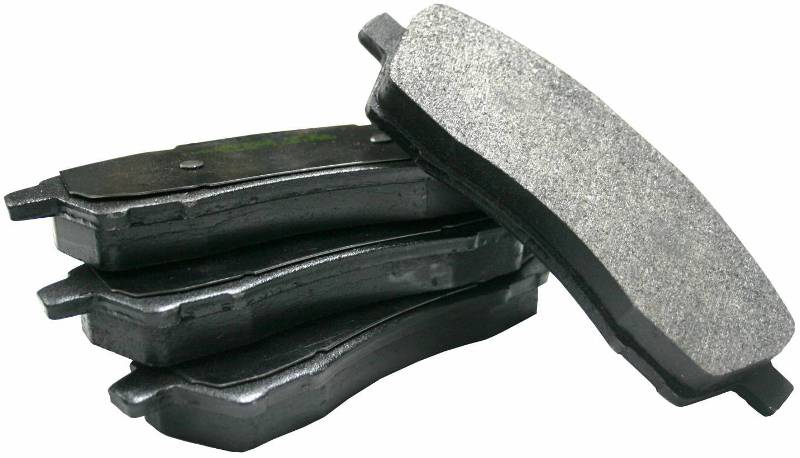
Brake pad test - how is their performance determined?
Content
The safety of the driver and passengers depends on the serviceability and reliability of many vehicle systems and, first of all, on the brake system. One of the factors determining the effectiveness of its work is the quality of the brake pads.
Content
- 1 Important aspects for selecting brake pads
- 2 Selection of pads according to performance characteristics
- 3 How to test drive pads
- 4 Test results for pads from various manufacturers
- 5 Results of laboratory testing
Important aspects for selecting brake pads
The quality of brake pads is determined primarily by which manufacturer produces them. Therefore, before purchasing them (regardless of which cars - domestic or foreign cars), you need to pay attention to the following general aspects of the choice.
The originality of the product is the first of them. This is a very important point. It's no secret that the auto parts market is literally filled with a lot of fakes. In addition, there is a certain difference between the products of the same manufacturer: the market offers original spare parts produced for the assembly line on which cars are assembled, and at the same time there are original spare parts produced directly for sale in the wholesale and retail network.
It does not make sense to consider pads intended for the conveyor, since they are quite expensive and quite rare on the market - the component of their quantity in the total volume of this product, as a rule, does not exceed 10%. Original products for sale can be found much more often, and their cost is 30-70% of the conveyor price. There are also pads that are significantly inferior in quality to the original ones, but are produced at the same factory along with them. These products are targeted at a wide range of different consumers, including those from developing countries. The price of these pads is 20-30% of the cost of the original.
Selection of pads according to performance characteristics
The next general aspect of pad selection is performance. For the practical application of these spare parts on a car, this moment is the most important. At the same time, this is a very individual aspect, since drivers are still different and, accordingly, their driving style is different. Therefore, in this case, it is no longer important who drives which car, the main thing is how he does it. That is why pad manufacturers, as a rule, at the presentations of their new product or in the descriptions for it, give appropriate recommendations regarding the selection of one or another of its models. There are pads that are recommended for:
- drivers whose main driving style is sporty;
- frequent use of the car in mountainous areas;
- moderate operation of the machine in the city.
Before making such recommendations, manufacturers conduct testing, on the basis of which a conclusion is made about the performance of the pads.
To understand what kind of product is offered for sale, you need to pay close attention to its packaging. In resolving this issue, you should rely on your own keen eye or select a spare part together with a specialist (master) involved in the maintenance of the car on which you need to put brake pads. When choosing them, you need to pay attention to the country and year of manufacture, the badges confirming the certification of the product, the design of the package, the inscriptions on it (even lines, correct spelling, clear and legible printing), as well as the integrity of the brake pad itself (no cracks, bulges). , chips, snug fit of the lining of the friction material to the metal base).
How to test drive pads
To conduct a comparative test, each set of run-in brake pads is subjected to 4 tests on special stands. First, the braking of a car accelerated to 100 km/h is simulated. This test is basic. It helps to determine the coefficient of friction of a disc-pad pair for cold brakes (up to 50 ° C). The higher the coefficient obtained, the higher the frictional parameters of the block, respectively.
But the brakes, in case of intensive use, can sometimes heat up to 300 ° C or more. This is especially true for very active drivers, often and intensively braking from high speed. To check whether the pads can withstand this mode of operation, a “hot” test is performed after the “cold” test. The disc and pads are heated by continuous braking to a temperature of 250 ° C (the degree of heating is controlled using a thermocouple, which is implanted directly into the friction material of one of the pads). Then make control braking from the same speed of 100 km / h.
The third test is even tougher. During it, repeated-cyclic braking is simulated in conditions of movement on a mountain road. This test includes 50 decelerations from 100 km/h to 50 km/h with 45 second breaks to spin up the test stand flywheel. The result of the 50th (last) braking is of the greatest interest - despite some cooling of the pads during the spin-up of the flywheel, by the 50th braking cycle, the material temperature of many of them is 300 °C.
The last test is also called the recovery test - it is checked how “warmed up” brake pads are able to maintain performance after cooling. To find out, after the "mountain" test, the brakes are cooled to the ambient (test) temperature, and in a natural way (not forcibly). Then control braking is again carried out after acceleration to 100 km/h.
According to the results of the tests for each individual set of pads, 4 values of the friction coefficient are obtained - one for each test. In addition, at the end of each individual test cycle, the thickness of the lining of the friction material is measured - thereby collecting information on wear.


Watch this video on YouTube
Test results for pads from various manufacturers
There are a lot of manufacturers of car pads, and the price range for various products is quite large, so it is rather difficult to determine which of them will be the best without trying them in practice or testing them. Below are the results of testing conducted by the test shop of the domestic car manufacturer AvtoVAZ with the participation of the Center for Independent Expertise and the Autoreview magazine. It should be noted that for pads installed on VAZ vehicles, technical specifications TU 38.114297-87 are applied, according to which the lower limit of the friction coefficient at the stage of "cold" testing is 0,33, and at "hot" - 0,3. At the end of the tests, the wear of the pads was calculated as a percentage.
As samples with which the testing was carried out, pads from different manufacturers (including Russian ones) and different price groups were taken. Some of them were tested not only with a native disk, but also with a VAZ one. Products from the following manufacturers have been tested:
- Credits: DAfmi, Trans Master;
- Germany: ATE, Bosch;
- UK: Ferodo, AP Lockheed, Lucas, QH;
- Denmark: Roulunds;
- Italy: Samko;
- Hungary: Rona;
- Russia: VATI, EZATI, Polyhedron, TIIR, STS;
- unknown: Best.
The samples were purchased from a retail network and the data on their manufacturers are taken exclusively from the packages.
The brake pad test revealed the following. The best cold test scores came from QH, Samko, ATE, Roulunds and Lucas. Their results were respectively: 0,63; 0,60; 0,58; 0,55 and 0,53. Moreover, for ATE and QH, the highest value of the friction coefficient was achieved not with native, but with VAZ disks.
The results of testing for "hot braking" were quite unexpected. During this test, Roulunds (0,44) and ATE (0,47) performed well. Hungarian Rona, as in the previous test, gave a coefficient of 0,45.
According to the results of the "mountain cycle", the Rona pads (0,44) turned out to be the best, continuing to maintain a position of stability, and, which is also important, heated up to a relatively low temperature of only 230 ° C. QH products have a friction coefficient of 0,43, and this time with their own, native discs.
During the final test Italian pads Samko (0,60) showed themselves well again in the “cooled braking”, cooled down and climbed up the indicators of the Rona pad (0,52), the best product was QH (0,65).
Results of laboratory testing
According to the final pad wear, the most wear-resistant products were Bosch (1,7%) and Trans Master (1,5%). Strange as it may seem, the leaders of the conducted testing were ATE (2,7% with a VAZ disk and 5,7% with a native one) and QH (2,9% with a native one, but 4,0 % - with VAZ).
According to laboratory tests, the best pads can be called the products of the ATE and QH brands, which fully comply with the main selection criterion - quality-price ratio. At the same time, one cannot ignore the fact that ATE pads were better used with a VAZ disk, and QH - with a native disk. Best, Trans Master, Rona, Roulunds and STS declared stable good quality. Good overall results were given by EZATI, VATI, to some extent - DAfmi and Lucas. The Polyhedron and AP Lockheed brand pads were simply disappointing.


Watch this video on YouTube
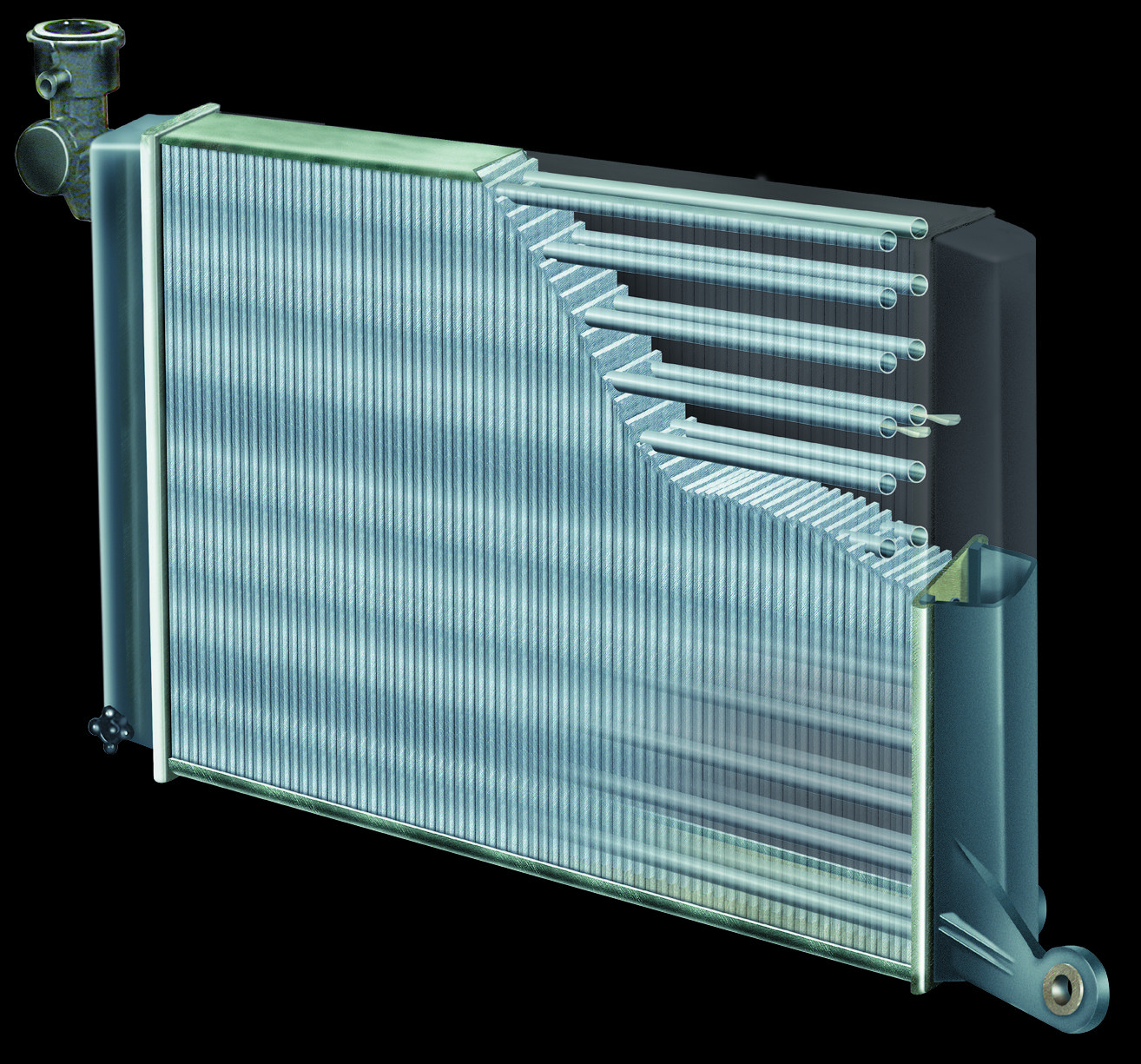
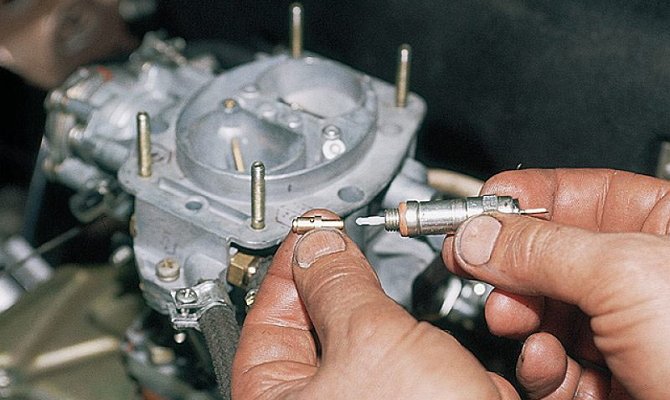