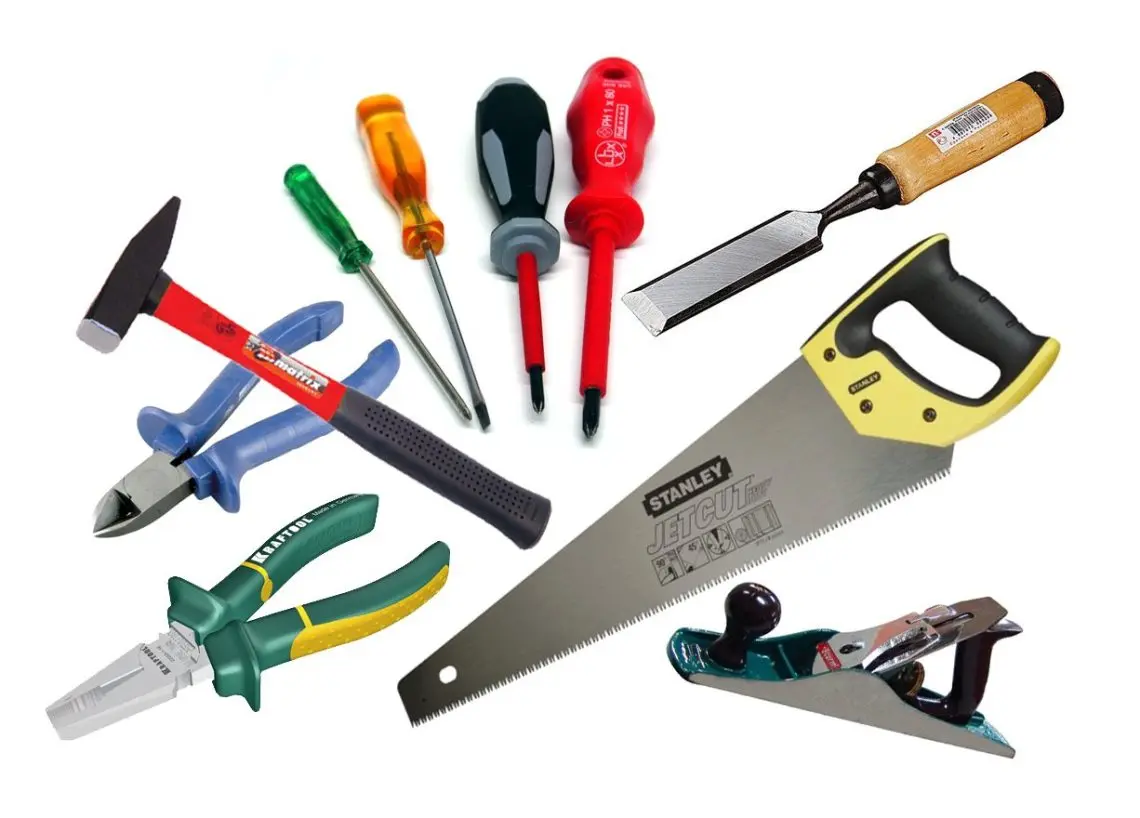
Knock sensor circuit
Content
This guide will discuss the knock sensor circuit and how it works. Knock sensors play an integral role in cars and you need to understand them well.
As an experienced mechanical engineer, I have worked on numerous knock sensor projects and learned a few tips and tricks along the way. The knock sensor (vibration sensor) is a simple device that detects vibrations or shocks when tapped or tapped. This is an electronic switch that is normally on. It closes when any shock or vibration is detected.
Brief summary: A typical knock sensor consists of a conductive vibrating spring as the main sensing element, a resistor, and three pins. The knock sensor module has 3 pins: GND, +5V and S.
I'll cover more below.
What is a knock sensor?
The knock sensor detects engine cylinder vibrations caused by detonation and sends an electrical signal to the ECM (engine control module).
When the ECM receives an electrical signal, it retards the ignition timing or ignition timing and prevents knocking in the engine.
The electrical signal voltage of the knock sensor is proportional to the strength of the knock. So the knock sensor helps the engine by sending knock signals to the ECM as knocking will harm the engine. This is because the heat and vibrations that occur when an engine knocks damage engine components.
Knock sensor circuit
Knock sensor location: The knock sensor is attached to the cylinder block or to the cylinder head.
The principle of operation of the knock sensor
The knock sensor is a piezoelectric type sensor that detects vibrations generated inside the engine due to knocking and sends electrical signals to the ECM.
When the ECM receives voltage signals from the engine, it retards the ignition timing. As a result, ignition starts closer to TDC than before, which reduces knocking in the engine.
The knock sensor reduces peak pressure and temperature inside the engine by delaying ignition timing, which stops knocking.
The roles of the knock sensor
- The roles of the knock sensor
- To reduce energy waste
- To improve fuel efficiency
- To increase the output torque
- To detect vibrations in the engine
knock sensor components
The knock sensor consists of the following main components (knock sensor design):
Piezoelectric element
The ceramic disc is a piezoelectric element. When the piezo element is subjected to pressure during the vibration of the motor, an electrical charge builds up in it.
contact discs
The contact discs of the piezoelectric element are located on both sides. Contact discs help transfer electrical charge from the piezoelectric element to the contacts.
seismic mass
The pressure on the seismic material changes continuously and rhythmically due to the inertia of the seismic mass during engine vibration. As a result, the piezoelectric element picks up the change in pressure, causing an electrical charge to build up in the element.
How does a knock sensor work?
The knock sensor is attached to the cylinder block with screws. When the engine starts knocking, high pressure and vibrations occur. An electric charge begins to accumulate inside the piezoelectric element due to strong vibrations.
The piezoelectric element has contact discs on both sides, so the electrical charge generated inside the element travels from the contact discs to the terminals, which are then connected to the ECM (engine control module).
The magnitude of the voltage of the electric charge is determined by the intensity of the vibrations produced by the knock.
When the ECM receives an electrical signal from the knock sensor, it delays ignition advance until knock stops. As a result, ignition occurs closer to TDC than before, and the knocking in the engine stops.
When the knock stops, the ECM returns to the previous ignition timing.
Applications, advantages and disadvantages of knock sensors
Statement
The knock sensor is used in many types of two-wheelers, four-wheelers, and construction machinery engines to prevent knocking.
benefits
The knock sensor has the following advantages
- Reduces the chance of knocking
- Improves power and fuel economy
- Reduces engine vibrations caused by engine knock.
- Protects engine components from damage caused by engine knock.
- Reduces the amount of unburned gas emitted.
- Increases engine performance
Disadvantages of a no deposit bonus
The knock sensor has the following disadvantages
- Noise generation during detonation reduces accuracy. (1)
- Requires regular maintenance.
- High price.
- More complications.
- Over time, they wear out, requiring costly replacements.
Some Frequently Asked Questions - Frequently Asked Questions
What effect does the knock sensor have on the engine?
The knock sensor detects engine vibrations caused by knocking and sends an electrical signal to the ECM. The ECM then retards the ignition timing to reduce engine knock.
Do you need a knock sensor?
Yes, a knock sensor is needed in an internal combustion engine to reduce engine knock. As a result, engine performance is improved.
What happens if the knock sensor fails?
When the knock sensor fails, the engine consumes more fuel, resulting in less acceleration and reduced engine power output.
What causes a knock sensor to fail?
The knock sensor fails primarily due to a broken knock sensor wire and improper installation.
What are the symptoms of a faulty knock sensor?
A faulty knock sensor causes an audible knock in the engine, the "Check Engine" light comes on, and an increase in engine fuel consumption, among other symptoms. (2)
Take a look at some of our articles below.
- How to check a knock sensor with a multimeter
- What does a bad knock sensor sound like?
- Symptoms of a bad plug wire
Recommendations
(1) Accuracy - https://blog.paperspace.com/deep-learning-metrics-precision-recall-accuracy/
(2) fuel consumption - https://www.sciencedirect.com/topics/earth-and-planetary-sciences/fuel-consumption
Video links


Watch this video on YouTube

