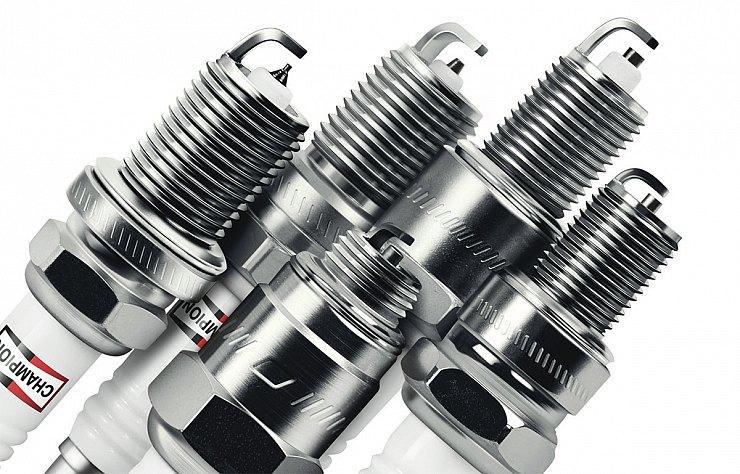
Spark plug: more than just a spark
The essence of the spark plug in a spark ignition engine seems obvious. This is a simple device in which the most important part is the two electrodes between which the ignition spark jumps. Few of us know that in modern engines, the spark plug has acquired a new function.
Modern engines are controlled almost exclusively electronically. Controller, popularly known as a "computer" collects a series of data on the operation of the unit (we mention here, first of all, the speed of the crankshaft, the degree of "pressing" on the gas pedal, atmospheric air pressure and in the intake manifold, the temperature of the coolant, fuel and air, and also the composition of the exhaust gases in the exhaust system before and after their cleaning by catalytic converters), and then, comparing this information with those stored in its memory, issues commands to the systems for controlling the ignition and fuel injection process, as well as the position of the air damper. The fact is that the flash point and the dose of fuel for the individual operating cycles must be optimal in terms of efficiency, economy and environmental friendliness at every moment of engine operation.
READ ALSO
Glow plugs
The game is worth the candle
Among the data necessary to control the correct operation of the engine, there is also information about the presence (or absence) of detonation combustion. The air-fuel mixture already in the combustion chamber above the piston must burn quickly but gradually, from the spark plug to the furthest reaches of the combustion chamber. If the mixture ignites in its entirety, i.e. "explodes", the efficiency of the engine (i.e., the ability to use the energy contained in the fuel) drops sharply, and at the same time, the load on important engine components increases, which can lead to failure. Therefore, a constant detonation phenomenon should not be allowed, but, on the other hand, the instant ignition setting and the composition of the fuel-air mixture should be such that the combustion process is relatively close to these detonations.
Therefore, for several years now, modern engines have been equipped with so-called. knock sensor. In the traditional version, this is actually a specialized microphone that, screwed into the engine block, responds only to vibrations with a frequency corresponding to a typical detonation combustion. The sensor sends information about possible knocking to the engine computer, which reacts by changing the ignition point so that knocking does not occur.
However, the detection of detonation combustion can be carried out in another way. Already in 1988, the Swedish company Saab launched the production of a distributorless ignition unit called Saab Direct Ignition (SDI) in the 9000 model. In this solution, each spark plug has its own ignition coil built into the cylinder head, and the “computer” feeds only control signals. Therefore, in this system, the ignition point can be different (optimal) for each cylinder.
However, more important in such a system is what each spark plug is used for when it is not producing an ignition spark (the duration of the spark is only tens of microseconds per operating cycle, and, for example, at 6000 rpm, one engine operation cycle is two hundredths seconds). It turned out that the same electrodes can be used to measure the ion current flowing between them. Here, the phenomenon of self-ionization of fuel and air molecules during the combustion of a charge above the piston was used. Separate ions (free electrons with a negative charge) and particles with a positive charge allow current to flow between the electrodes placed in the combustion chamber, and this current can be measured.
It is important to note that the degree of indicated gas ionization in the chamber combustion depends on combustion parameters, i.e. mainly on the current pressure and temperature. Thus, the value of the ion current contains important information about the combustion process.
The basic data obtained by the Saab SDI system provided information on knocking and possible misfires, and also allowed the required ignition timing to be determined. In practice, the system gave more reliable data than a conventional ignition system with a traditional knock sensor, and was also cheaper.
Currently, the so-called Distributionless system with individual coils for each cylinder is widely used, and many companies already use ion current measurement to collect information about the combustion process in the engine. Ignition systems adapted to this are offered by the most important engine suppliers. It also turns out that evaluating the combustion process in an engine by measuring the ion current can be an important way to study engine performance in real time. It allows you to directly detect not only improper combustion, but also determine the size and position (calculated in degrees of rotation of the crankshaft) of the actual maximum pressure above the piston. Until now, such a measurement was not possible in serial engines. Using the appropriate software, thanks to this data, it is possible to accurately control the ignition and injection in a much wider range of engine loads and temperatures, as well as adjust the unit's operating parameters to specific fuel properties.
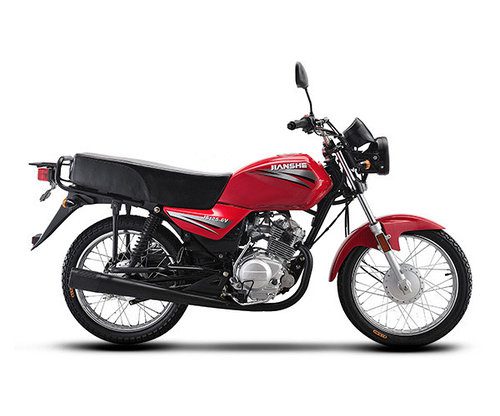
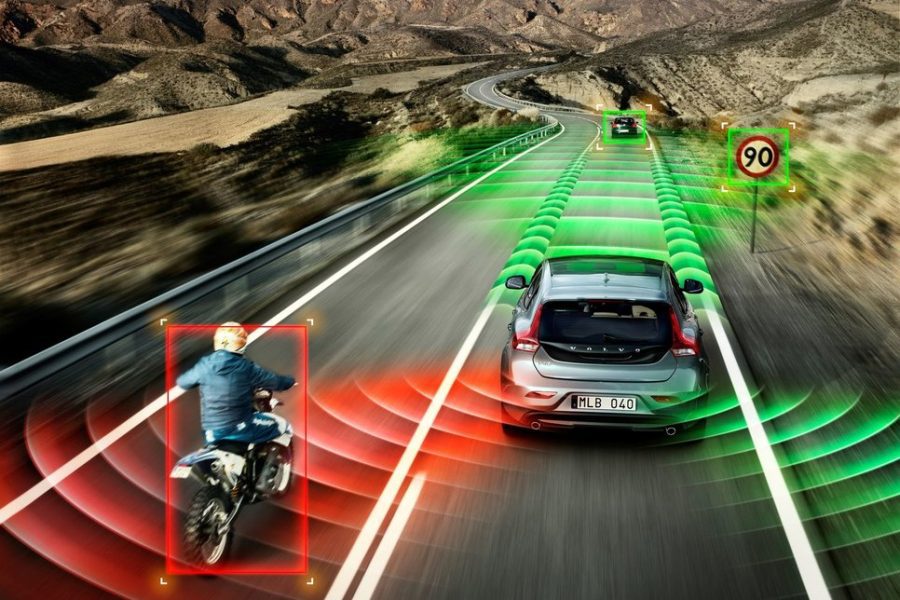