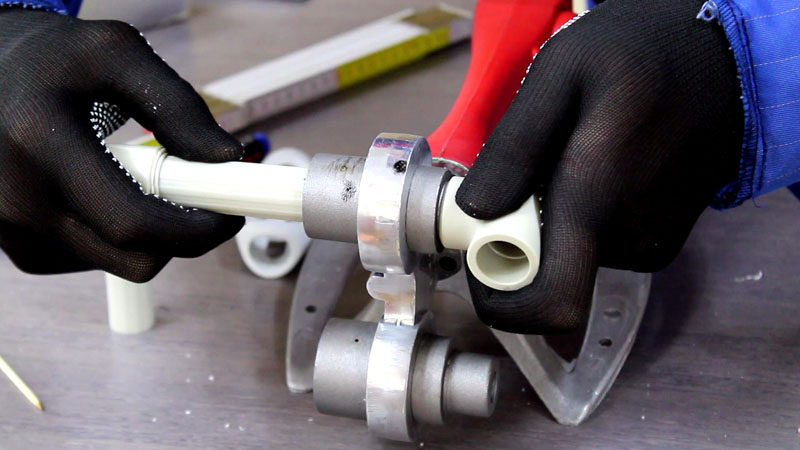
Do-it-yourself plastic welding - how to connect plastic elements with a welding machine?
Content
- Bonding of plastics and other ways of joining materials
- plastic welding temperature
- Type of binder and welding electrodes
- Welding equipment in workshop
- Accessories for thermoplastic welding
- Skills and abilities
- Welding plastic step by step
- Plastic Welding Mistakes to Avoid
- Where is plastic welding most commonly used?
- The price of plastic welding - how much does it cost?
- Plastic welder and joint strength
Does welding plastic sound a little weird? Although at first glance this may come as a surprise, this combination of elements is fully consistent with Art. This method is used in construction, automotive and industry. You can also weld these items in your home garage or workshop. We offer what you need to get started. Check out what you need to do step by step to weld the elements of your car!
Bonding of plastics and other ways of joining materials
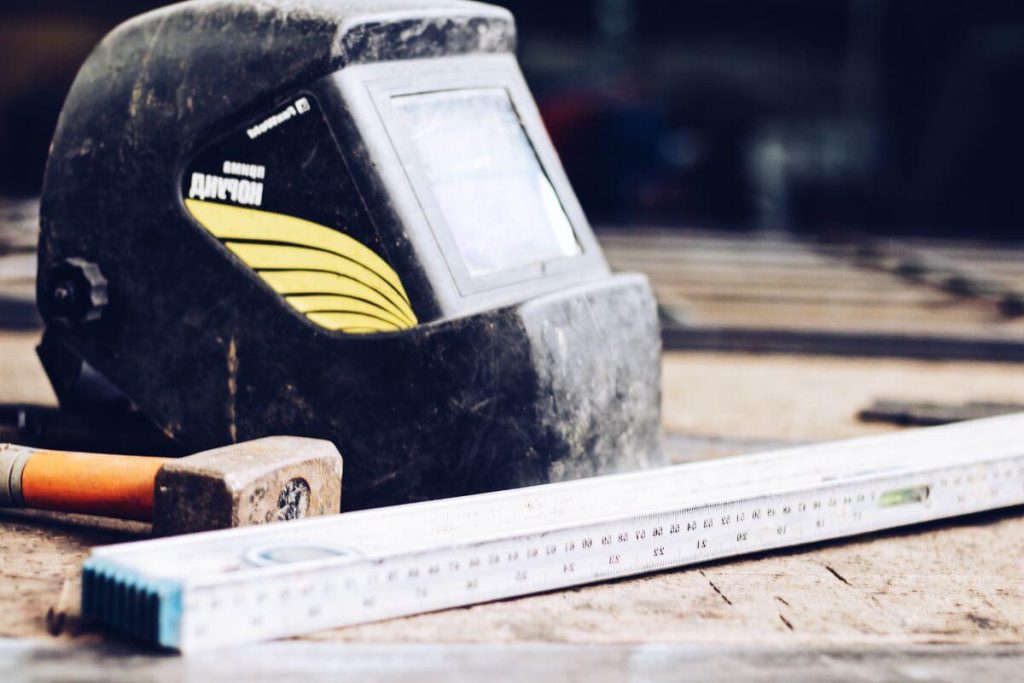
Plastic parts are usually glued together. This is especially true for small objects that are not subject to large overloads. Adhesives are also used for materials that do not need to be particularly dense or aesthetically pleasing. How to glue plastic in other ways? For this, welding machines with clamps can be used, which are placed between two separable elements. Under the action of the flowing current, the clip inside melts and a permanent connection is created.
Welding and plastic welding
It is also common practice (eg in plumbing) to weld plastic. It is the process of heating two objects and fusing them under pressure. In this way, for example, PP or PVC pipes are connected to each other or to elbows or branch pipes. The last solution is plastic welding. It is no different from the traditional connection of metals. The plastic binder allows you to create a permanent combination of two or more elements. And it is on this method that we will focus in our article.
plastic welding temperature
Of fundamental importance is the choice of operating parameters of the device for superimposed anastomosis. To do this, you need to know the plastic being welded and its melting point. The most popular ones are listed below:
- PE (polyethylene) - 110°С-180°С;
- PP (polypropylene) – 160°C;
- PVC (polyvinyl chloride) - 180°C-270°C;
- PC (polycarbonate) - 230°С;
- ABS (acrylobutylstyrene) - 240°С;
- PA (polyamide) - 255°С;
- PTFE - 325°С.
Type of binder and welding electrodes
The electrode must always be made of the same material as the plastic items to be welded. Otherwise, all the work will be wasted and the result will not be executed properly. If you want to weld, you must also choose the correct filler metal width to keep the joint tight and strong. This parameter is also related to the size of the high speed welding nozzle.
Welding equipment in workshop
Which welding machine is suitable? It all depends on the level of sophistication of the operator and the frequency of welding. The simplest devices, which can also be called heat guns, should not cost more than 10 euros, they are usually equipped with nozzles for various types of binder and are powered by a network. Can also be welded with cartridge gas welding machines. There are also battery powered devices as well as professional welding stations for use in service businesses. Their welding requires practice. The price of these devices reaches several thousand zlotys.
Also check the information about welding aluminum rims here: https://spawam.pl/spawanie-felg-aluminiowych
Accessories for thermoplastic welding
What are we talking about in this case? To repair plastic, not only a welding machine is required, but also surface grinding tools. Usually narrow and wide scrapers are sufficient, as well as an electric grinder with plastic tips. With their help, you will remove the oxidized surface and prepare it for welding.
Skills and abilities
It is difficult for you to have welding practice if you have not worked with a welding machine before. However, you have nothing to worry about, because after reading this guide, you will know what mistakes to avoid and how to make welds. For training, you will need the simplest devices that can be used to weld plastics.
Welding plastic step by step
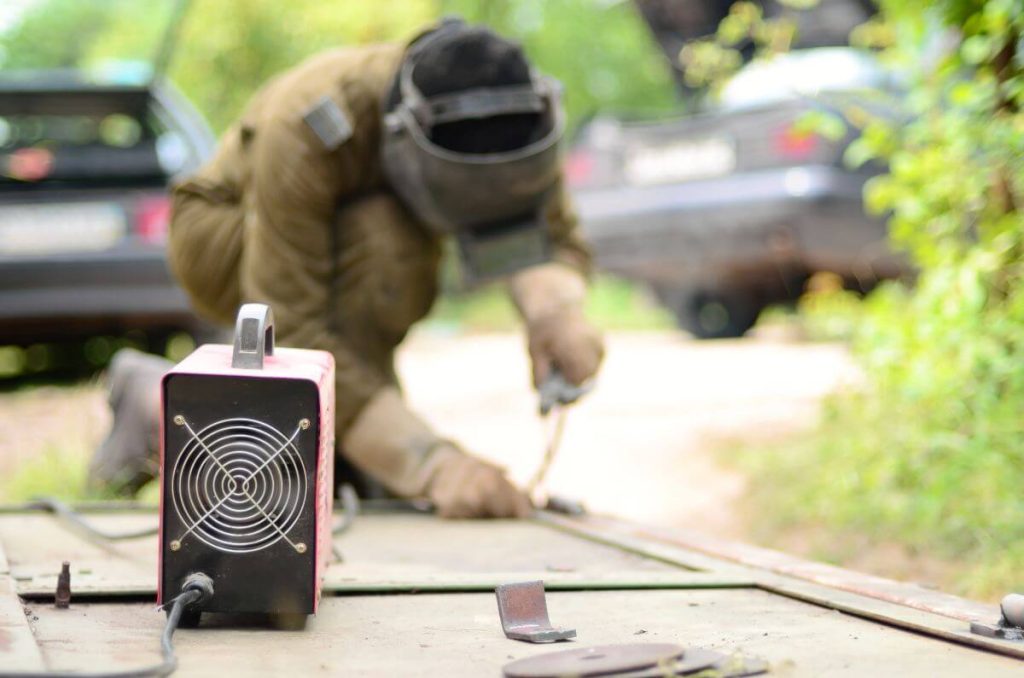
There are a few things to decide before you start making your first plastic weld. Check what you need to do step by step once you decide to get started.
Welding of ABS and other plastics - preparation of the base
It is impossible to connect the elements well without first cleaning them. This applies not only to plastics, but also to metals. Therefore, start welding by cleaning the surface. You can even wash it if you need to. This may be especially important in the case of items in which oils or liquids have been present. After thorough drying, the upper oxides must also be removed from the element. Grinding and slightly blunting objects will allow the element to be welded to effectively connect to the weld. Use scrapers and a grinder for this. Finally, carefully dedust the surface.
Welding plastic with a soldering iron and a welder - primary joining of elements
If the elements have never been merged together, it is recommended that you perform an initial merging first. To do this, use a pre-weld nozzle with a special wedge that will pass between adjacent materials. This will initially stabilize the products and prepare the station for the main welding using a plastic binder. Before welding plastic elements, set the device to the desired plastic melting temperature and wait until the tip heats up. It is good to weld in one motion, without tearing the element from the objects to be welded. Try to keep the welder at a constant angle, preferably 45°.
Hot plastic bonding - basic welding
Now it's time to make the main weld.
- Measure the required binding length with a margin of several centimeters. It will be good if you have a fast welding tip, because this way the application of putty will be the most accurate.
- Warm up the device and place the element inside. You can release the binder a little outside the contour so that the plastic has perfect contact with the surfaces to be joined in the place where there is no connection.
- Then, with slow but sure movements, run the welder along the crack.
Repair of plastic by pendulum welding
If you do not have a high speed welding tip or if it is not suitable for the welding method, the pendulum method is the best choice. Seam sealants here must be applied and plasticized manually. Don't forget to weld the elements on the bottom so that the surfaces can join. In this repair method, it is also necessary to take into account the correct pressure of the binder, otherwise the weld will break.
Finishing welds
After all the parts have cooled, you can start grinding them. To do this, use scrapers or an electric grinder and get rid of excess welds. If you try to do this on hot welds, they may break their continuity. So it's better to wait until they cool down.
Plastic Welding Mistakes to Avoid
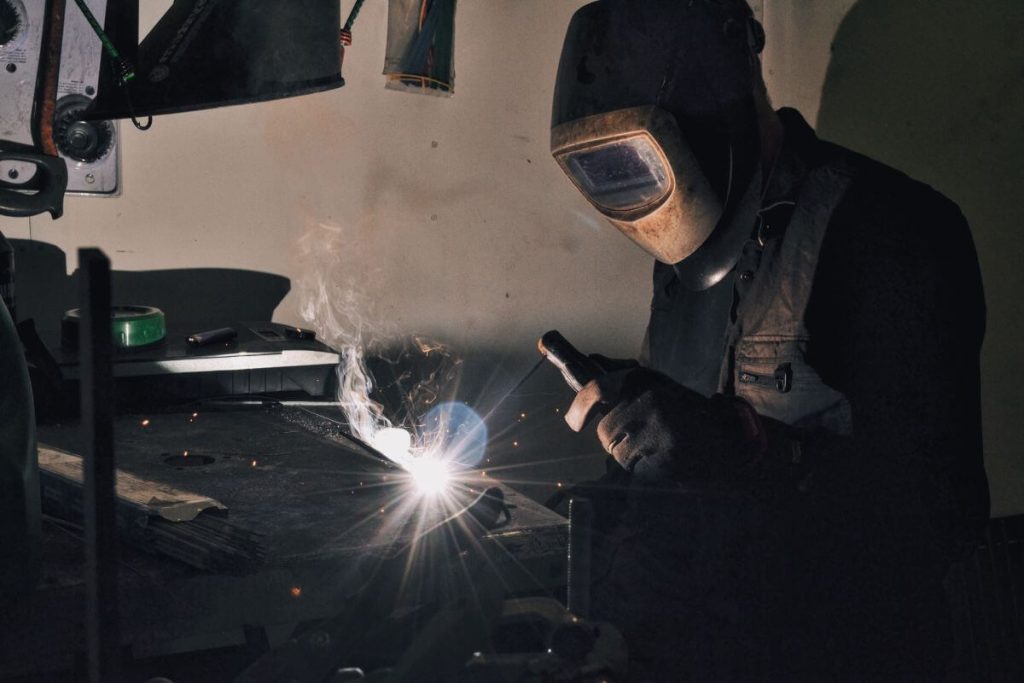
There are a few basic mistakes that even experienced welders make. They are here:
- poorly recognizable plastic;
- not thoroughly cleaned surface;
- wrong clamping force;
- heating only one of the elements.
Misdiagnosed Plastic
In this case, it will be difficult for you to set the correct temperature on the welding machine. And this can lead to too rapid melting of the elements and burnout of the weld. Welding plastic with an incorrectly identified material presents the risk of incorrect selection of the connecting element. And then all the work will be in vain, because the objects will not connect to each other.
Surface not thoroughly cleaned
Plastic adheres well to each other, but without the participation of solid impurities. Therefore, before starting work, try to clean and scrape the surface of the products to be welded well. Otherwise, even a perfectly matched temperature and binder will be useless. The weld will peel off in a few moments, and in the optimistic case this will happen in a few minutes.
Incorrect clamping force
This can happen especially at the beginning of plastic welding training. You will burn a lot of materials, before you feel, with what force to press them to the surface. If the pressure is too light, the elements will not connect to each other. Too much force can cause the welding tip to sink into the workpiece.
Heating only one of the elements
The quality of the connection also depends on how you heat the components. During the welding process, try to heat the filler metal and the material to be joined equally. If you do otherwise and heat only one of them, they will only slightly stick to each other. After a short time, you will easily be able to break these pieces without much effort.
Where is plastic welding most commonly used?
For the user of the vehicle, welding of this type of material is usually beneficial when bumpers are damaged. Of course, if the parts are scattered, it is impossible to reassemble them in such a way as to retain their current form and function. However, after an impact that will cause a long crack without serious damage, bumper welding makes sense. The same can be said about the brackets that fix the headlights and other items of car equipment, the replacement of which is very expensive.
The price of plastic welding - how much does it cost?
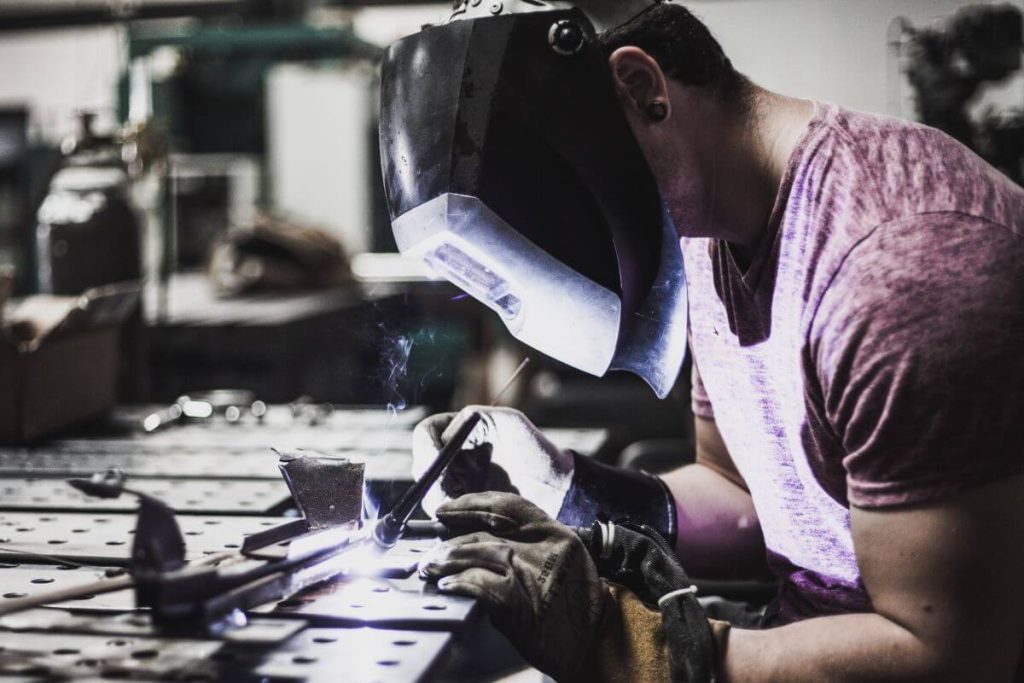
If you are not able to carry out such repairs yourself, welding a plastic bumper can cost you at least 20 euros. The older the car, the less profitable it is to carry out such repairs. The cost of replacement from popular scrap metal may not even exceed the price of welding, and remember that the price must include the painting of the element. In many cases, welding will be much cheaper than buying a new component. However, how it will be in your case, you must determine for yourself.
Plastic welder and joint strength
Welding is a common way to connect elements. In this way, household items are combined, as well as industrial machines and equipment. The durability of the weld will be satisfactory if you avoid the mistakes we mentioned when welding plastic at high temperature. You need a lot of practice in using the welding machine, choosing the temperature and using the accessories to make the effect permanent. The joining of plastics by welding is used, for example, in hydraulics, and combined pipes with high costs last for years.
If you want to weld the bumper yourself, it may not be worth buying all the parts. Another thing is if in the future you want to perform this type of service, at least occasionally. Then it makes sense to weld plastic elements on your own and buy equipment. If you do not have the tools, experience and time, it is better to take the damaged item to a specialized workshop.
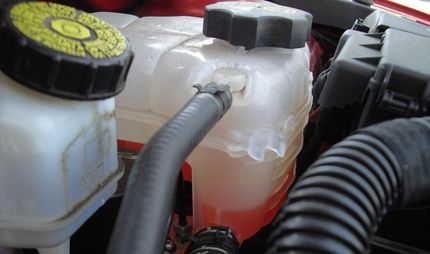
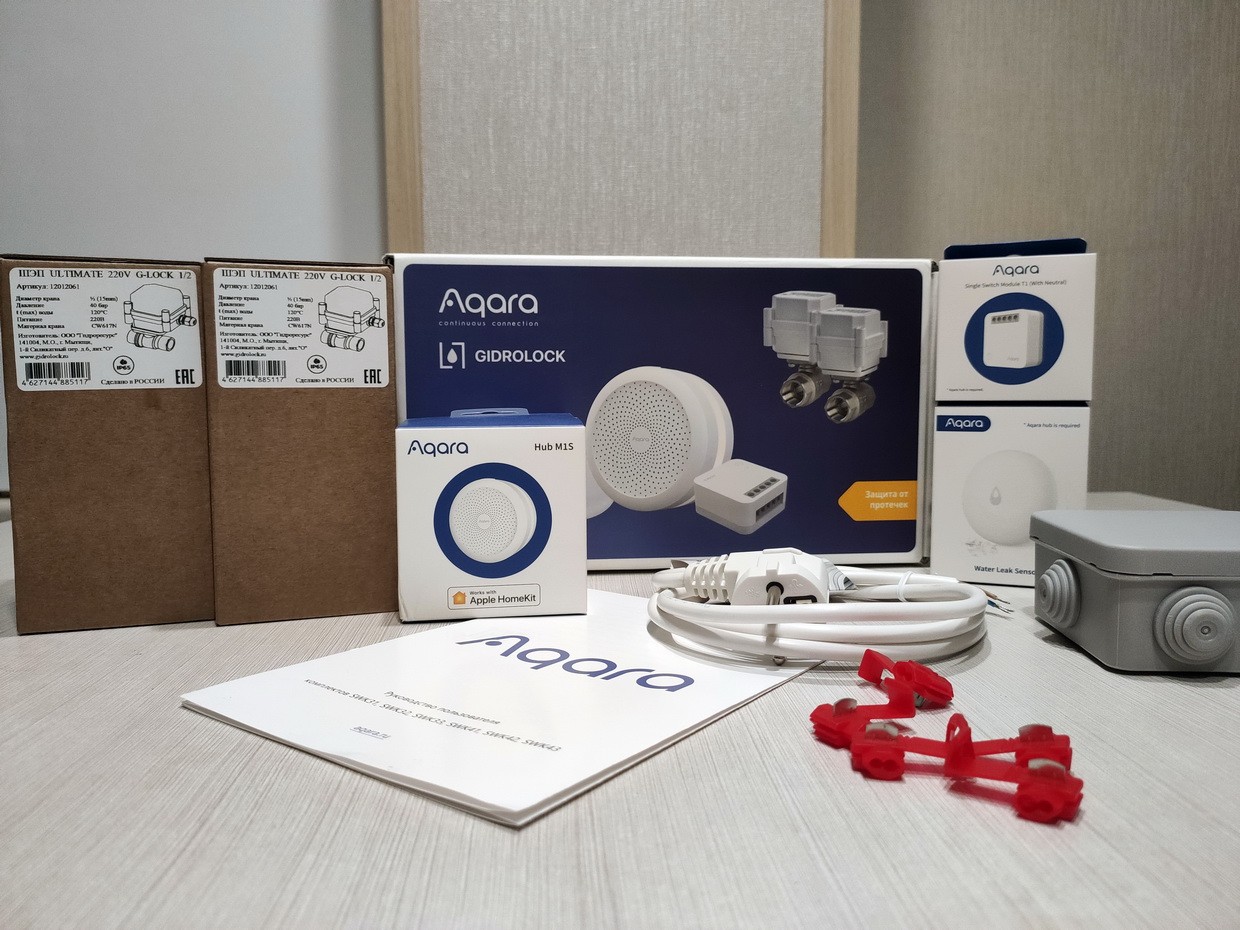