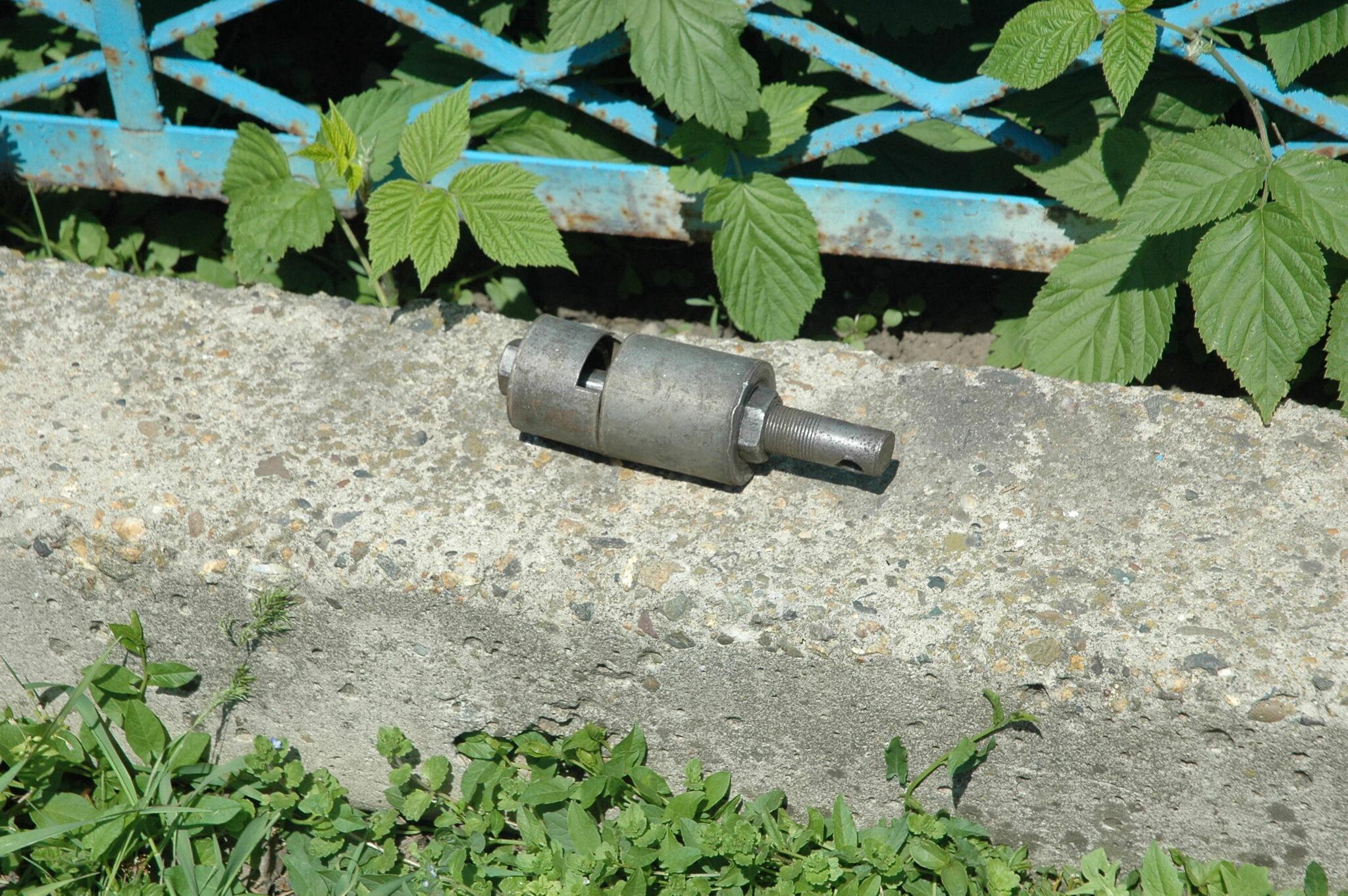
Do-it-yourself bearing puller: design and device, drawings, types, materials and manufacturing process
Content
It is easier to make a mechanical bearing puller with your own hands, since it is simpler and cheaper. In garages and auto repair shops, this is the most common type of tool. It allows you to quickly change grip points, has a spring-loaded effect that improves traction operation.
In the tool kit, car mechanics keep devices for dismantling various types of bearings. On sale there is a repair equipment specially designed for this. But it is expensive, so many craftsmen make their own bearing puller.
Design and construction
Bearings are found in a car in many nodes: clutch release, hub. The part “sits” always very tightly, with an interference fit, and it is difficult to remove it during current or operational repairs. Locksmiths have to make great efforts, which are facilitated by auxiliary, often home-made, equipment.
The press tool is not a very simple tool, but, having studied the technology and drawings of bearing pullers, it is possible to make a mechanism in garage conditions with your own hands.
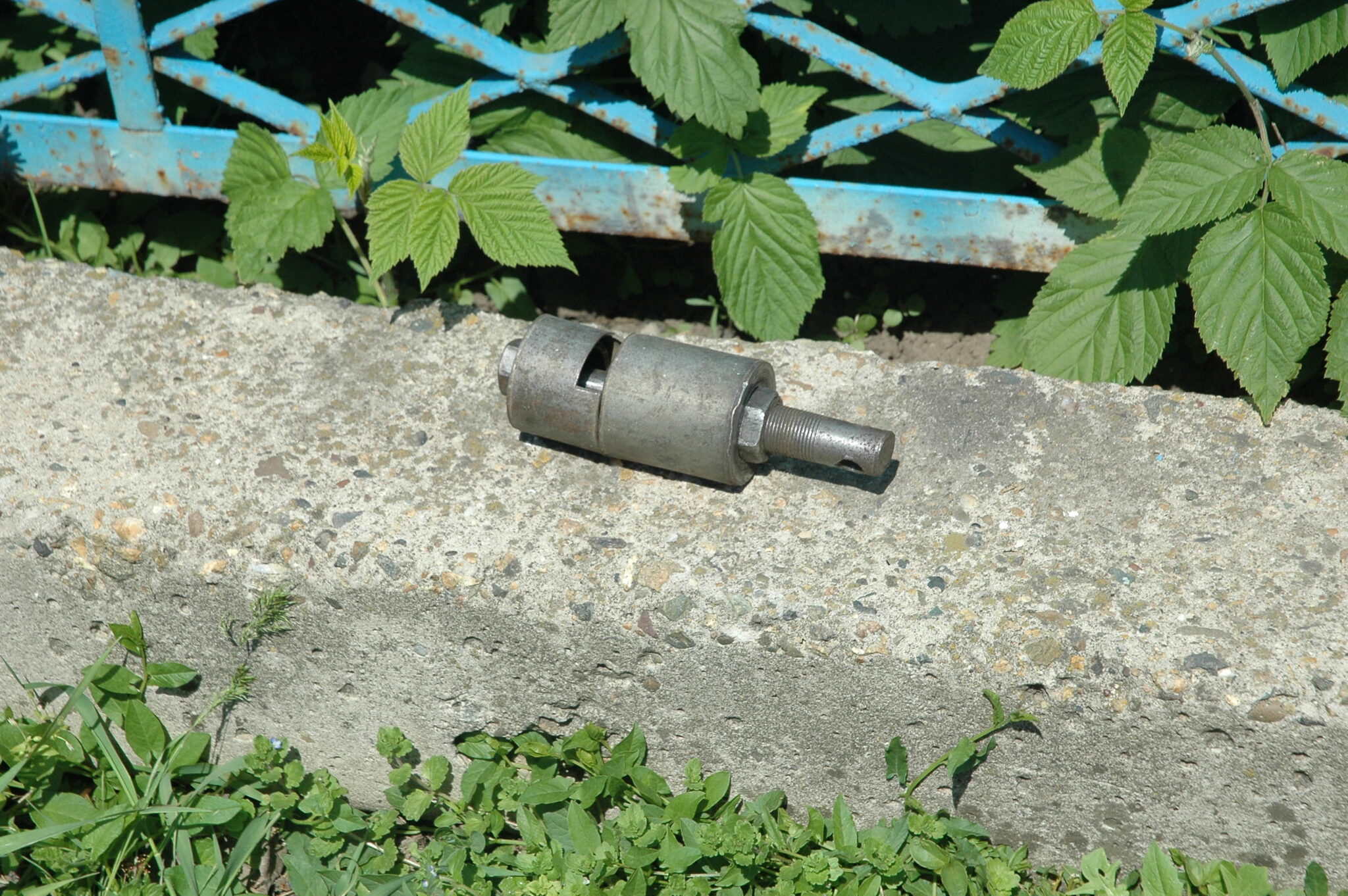
Presser / presser of silent blocks and wheel bearings
The principle of operation of the mechanism is to transmit a very high torque (sometimes up to 40 tons) to a dismantled part. With all the constructive diversity, vypressovshchiki consist of two main elements:
- The threaded center stem is a solid bolt of defined dimensions.
- Hook-shaped grips for engagement with the element being removed.
The mechanism works by means of a bolt (central body): when it is twisted or unscrewed, the bearing leaves the seat or is pressed in.
Blueprints
The undercarriage of the car suffers from unevenness in the roadway, especially the parts responsible for damping vibrations. First of all, the front and rear hub mechanisms are destroyed. To restore them, a do-it-yourself wheel bearing puller is required.
The creation of a mechanism begins with calculations, do-it-yourself drawings of wheel bearing pullers, selection of materials and tools.
Types of pullers
According to the type of drive, the toolkit is divided into two groups: mechanical and hydraulic pullers. A hydraulic cylinder is built into the latter, which develops a force of tens of tons. Hydraulic lifters are designed for the most complex and difficult cases.
It is easier to make a mechanical bearing puller with your own hands, since it is simpler and cheaper. In garages and auto repair shops, this is the most common type of tool. It allows you to quickly change grip points, has a spring-loaded effect that improves traction operation.
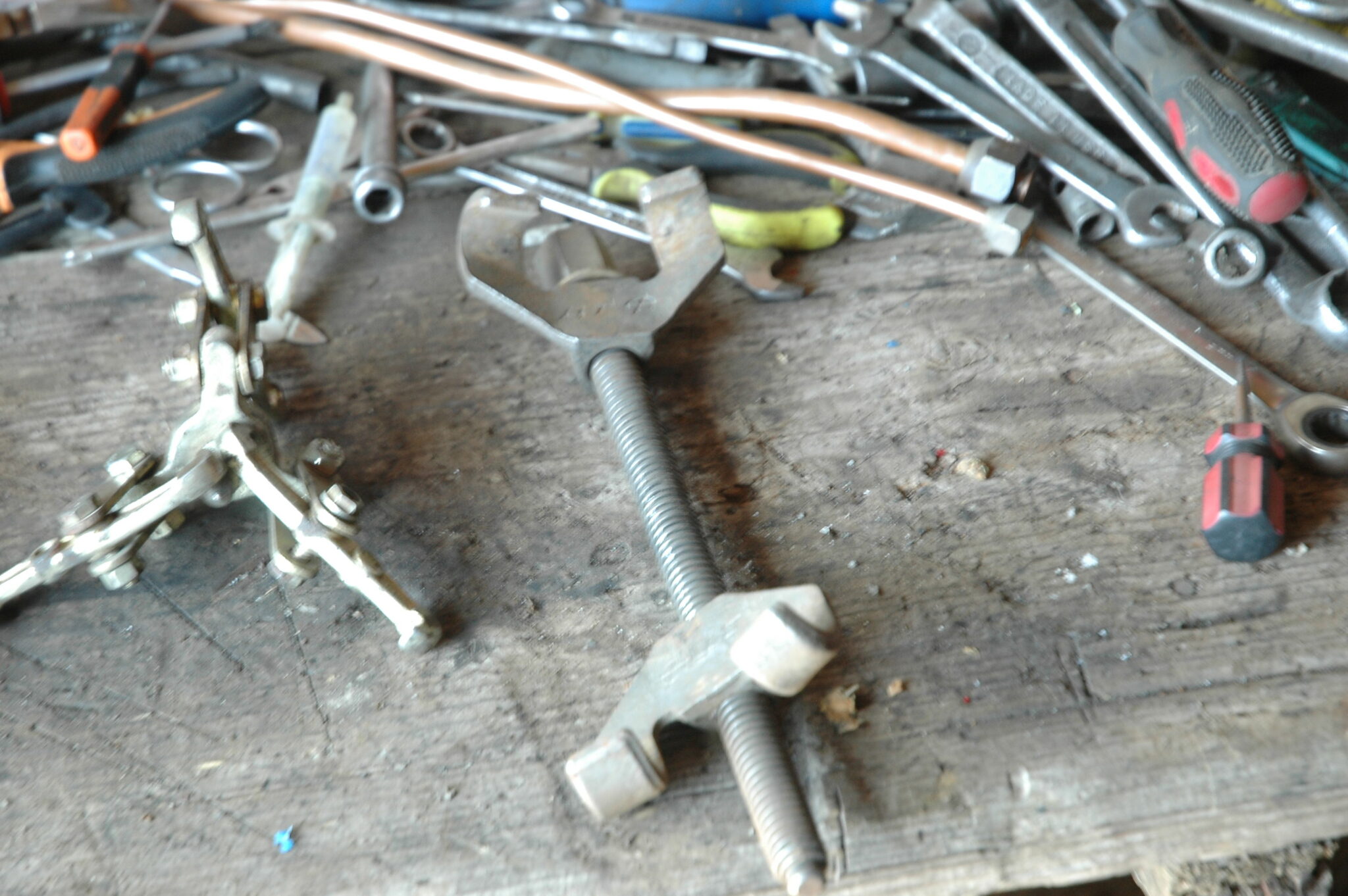
Three-arm bearing puller and shock absorber spring tensioner
The gradation of mechanical devices is according to the number of grips (two- or three-legged) and the method of engagement (external or internal).
In addition, there are rotary and self-centering structures, devices such as "pantograph" and others.
Double grip
The stability of removable accessories is determined by the number of grips. Two-grip (two-legged) devices have a monolithic design with two supporting paws. The main nodes are made by forging.
Do-it-yourself VAZ hub bearing puller with two grips is made for a specific size of the part to be removed, or for a universal device. Homemade products are used for the accurate dismantling of tight bearings in hard-to-reach places. It is better to make the paws mobile due to the hinge mechanism, couplers or traverse.
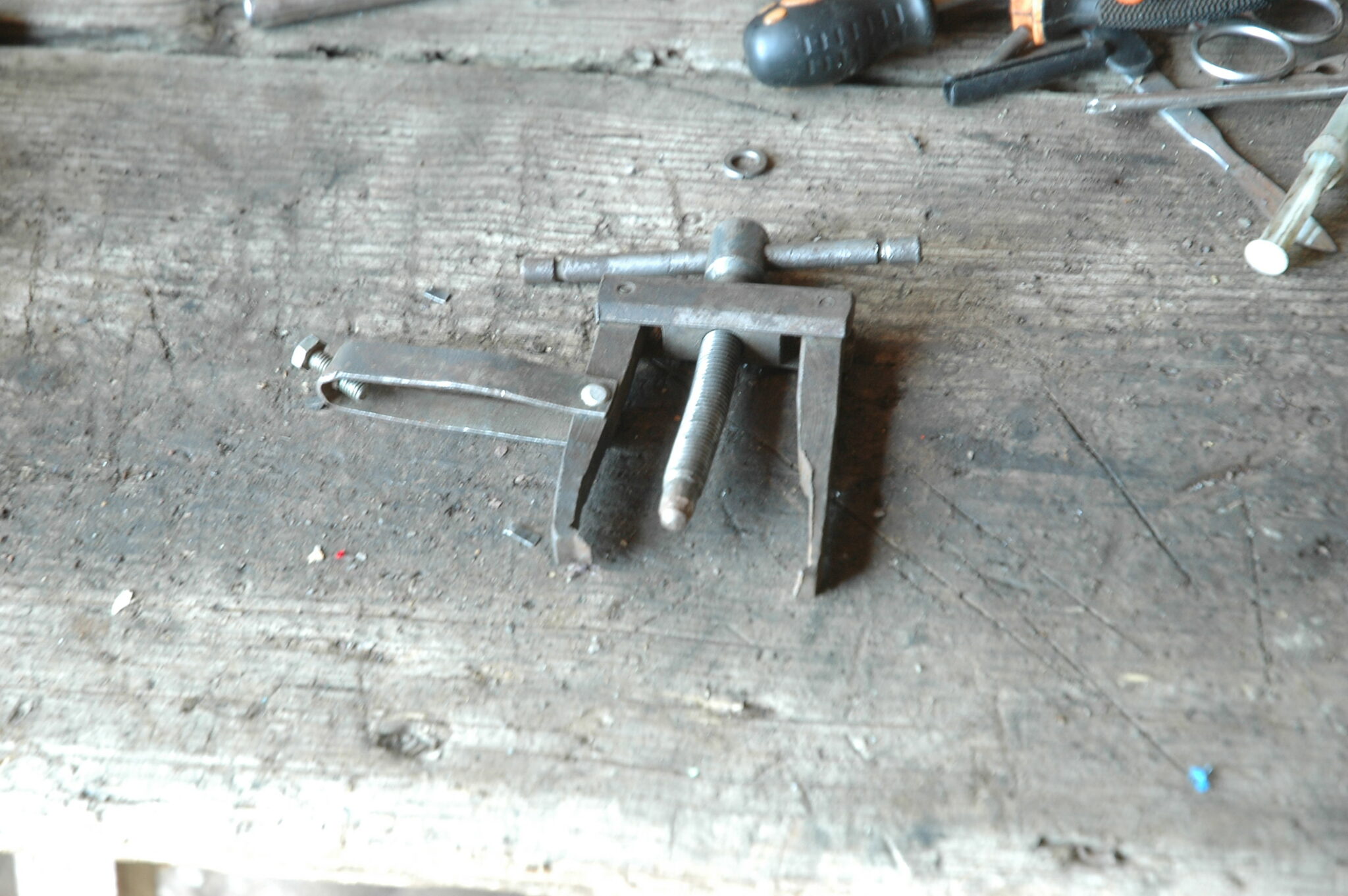
Two-arm puller
Pressers differ in the following characteristics:
- type of attachment of paws;
- tip shape;
- capture length;
- screw dimensions (diameter, length);
- manufacturing material.
Triangular
In terms of strength, this design is superior to 2-arm pull-outs, as it is made of forged reinforced steel. The vypressovshchik carefully removes the part from the recess, while the physical costs of the master are minimal.
Swivel pullers are very popular among professionals and amateurs. The tool is easily adjusted to the diameter of the removed auto part (you just need to move the grips apart), centering occurs automatically.
Most often, the bearing is removed by grabbing it by the outer ring. But it is possible to hook the element on the inner ring with a special puller and pull it out of the housing.
In this case, determine the size of the bearing bore and the type of grips. If there is a supporting surface, then it is more convenient to take a 3-legged tool, at the end of the grips of which there are bends on the outer and inner sides.
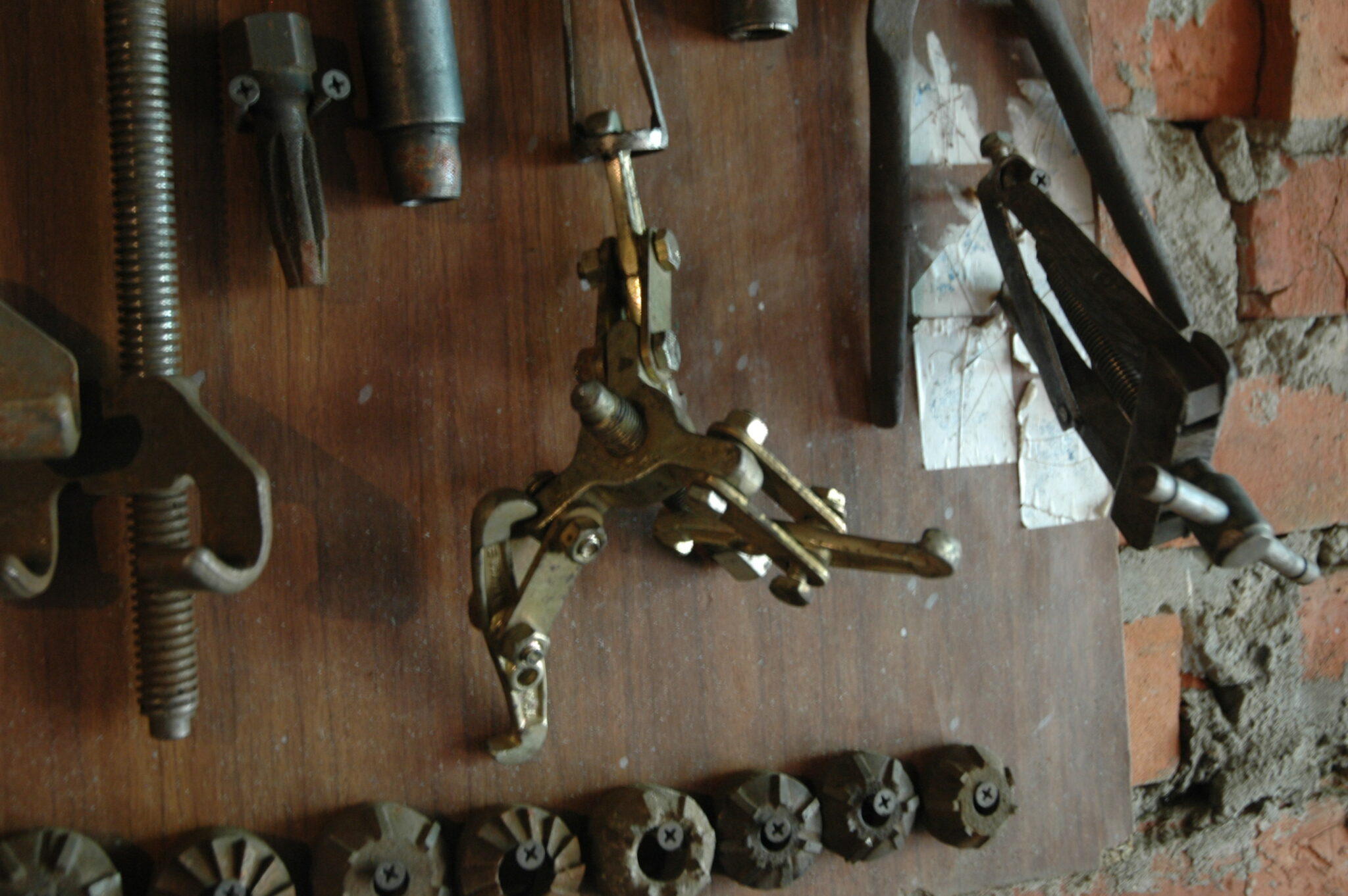
Three-legged puller - vypressovshchik
However, you can make your own do-it-yourself inner bearing puller from two wrenches, four plates, threaded studs, bolts and nuts.
Materials for manufacturing
The bearing is an element that you cannot take with “bare hands”. Therefore, the material of manufacture is only durable high-alloy steel. The central body, the power bolt, has an even greater strength.
The following materials will be required for the job:
- two metal blanks of square section;
- a pair of steel plates;
- two bolts with nuts;
- release bolt with a working nut of a suitable diameter.
Tools: welding machine, grinder, electric drill with a set of drills.
Step-by-step process
A self-made mechanism will replenish the set of locksmith fixtures for an auto mechanic. You can make a VAZ 2108 wheel bearing puller with your own hands in an hour.
Work step by step:
- Prepare “fingers”-grabs from the blanks: leave the shank square, grind the rods so that bends are obtained at the ends.
- Drill holes in the tails.
- Drill holes along the edges of the plates as well.
- Using welding, secure between the plates, exactly in the middle, the working nut.
- Insert the “fingers” between the plates so that the holes of the parts match and the bends look inward.
- Fasten the blanks and plates with bolts and nuts.
- Screw the power pin into the working nut.
- At its rear end, weld the collar.
The design for replacing bearings is assembled. Do not overtighten the bolts that connect the hooks to the plates - leave the grips movable.
At the last stage, give the instrument an aesthetic look: treat it with sandpaper and an anti-corrosion compound. Lubricate the threads to make it easier to pass the working nut.
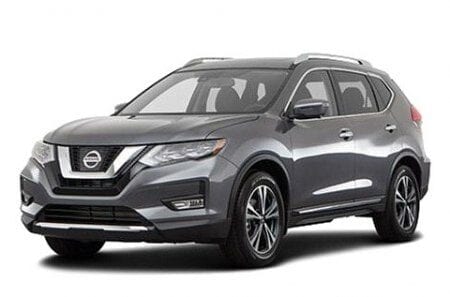
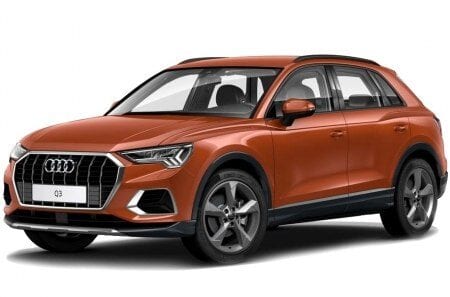