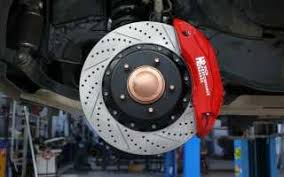
Types, device and principle of operation of disc brakes
Content
Hydraulic disc brakes are one of the types of friction type brakes. Their rotating part is represented by a brake disc, and the stationary part is represented by a caliper with brake pads. Despite the widespread use of drum brakes, disc brakes are still the most popular. We will understand the device of a disc brake, as well as find out the differences between the two brakes.
Disc brakes device
The disc brake design is as follows:
- support (bracket);
- service brake cylinder;
- brake pads;
- brake disk.
The caliper, which is a cast iron or aluminum body (in the form of a bracket), is attached to the steering knuckle. The design of the caliper allows it to move along the guides in the horizontal plane relative to the brake disc (in the case of a floating caliper mechanism). The caliper housing contains pistons, which, when braking, press the brake pads against the disc.
The working brake cylinder is made directly in the caliper housing, inside it there is a piston with a sealing lip. To remove accumulated air when bleeding the brakes, a fitting is installed on the body.
Brake pads, which are metal plates with fixed friction linings, are installed in the caliper housing on both sides of the brake disc.
The rotating brake disc is mounted on the wheel hub. The brake disc is bolted to the hub.
Types of disc brakes
Disc brakes are divided into two large groups according to the type of caliper (caliper) used:
- mechanisms with a fixed bracket;
- mechanisms with a floating bracket.
In the first version, the bracket has the ability to move along the guides and has one piston. In the second case, the caliper is fixed and contains two pistons mounted on opposite sides of the brake disc. Brakes with a fixed caliper are capable of creating a greater force of pressing the pads against the disc and, accordingly, a greater braking force. However, their cost is higher than that of floating caliper brakes. Therefore, these brakes are mainly used on powerful cars (using several pairs of pistons).
How disc brakes work
Disc brakes, like any other brake, are designed to change the speed of the vehicle.
Step-by-step operation of disc brakes:
- When the driver presses the brake pedal, the GTZ creates pressure in the brake pipes.
- For a mechanism with a fixed shackle: fluid pressure acts on the pistons of the working brake cylinders with both sides of the brake disc, which in turn press the pads against it. For the floating bracket mechanism: fluid pressure acts on the piston and caliper body at the same time, forcing the latter to move and press the pad against the disc from the other side.
- A disc sandwiched between two pads reduces speed due to frictional force. And this, in turn, leads to braking of the car.
- After the driver releases the brake pedal, the pressure is lost. The piston returns to its original position due to the elastic properties of the sealing collar, and the pads are retracted using a slight vibration of the disc during movement.
Types of brake discs
According to the material of manufacture, brake discs are divided into:
- Cast iron;
- Stainless steel discs;
- Carbon;
- Ceramic.
Most often, brake discs are made of cast iron, which has good frictional properties and low production costs. The wear of the cast iron brake discs is not great. On the other hand, with regular intensive braking, which causes an increase in temperature, the cast-iron disc may buckle, and if water gets on it, it may become cracked. In addition, cast iron is a rather heavy material, and after a long stay it can become rusty.
Known discs and stainless steel, which is not so sensitive to temperature changes, but has weaker frictional properties than cast iron.
Carbon discs are lighter than cast iron discs. They also have a higher coefficient of friction and working range. However, in terms of their cost, such wheels can compete with the cost of a small car. Yes, and for normal operation, they need to be preheated.
Ceramic brakes cannot match carbon fiber in terms of coefficient of friction, but they have a number of their advantages:
- high temperature resistance;
- resistance to wear and corrosion;
- high strength;
- small specific gravity;
- durability.
Ceramics also have their disadvantages:
- poor performance of ceramics at low temperatures;
- creak during work;
- high price.
Brake discs can also be subdivided into:
- Ventilated;
- Perforated.
The first ones consist of two plates with cavities between them. This is done for better heat dissipation from disks, the average operating temperature of which is 200-300 degrees. The latter have perforations / notches along the surface of the disc. Perforations or notches are designed to drain brake pad wear products and maintain a constant coefficient of friction.
Types of brake pads
Brake pads, depending on the material of the friction linings, are divided into the following types:
- asbestos;
- asbestos-free;
- organic.
The first ones are very harmful to the body, therefore, in order to change such pads, all safety measures must be observed.
In asbestos-free pads, steel wool, copper shavings and other elements can play the role of a reinforcing component. The cost and quality of the pads will depend on their constituent elements.
Pads made from organic fibers have the best braking properties, but their cost will be high.
Service of brake discs and pads
Disc wear and replacement
Brake disc wear is directly related to the driving style of the motorist. The degree of wear is determined not only by the mileage, but also by driving on bad roads. Also, the quality of the brake discs affects the degree of wear.
The minimum permissible brake disc thickness depends on the make and model of the vehicle.
The average value of the minimum permissible disc thickness for the front brakes is 22-25 mm, for the rear ones - 7-10 mm. It depends on the weight and power of the vehicle.
The main factors indicating that the front or rear brake discs need to be replaced are:
- runout of discs during braking;
- mechanical damage;
- increase in stopping distance;
- lowering the level of the working fluid.
Wear and replacement of pads
Brake pad wear primarily depends on the quality of the friction material. Driving style also plays an important role. The more intensive the braking is, the stronger the wear.
The front pads wear out faster than the rear ones due to the fact that when braking they are experiencing the main load. When replacing pads, it is better to change them at the same time on both wheels, be it rear or front.
Pads installed on one axle can also wear out unevenly. It depends on the serviceability of the working cylinders. If the latter are faulty, then they compress the pads unevenly. A difference in the thickness of the pads of 1,5-2 mm may indicate uneven wear of the pads.
There are several ways to determine if the brake pads need to be replaced:
- Visual based on checking the thickness of the friction lining. Wear is indicated by a lining thickness of 2-3 mm.
- Mechanical, in which the pads are equipped with special metal plates. The latter, as the linings wear out, begin to come into contact with the brake discs, which is why the disc brakes creak. The reason for the squeak of the brakes is the abrasion of the lining up to 2-2,5 mm.
- Electronic, which uses pads with a wear sensor. As soon as the friction lining is erased to the sensor, its core contacts the brake disc, the electrical circuit closes and the indicator on the dashboard lights up.
Pros and cons of disc brakes versus drum brakes
Disc brakes have a number of advantages over drum brakes. Their advantages are as follows:
- stable operation with water ingress and pollution;
- stable operation when the temperature rises;
- effective cooling;
- small size and weight;
- ease of maintenance.
The main disadvantages of disc brakes in comparison with drum brakes include:
- high price;
- less braking efficiency.
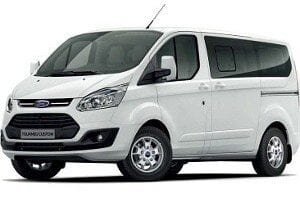
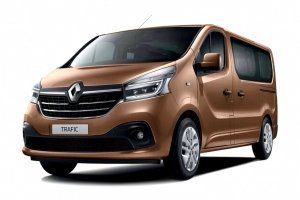