercars."
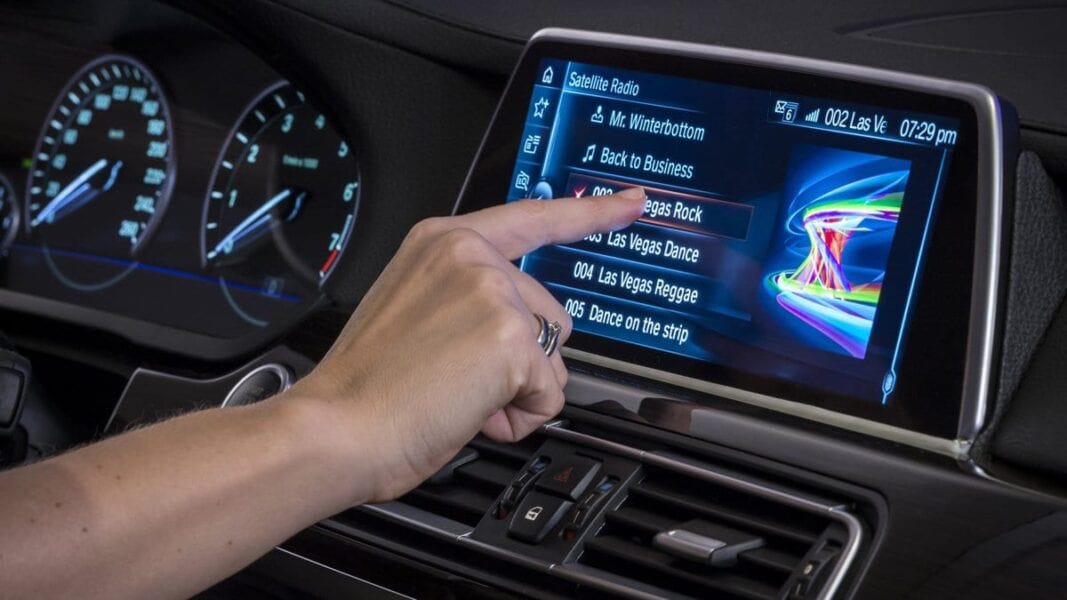
