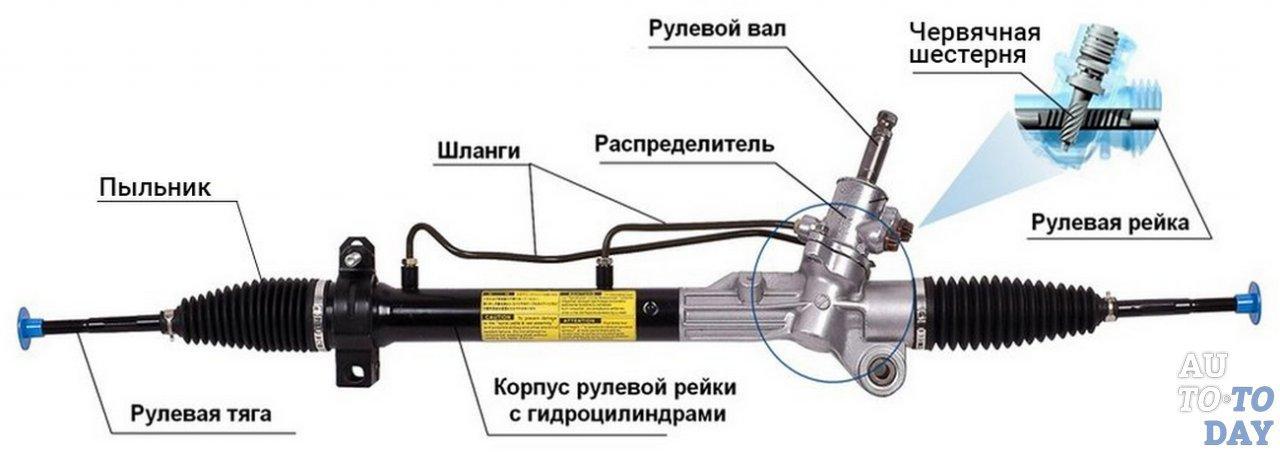
The principle of operation of the power steering rack
Content
The principle of operation of the power steering rack is based on the short-term effect of pressure generated by the pump on the cylinder, which shifts the rack in the right direction, helping the driver to steer the car. Therefore, cars with power steering are much more comfortable, especially when maneuvering at low speed or driving in difficult conditions, because such a rail takes on most of the load required to turn the wheel, and the driver only gives it commands, without losing feedback from the road. .
The steering rack in the passenger transport industry has long supplanted other types of similar devices due to its technical characteristics, which we talked about here (How the steering rack works). But, despite the simplicity of the design, the principle of operation of the steering rack with a hydraulic booster, that is, a hydraulic booster, is still incomprehensible to most car owners.
Steering evolution - a brief overview
Since the advent of the first cars, the basis of steering has become a gear reducer with a large gear ratio, which turns the front wheels of the vehicle in various ways. Initially, it was a column with a bipod attached to the bottom, so a complex structure (trapezium) had to be used to transfer the biasing force to the steering knuckles to which the front wheels were bolted. Then they invented a rack, also a gearbox, which transmitted the turning force to the front suspension without additional structures, and soon this type of steering mechanism replaced the column everywhere.
But the main disadvantage arising from the principle of operation of this device could not be overcome. The increase in gear ratio allowed the steering wheel, also called the steering wheel or steering wheel, to be turned effortlessly, but forced more turns to move the steering knuckle from the extreme right to the extreme left position or vice versa. Reducing the gear ratio made the steering sharper, because the car reacted more strongly even to a slight shift of the steering wheel, but driving such a car required great physical strength and endurance.
Attempts to solve this problem have been made since the beginning of the twentieth century, and some of them were related to hydraulics. The term "hydraulics" itself came from the Latin word hydro (hydro), which meant water or some kind of liquid substance comparable in its fluidity to water. However, until the beginning of the 50s of the last century, everything was limited to experimental samples that could not be put into mass production. The breakthrough came in 1951 when Chrysler introduced the first mass-produced power steering (GUR) that worked in conjunction with the steering column. Since then, the general principle of operation of a hydraulic steering rack or column has remained unchanged.
The first power steering had serious shortcomings, it:
- heavily loaded the engine;
- strengthened the steering wheel only at medium or high speeds;
- at high engine speeds, it created excess pressure (pressure) and the driver lost contact with the road.
Therefore, a normally working hydraulic booster appeared only at the turn of the XXI, when the rake had already become the main steering mechanism.
How a hydraulic booster works
To understand the principle of operation of the hydraulic steering rack, it is necessary to consider the elements included in it and the functions they perform:
- pump;
- pressure reducing valve;
- expansion tank and filter;
- cylinder (hydraulic cylinder);
- distributor.
Each element is part of the hydraulic booster, therefore, the correct operation of the power steering is possible only when all components clearly perform their task. This video shows the general principle of operation of such a system.
Pump
The task of this mechanism is the constant circulation of fluid (hydraulic oil, ATP or ATF) through the power steering system with the creation of a certain pressure sufficient to turn the wheels. The power steering pump is connected by a belt to the crankshaft pulley, but if the car is equipped with an electric hydraulic booster, then its operation is provided by a separate electric motor. The performance of the pump is chosen such that even at idle it ensures the rotation of the machine, and the excess pressure that occurs when the speed increases is compensated by the pressure reducing valve.
The power steering pump is made of two types:
- lamellar;
- gear.
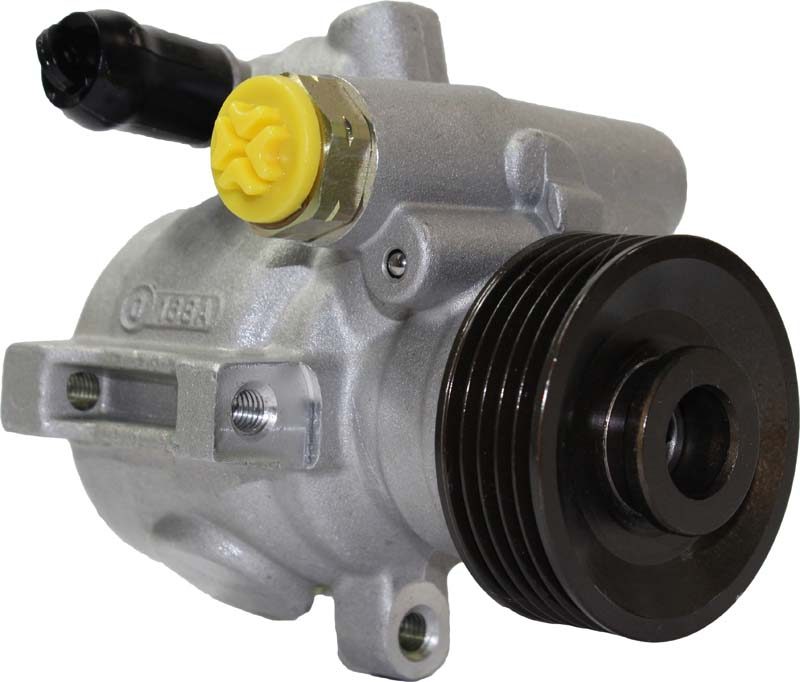
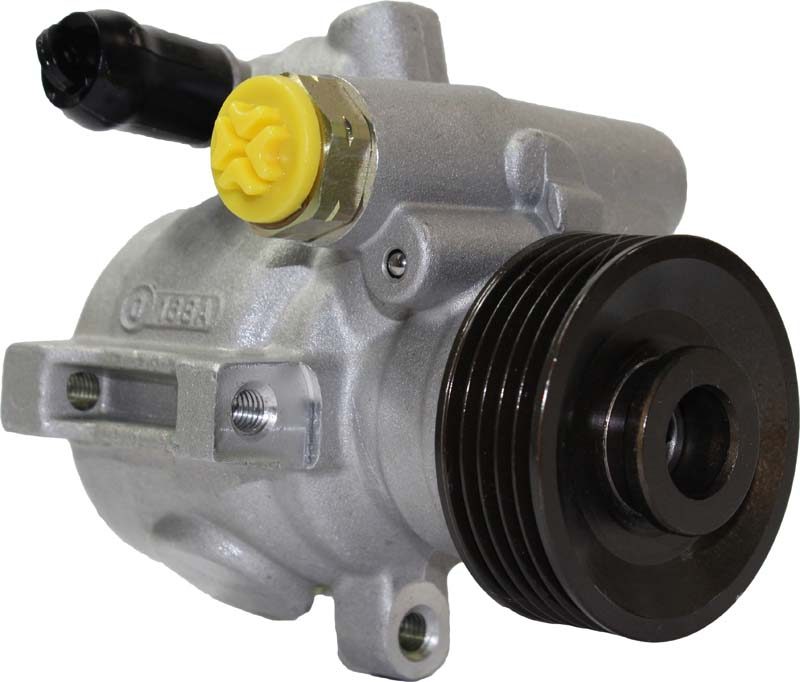
Power steering pump
On cars with hydraulic suspension, one pump ensures the operation of both systems - power steering and suspension, but works on the same principle. It differs from the usual one only in increased power.
Pressure reducing valve
This part of the hydraulic booster works on the principle of a bypass valve, consisting of a locking ball and a spring. During operation, the power steering pump creates a circulation of fluid with a certain pressure, because its performance is higher than the throughput of hoses and other elements. As the engine speed increases, the pressure in the power steering system increases, acting through the ball on the spring. The spring stiffness is chosen so that the valve opens at a certain pressure, and the diameter of the channels limits its throughput, so operation does not lead to a sharp drop in pressure. When the valve opens, part of the oil bypasses the system, which stabilizes the pressure at the required level.
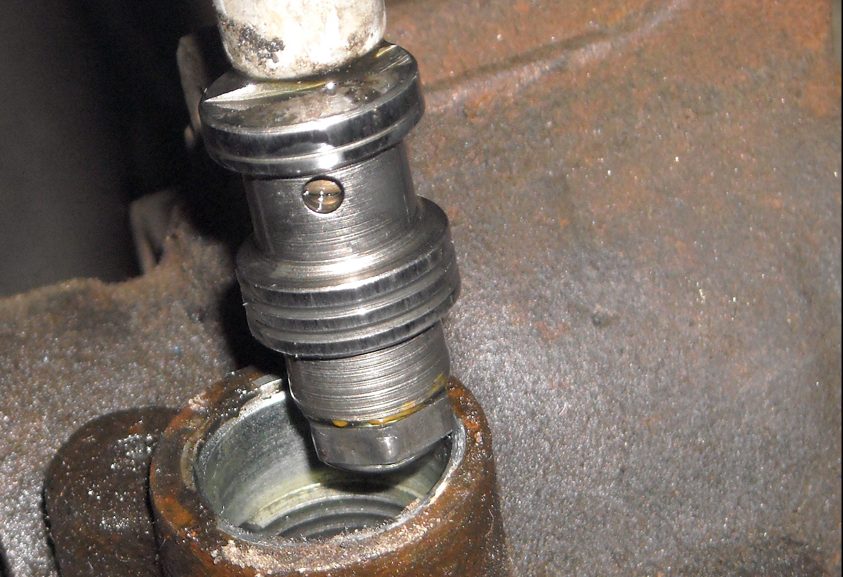
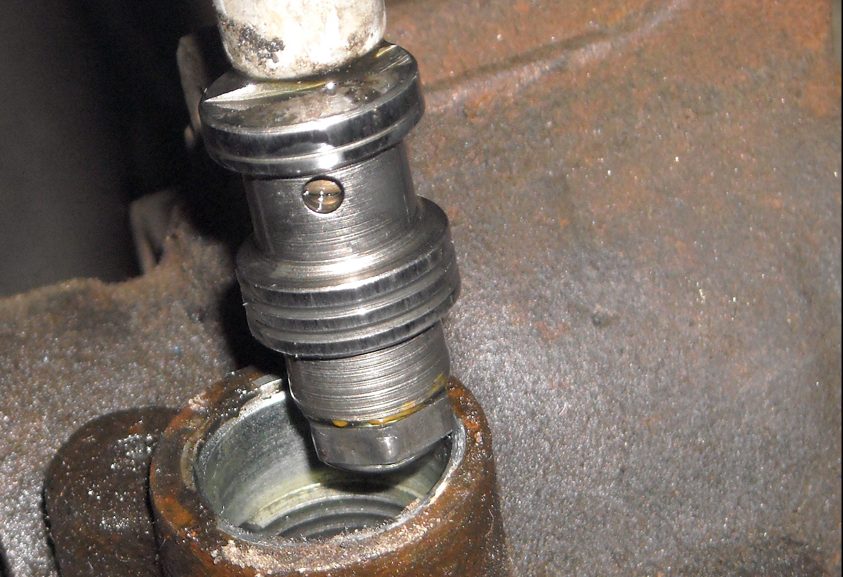
Power steering pressure reducing valve
Despite the fact that the pressure reducing valve is installed inside the pump, it is an important element of the hydraulic booster, therefore it is on a par with other mechanisms. Its malfunction or incorrect operation jeopardizes not only the power steering, but also traffic safety on the road, if the supply line bursts due to excessive hydraulic pressure, or a leak appears, the car’s reaction to turning the steering wheel will change, and an inexperienced person behind the wheel risks not deal with management. Therefore, the device of the steering rack with hydraulic booster implies maximum reliability of both the entire structure as a whole and each individual element.
Expansion tank and filter
During power steering operation, hydraulic fluid is forced to circulate through the power steering system and is affected by the pressure created by the pump, which leads to heating and expansion of the oil. The expansion tank takes in excess of this material, so that its volume in the system is always the same, which eliminates pressure surges caused by thermal expansion. ATP heating and wear of rubbing elements leads to the appearance of metal dust and other contaminants in the oil. Getting into the spool, which is also a distributor, this debris clogs the holes, disrupting the operation of the power steering, which negatively affects the vehicle's handling. To avoid such a development of events, a filter is built into the power steering, which removes various debris from the circulating hydraulic fluid.
Cylinder
This part of the hydraulic booster is a pipe, inside of which there is a part of the rail with a hydraulic piston installed on it. Oil seals are installed along the edges of the pipe to prevent ATP from escaping when the pressure rises. When oil enters the corresponding part of the cylinder through the pipes, the piston moves in the opposite direction, pushing the rack and, through it, acting on the steering rods and steering knuckles.
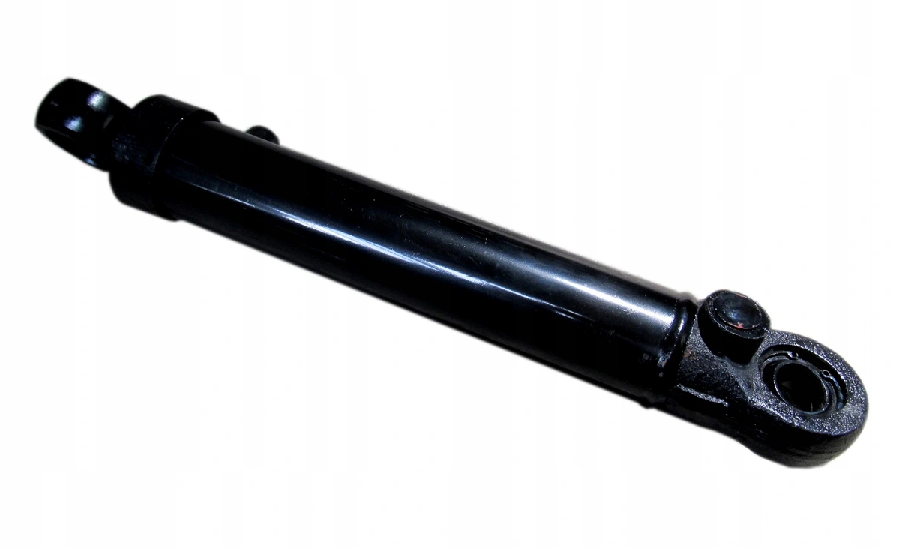
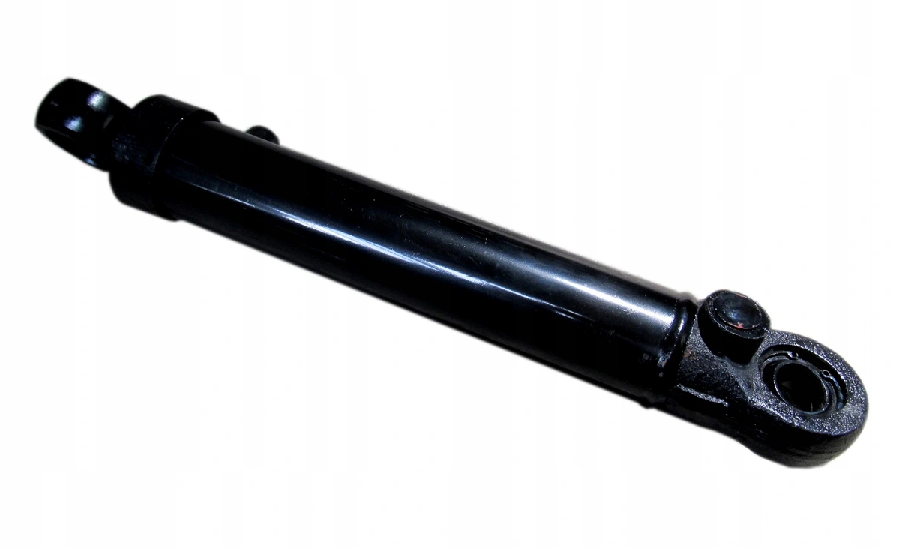
power steering cylinder
Thanks to this power steering design, the steering knuckles begin to move even before the drive gear moves the rack.
Distributor
The principle of operation of the power steering rack is to briefly supply hydraulic fluid at the moment the steering wheel is turned, due to which the rack will begin to move even before the driver makes a serious effort. Such a short-term supply, as well as draining excess fluid from the hydraulic cylinder, is provided by a distributor, which is often called a spool.
To understand the principle of operation of this hydraulic device, it is necessary not only to consider it in a section, but also to more fully analyze its interaction with the rest of the power steering elements. As long as the position of the steering wheel and the steering knuckles correspond to each other, the distributor, also known as the spool, blocks the flow of fluid into the cylinder from either side, so the pressure inside both cavities is the same and it does not affect the direction of rotation of the rims. When the driver turns the steering wheel, the small ratio of the steering rack reducer does not allow him to quickly turn the wheels without applying significant effort.
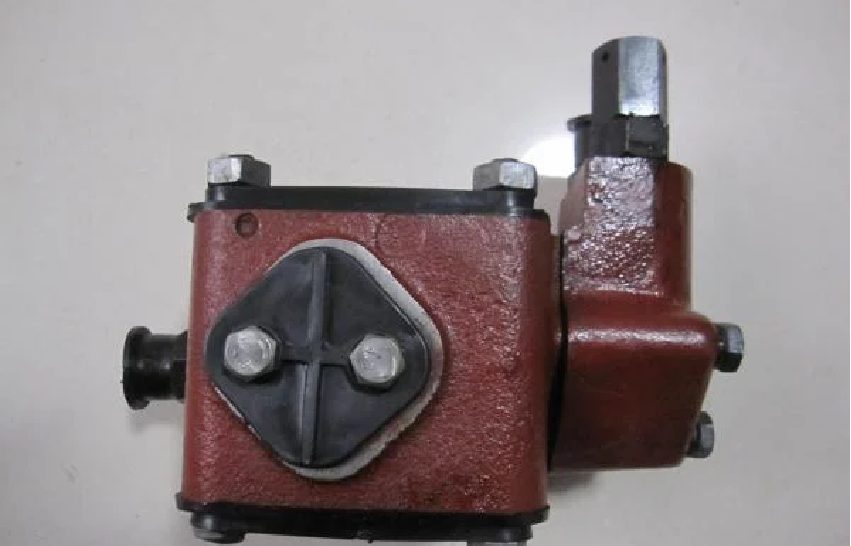
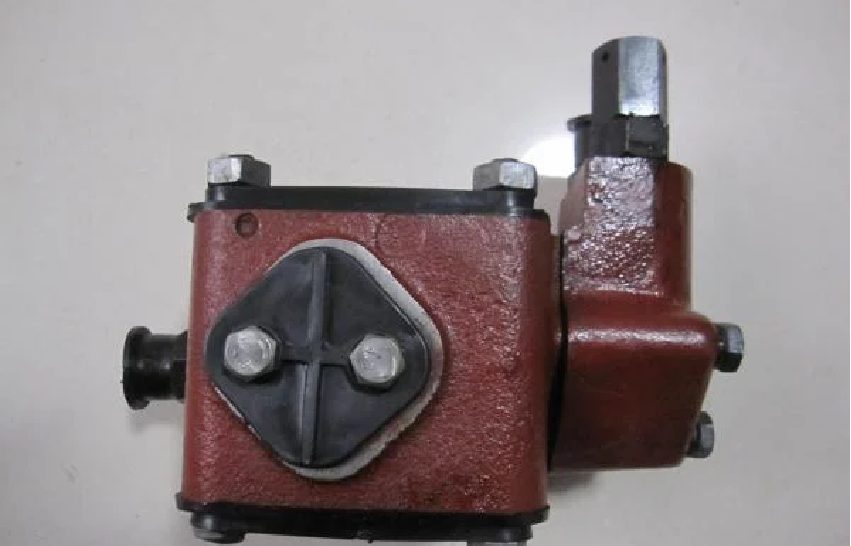
Power steering distributor
The task of the power steering distributor is to supply ATP to the hydraulic cylinder only when the position of the steering wheel does not correspond to the position of the wheels, that is, when the driver turns the steering wheel, the distributor first fires and forces the cylinder to act on the suspension knuckles. Such an impact should be short-term and depend on how much the driver turned the steering wheel. That is, first the hydraulic cylinder must turn the wheels, and then the driver, this sequence allows you to apply minimal effort to turn, but at the same time “feel the road”.
Principle of operation
The need for such a distributor operation was one of the problems that prevented the mass production of hydraulic boosters, because usually in a car the steering wheel and steering gear are connected by a rigid shaft, which not only transfers force to the steering knuckles, but also provides the pilot of the car with feedback from the road. To solve the problem, I had to completely change the arrangement of the shaft connecting the steering wheel and the steering gear. A distributor was installed between them, the basis of which is the principle of torsion, that is, an elastic rod capable of twisting.
When the driver turns the steering wheel, the torsion bar initially twists slightly, which causes a mismatch between the position of the steering wheel and the front wheels. At the moment of such a mismatch, the distributor spool opens and hydraulic oil enters the cylinder, which shifts the steering rack in the right direction, and therefore eliminates the mismatch. But, the throughput of the distributor spool is low, so the hydraulics do not completely replace the efforts of the driver, which means that the faster you need to turn, the more the driver will have to turn the steering wheel, which provides feedback and allows you to feel the car on the road
Устройство
To perform such work, that is, dosed ATP into the hydraulic cylinder and stop the supply after the mismatch has been eliminated, it was necessary to create a rather complex hydraulic mechanism that works according to a new principle and consists of:
- a torsion bar connected to the drive gear, which provides mismatch when turning the steering wheel;
- the inside of the spool;
- outer part of the spool.
The inner and outer parts of the spool adjoin each other so tightly that not a drop of liquid seeps between them, in addition, holes are drilled in them for the supply and return of ATP. The principle of operation of this design is the precise dosing of the hydraulic fluid supplied to the cylinder. When the position of the rudder and rack is coordinated, the supply and return openings are shifted relative to each other and the liquid through them does not enter or flow out of the cylinders, so the latter is constantly filled and there is no threat of airing. When the pilot of the car turns the steering wheel, the torsion bar first twists, the outer and inner parts of the spool are displaced relative to each other, due to which the supply holes on one side and the drain holes on the other are combined.
Entering the hydraulic cylinder, the oil presses on the piston, shifting it to the edge, the latter shifts to the rail and it begins to move even before the drive gear acts on it. As the rack shifts, the mismatch between the outer and inner parts of the spool disappears, due to which the oil supply gradually stops, and when the position of the wheels reaches a balance with the position of the steering wheel, the supply and output of ATP are completely blocked. In this state, the cylinder, both parts of which are filled with oil and form two closed systems, performs a stabilizing role, therefore, when hitting a bump, a noticeably smaller impulse reaches the steering wheel and the steering wheel does not pull out of the driver’s hands.
Conclusion
The principle of operation of the power steering rack is based on the short-term effect of pressure generated by the pump on the cylinder, which shifts the rack in the right direction, helping the driver to steer the car. Therefore, cars with power steering are much more comfortable, especially when maneuvering at low speed or driving in difficult conditions, because such a rail takes on most of the load required to turn the wheel, and the driver only gives it commands, without losing feedback from the road. .


Watch this video on YouTube
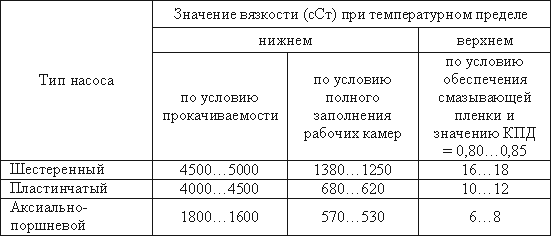
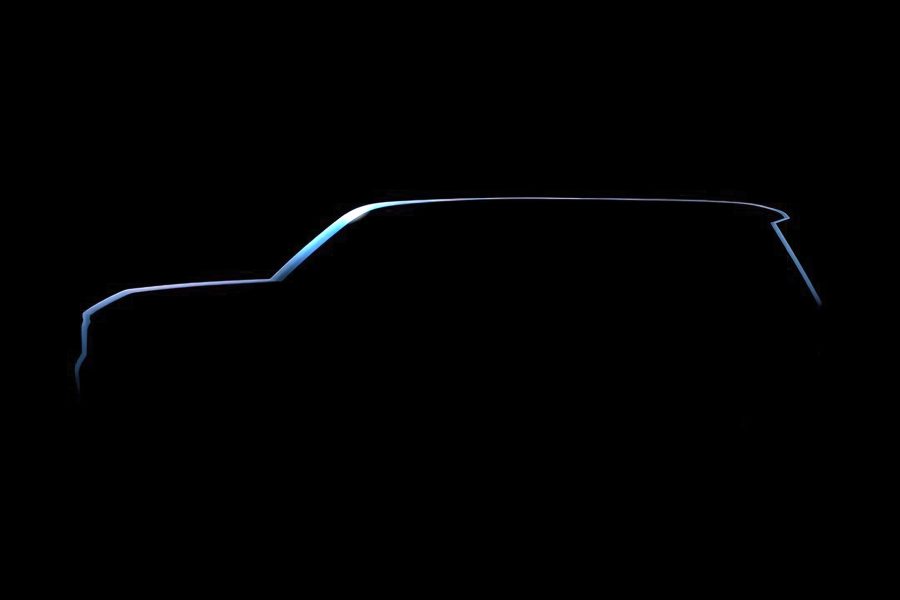