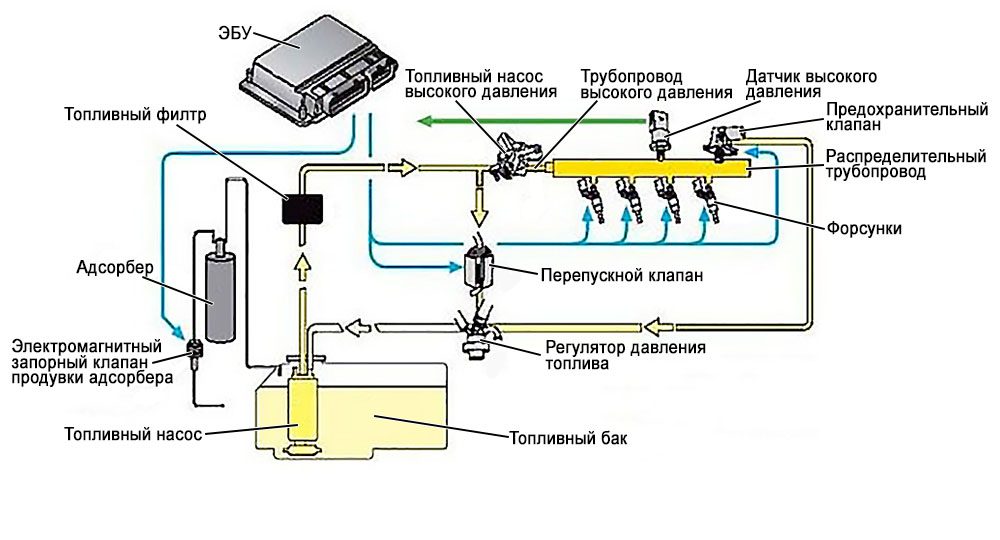
Diesel engine injection system - direct injection with rotary pump VP 30, 37 and VP 44
Content
Constantly rising fuel prices have pushed manufacturers to step up the development of diesel engines. Until the late 80s, they played only second violin besides gasoline engines. The main culprits were their bulkiness, noise and vibration, which were not compensated by even significantly lower fuel consumption. The situation should have been aggravated by the forthcoming tightening of legal requirements to reduce emissions of pollutants in exhaust gases. As in other fields, the omnipotent electronics has lent a helping hand to diesel engines.
In the late 80s, but especially in the 90s, the electronic diesel engine control (EDC) was gradually introduced, which significantly improved the performance of diesel engines. The main advantages turned out to be better fuel atomization achieved through higher pressure, as well as electronically controlled fuel injection in accordance with the current situation and the needs of the engine. Many of us remember from real-life experience what a "go-ahead" was a good call for the commissioning of the legendary 1,9 TDi engine. Like a magic wand, the hitherto bulky 1,9 D / TD has become a nimble athlete with extremely low energy consumption.
In this article we will tell you how a rotary injection pump works. We will first explain how mechanically controlled rotary lobe pumps work and then electronically controlled pumps. An example is the injection pump from Bosch, which has been and remains the pioneer and largest manufacturer of injection systems for diesel engines in passenger cars.
The injection unit with a rotary pump supplies fuel simultaneously to all cylinders of the engine. The distribution of the fuel to the individual injectors is carried out by a distributor piston. Depending on the movement of the piston, rotary lobe pumps are divided into axial (with one piston) and radial (with two to four pistons).
Rotary injection pump with axial piston and distributors
For the description, we will use the well-known Bosch VE pump. The pump consists of a feed pump, a high pressure pump, a speed controller and an injection switch. The feed vane pump delivers fuel to the pump suction space, from where the fuel enters the high pressure section, where it is compressed to the required pressure. The distributor piston performs a sliding and rotational movement at the same time. The sliding motion is caused by an axial cam firmly connected to the piston. This allows fuel to be sucked in and supplied to the high pressure line of the engine fuel system through the pressure valves. Due to the rotational movement of the control piston, it is achieved that the distribution groove in the piston rotates opposite the channels through which the high pressure line of the individual cylinders is connected to the pump head space above the piston. Fuel is sucked in during the movement of the piston to the bottom dead center, when the cross-sections of the intake duct and grooves in the piston are open to each other.
Rotary injection pump with radial pistons
The rotary pump with radial pistons provides higher injection pressure. Such a pump contains from two to four pistons, which move the cam rings, which are fixed in the piston in their cylinders, towards the injection switch. The cam ring has as many lugs as the given engine cylinder. As the pump shaft rotates, the pistons move along the trajectory of the cam ring with the help of rollers and push the cam protrusions into the high pressure space. The rotor of the feed pump is connected to the drive shaft of the injection pump. The feed pump is designed to supply fuel from the tank to the high pressure fuel pump at the pressure necessary for its correct operation. The fuel is supplied to the radial pistons through the distributor rotor, which is rigidly connected to the injection pump shaft. On the axis of the distributor rotor there is a central hole that connects the high pressure space of the radial pistons with transverse holes for supplying fuel from the feed pump and for discharging high pressure fuel to the injectors of the individual cylinders. The fuel comes out into the nozzles at the moment of connecting the cross-sections of the rotor bore and the channels in the pump stator. From there, the fuel flows through a high-pressure line to the individual injectors of the engine cylinders. The regulation of the amount of injected fuel occurs by limiting the flow of fuel flowing from the feed pump to the high pressure part of the pump.
Electronically Controlled Rotary Injection Pumps
The most common electronically controlled high-pressure rotary pump used in vehicles in Europe is the Bosch VP30 series, which generates high pressure with an axial piston motor, and the VP44, in which it creates a positive displacement pump with two or three radial pistons. With an axial pump it is possible to achieve a maximum nozzle pressure of up to 120 MPa, and with a radial pump up to 180 MPa. The pump is controlled by the electronic engine control system EDC. In the early years of production, the control system was divided into two systems, one of which was controlled by the engine management system, and the other by the injection pump. Gradually, one common controller located directly on the pump began to be used.
Centrifugal pump (VP44)
One of the most common pumps of this type is the VP 44 radial piston pump from Bosch. This pump was introduced in 1996 as a high pressure fuel injection system for passenger cars and light commercial vehicles. The first manufacturer to use this system was Opel, which installed a VP44 pump in the four-cylinder diesel engine of its Vectra 2,0 / 2,2 DTi. This was followed by Audi with a 2,5 TDi engine. In this type, the start of the injection and the regulation of the fuel consumption are fully electronically controlled by means of solenoid valves. As already mentioned, the entire injection system is controlled either by two separate control units, separately for the engine and pump, or one for both devices located directly in the pump. The control unit (s) processes signals from a number of sensors, which is clearly seen in the figure below.
From a design point of view, the principle of operation of the pump is essentially the same as that of a mechanically driven system. The high-pressure fuel pump with radial distribution consists of a vane-chamber pump with a pressure control valve and a flow throttle valve. Its task is to suck up fuel, create pressure inside the accumulator (approximately 2 MPa) and refuel with a high-pressure radial piston pump that creates the necessary pressure for fine atomization-injection of fuel into the cylinders (up to approximately 160 MPa). ). The camshaft rotates together with the high-pressure pump and supplies fuel to the individual injector cylinders. A fast solenoid valve is used to measure and regulate the amount of fuel injected, which is controlled by signals with a variable pulse frequency via the el. the unit is located on the pump. The opening and closing of the valve determines the time during which fuel is supplied by the high pressure pump. Based on the signals from the reverse angle sensor (angular position of the cylinder), the instantaneous angular position of the drive shaft and the cam ring during reversing is determined, the rotation speed of the injection pump (in comparison with the signals from the crankshaft sensor) and the position of the injection switch in the pump are calculated. The solenoid valve also adjusts the position of the injection switch, which rotates the cam ring of the high pressure pump accordingly. As a result, the shafts driving the pistons sooner or later come into contact with the cam ring, which leads to an acceleration or delay in the start of compression. The injection changeover valve can be opened and closed continuously by the control unit. The steering angle sensor is located on a ring that rotates synchronously with the cam ring of the high pressure pump. The pulse generator is located on the pump drive shaft. The jagged points correspond to the number of cylinders in the engine. When the camshaft rotates, the shift rollers move along the surface of the cam ring. The pistons are pushed inward and pressurize fuel to high pressure. Compression of fuel under high pressure begins after the opening of the solenoid valve by a signal from the control unit. The distributor shaft moves to a position in front of the compressed fuel outlet to the corresponding cylinder. The fuel is then piped through the throttle check valve to the injector, which injects it into the cylinder. The injection ends with the closing of the solenoid valve. The valve closes approximately after overcoming the bottom dead center of the pump radial pistons, the start of the pressure rise is controlled by the cam overlap angle (controlled by the injection switch). Fuel injection is influenced by speed, load, engine temperature and ambient pressure. The control unit also evaluates information from the crankshaft position sensor and the drive shaft angle in the pump. The control unit uses the angle sensor to determine the exact position of the drive shaft of the pump and the injection switch.
1. - Vane extrusion pump with pressure control valve.
2. – rotation angle sensor
3. - pump control element
4. - high pressure pump with camshaft and drain valve.
5. - injection switch with switching valve
6. - high pressure solenoid valve
Axial pump (VP30)
A similar electronic control system can be applied to a rotary piston pump, such as the Bosch type VP 30-37 pump, which has been used in passenger cars since 1989. In a VE axial flow fuel pump controlled by a mechanical eccentric governor. the effective travel and fuel dose determine the position of the gear lever. Of course, more precise settings are achieved electronically. The electromagnetic regulator in the injection pump is a mechanical regulator and its additional systems. The control unit determines the position of the electromagnetic regulator in the injection pump, taking into account signals from various sensors that monitor the performance of the engine.
Finally, a few examples of the mentioned pumps in specific vehicles.
Rotary fuel pump with axial piston motor VP30 uses e.g. Ford Focus 1,8 TDDi 66 kW
VP37 uses a 1,9 SDi and TDi engine (66 kW).
Rotary injection pump with radial pistons VP44 used in vehicles:
Opel 2,0 DTI 16V, 2,2 DTI 16V
Audi A4 / A6 2,5 TDi
BMW 320d (100 kW)
A similar design is a rotary injection pump with Nippon-Denso radial pistons in the Mazde DiTD (74 kW).
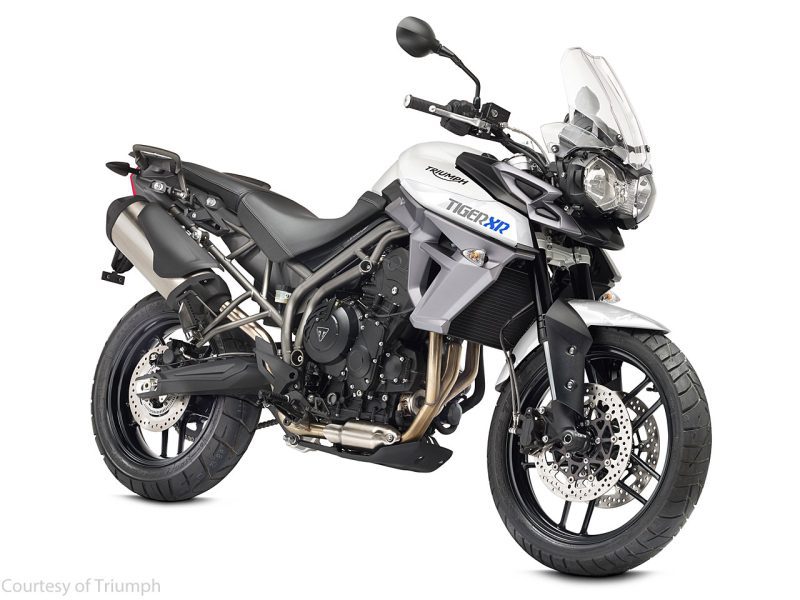
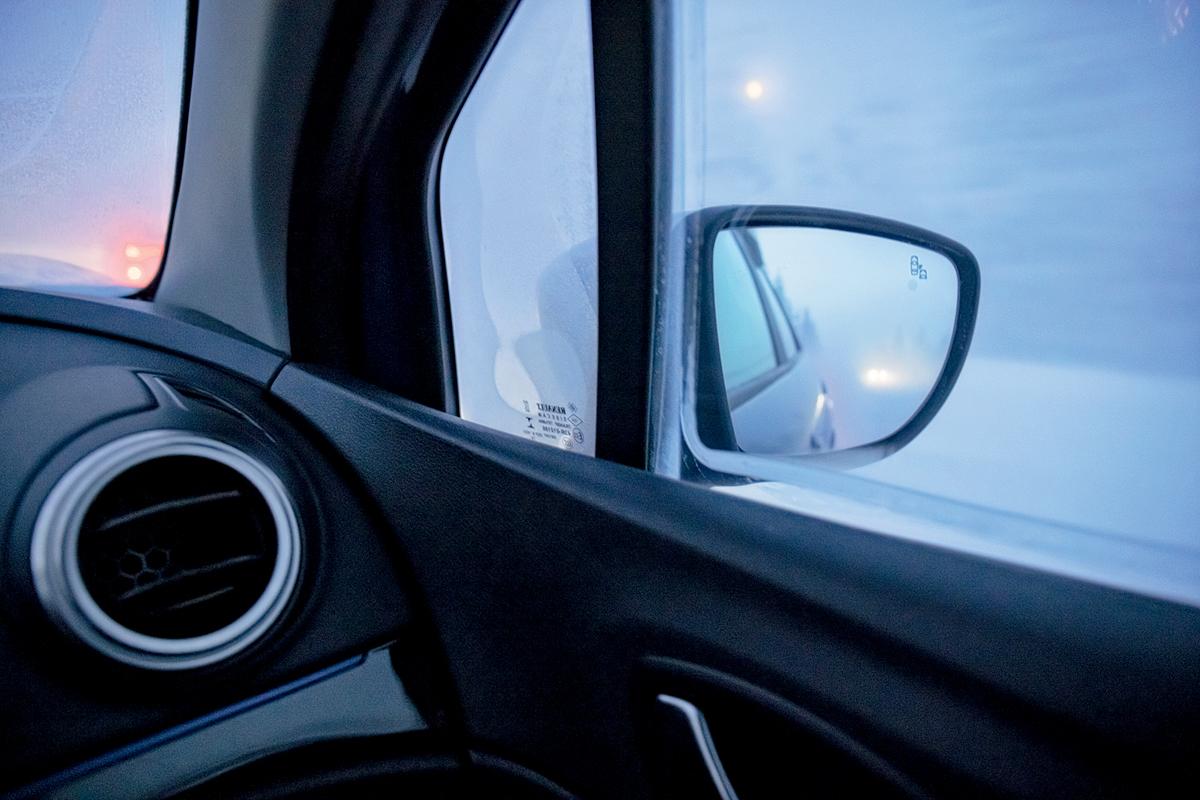