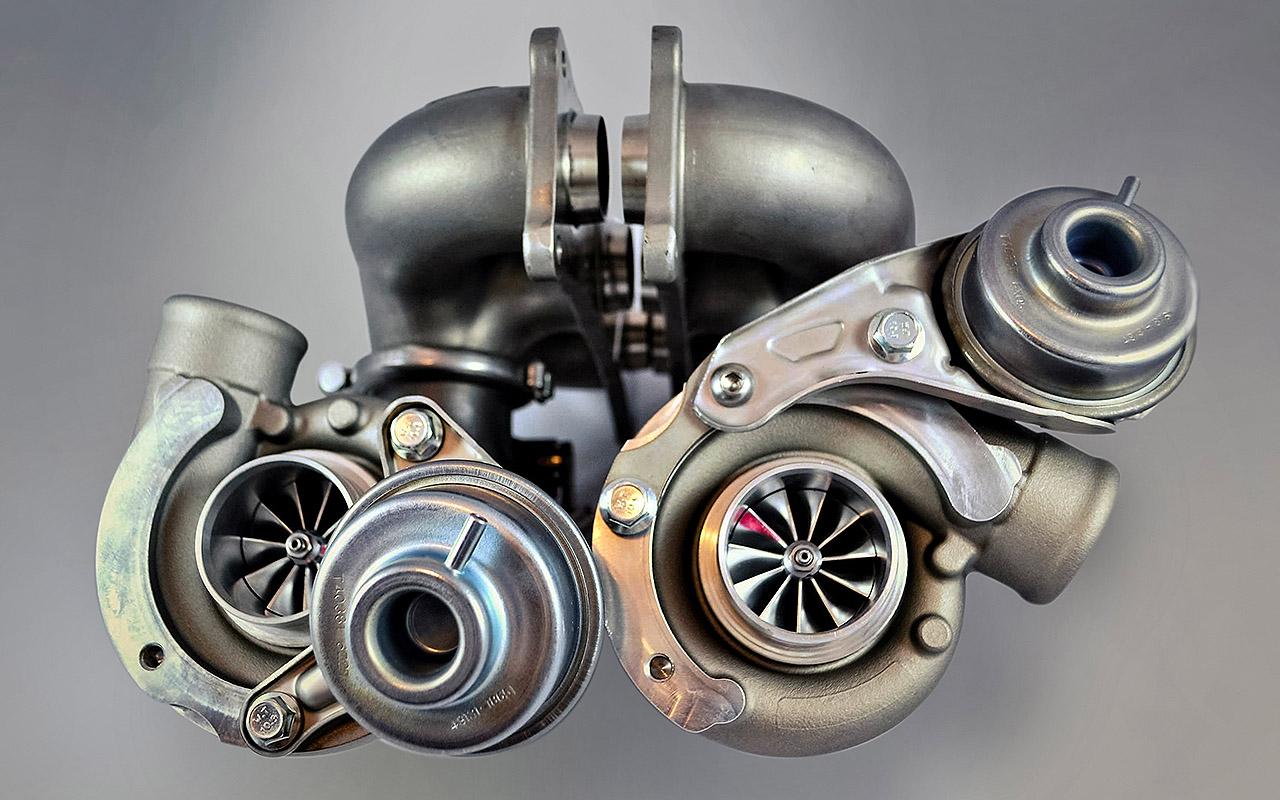
Reduction. Turbo in a small engine. The whole truth about modern technology
Content
It is now almost standard for manufacturers to install low-powered powertrains in cars, even the likes of the Volkswagen Passat or Skoda Superb. The idea of reduction has evolved for the better, and time has shown that this solution works every day. An important element in this type of engine is, of course, the turbocharger, it allows you to achieve relatively high power with little power at the same time.
operating principle
The turbocharger consists of two simultaneously rotating rotors mounted on a common shaft. The first one is installed in the exhaust system, the exhaust gases provide movement, enter the mufflers and are thrown out. The second rotor is located in the intake system, compresses the air and pressurizes it into the engine.
This pressure must be controlled so that too much of it does not enter the combustion chamber. Simple systems use the shape of a bypass valve, while advanced designs, i.e. the most common use blades with variable geometry.
See also: Top 10 ways to reduce fuel consumption
Unfortunately, the air at the time of high compression is very hot, besides, it is heated by the turbocharger housing, which in turn reduces its density, and this adversely affects the proper combustion of the fuel-air mixture. Therefore, manufacturers use, for example, an intercooler, whose task is to cool the heated air before it enters the combustion chamber. As it cools, it thickens, which means that more of it can get into the cylinder.
Eaton compressor and turbocharger
In an engine with two superchargers, a turbocharger and a mechanical compressor, they are installed on both sides of the engine. This is due to the fact that the turbine is a high-temperature generator, so the optimal solution is to install a mechanical compressor on the opposite side. The Eaton compressor supports the operation of the turbocharger, is driven by a multi-ribbed belt from the main water pump pulley, which is equipped with a maintenance-free electromagnetic clutch responsible for activating it.
Appropriate internal proportions and the ratio of the belt drive cause the compressor rotors to rotate at five times the speed of an automobile drive crankshaft. The compressor is attached to the engine block on the intake manifold side, and the regulating throttle doses the amount of pressure generated.
When the throttle is closed, the compressor generates maximum pressure for the current speed. Compressed air is then forced into the turbocharger and the throttle opens at too much pressure, which separates the air into the compressor and turbocharger.
Difficulties of work
The aforementioned high operating temperature and variable loads on structural elements are factors that mainly negatively affect the durability of the turbocharger. Improper operation leads to faster wear of the mechanism, overheating and, as a result, failure. There are several tell-tale symptoms of a turbocharger malfunction, such as a louder "whistling", sudden loss of power on acceleration, blue smoke from the exhaust, going into emergency mode, and an engine error message called "bang". "Check engine" and also lubricate with oil around the turbine and inside the air intake pipe.
Some modern small engines have a solution to protect the turbo from overheating. To avoid heat accumulation, the turbine is equipped with coolant channels, which means that when the engine is turned off, the liquid continues to flow and the process continues until the appropriate temperature is reached, in accordance with the thermal characteristics. This is made possible by an electric coolant pump that operates independently of the internal combustion engine. The engine controller (through a relay) regulates its operation and activates it when the engine reaches a torque of more than 100 Nm and the air temperature in the intake manifold is more than 50 ° C.
turbo hole effect
The disadvantage of some supercharged engines with higher power is the so-called. turbo lag effect, i.e. a temporary decrease in engine efficiency at the time of takeoff or the desire to accelerate sharply. The larger the compressor, the more noticeable the effect, because it needs more time for the so-called “Spinning”.
A small engine develops power more vigorously, the installed turbine is relatively small, so that the described effect is minimized. Torque is available from low engine speeds, which ensures comfortable operation, for example, in urban conditions. For example, in a VW 1.4 TSI engine with 122 hp. (EA111) already at 1250 rpm, about 80% of the total torque is available, and the maximum boost pressure is 1,8 bar.
Engineers, wanting to completely solve the problem, developed a relatively new solution, namely an electric turbocharger (E-turbo). This system is increasingly appearing in low power engines. The method is based on the fact that the rotor, which drives the air injected into the engine, rotates with the help of an electric motor - thanks to this, the effect can be practically eliminated.
True or myth?
Many people are concerned that turbochargers found in undersized engines can fail faster, which may be due to the fact that they are overloaded. Unfortunately, this is a frequently repeated myth. The truth is that longevity depends a lot on how you use, drive and change your oil - about 90% of the damage is caused by the user.
It is assumed that cars with a mileage of 150-200 thousand km belong to the group of increased risk of failure. In practice, many cars have traveled more than a kilometer, and the described unit has been working flawlessly to this day. Mechanics claim that an oil change every 30-10 kilometers, i.e. Long Life, has a negative impact on the condition of the turbocharger and the engine itself. So we will reduce the replacement intervals to 15-XNUMX thousand. km, and use oil in accordance with the recommendations of your car manufacturer, and you can enjoy trouble-free operation for a long time.
Possible regeneration of the element costs from PLN 900 to PLN 2000. A new turbo costs much more - even more than 4000 zł.
See also: Fiat 500C in our test
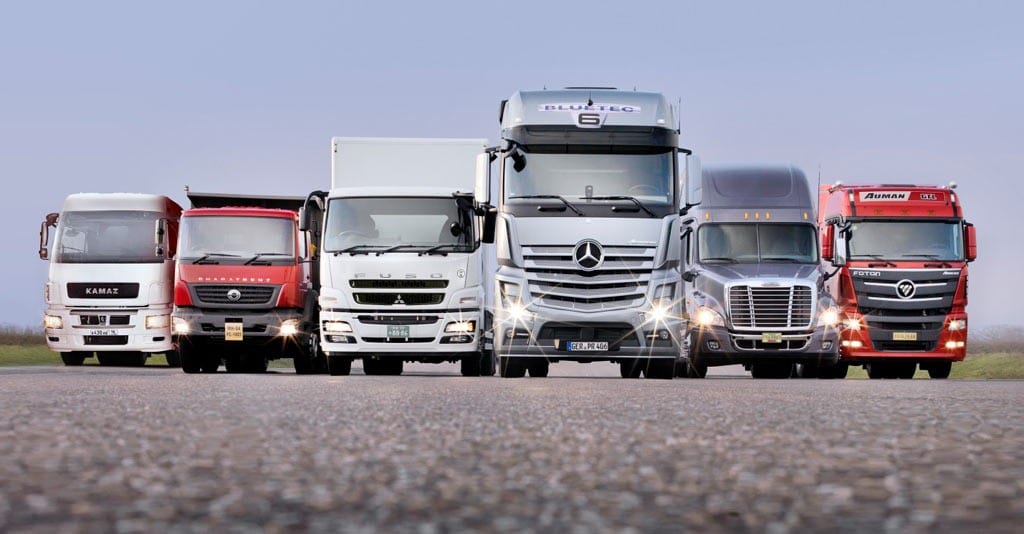
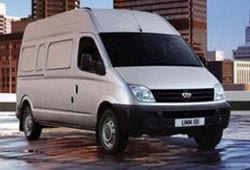