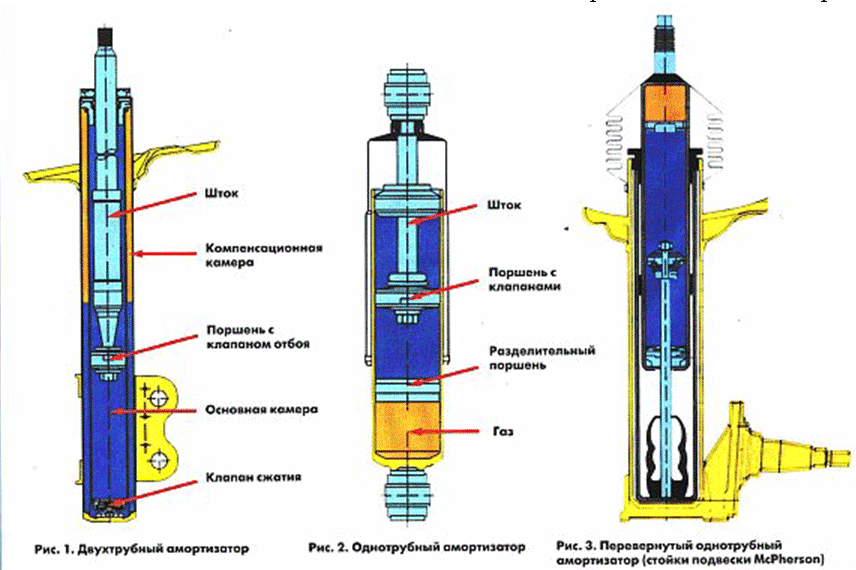
Shock absorbers in the suspension of a car - design and principle of operation
Content
Shock absorber history
The bodies of the first "self-propelled carriages" were made in carriage workshops, and the springs, indispensable parts of a comfortable horse-drawn carriage, migrated to a new mode of transport.
Interleaf friction, pronounced in flat multi-leaf springs, prevents resonant vibrations of the body, and with a sufficiently slow movement, this effect was quite enough for ease of control and passenger comfort.
As vehicle speeds increased, it became necessary to compensate for the rapid response of the elastic elements of the undercarriage, reduce shock loads during the reverse motion of the wheels and ensure their constant connection with the road.

The simplest solution was to add crank arms with friction discs in the hinges to the design of the undercarriage.
Friction damping devices served until the 50s of the last century. Rapid wear and difficulty in restoring the friction parts of friction dampers, their large dimensions, the difficulty of combining with the springs that appeared instead of the springs - all this forced designers and manufacturers to look for other methods of damping in mass-produced cars.
By this time, almost all sports and racing cars were already using hydraulic shock absorbers, which had migrated there from the design of aircraft landing gear.
Purpose of shock absorbers
Together with springs, springs or other elastic elements, the damping device solves important problems:
- Slows down and stretches in time sharp deformations of elastic elements.
- Absorbs part of the vertical loads transmitted to the frame (body) of the machine.
- Prevents the appearance of resonant vibrations.
- Maintains constant contact of the wheels with the road.
The smoothness of the movement of the car and its controllability on difficult sections of roads directly depend on the serviceability of the shock absorbers.
Principle of operation and design
The vertical forces arising in the suspension are transmitted through the rod to the piston moving longitudinally in the cylinder filled with the working medium. The piston acts on the working medium and forces it to decrease in volume. After the load is removed, the elastic elements of the suspension return to their previous position, dragging the rod with the piston, and the working medium assumes its previous volume.

The shock absorber housing is closed by a cylindrical casing fixed on the rod and serving to protect against dirt and mechanical damage.
In the chassis of the car, the shock absorber is connected by a rod to the frame (body) of the car, the lower part is fixed on the suspension arm or on the bridge. Rubber-metal hinges are installed at the attachment points.
Acting as a damper, the shock absorber simultaneously serves as a suspension travel limiter, so a rebound buffer is installed on the rod.
According to the type of working fluid (medium), all structures can be divided into:
- Hydraulic (oil);
- Gas (gas-filled);
- Gas-hydraulic (gas-oil).
Hydraulic (oil)
Under compressive loads on the rod, oil flows from the cavity under the piston into the rod cavity through calibrated holes equipped with forward and reverse bypass valves. Valves slow down the rate of change in the volume of the liquid and, accordingly, the speed of the piston.

A significant part of the compressive and tensile loads is spent on pumping oil, the piston movement speed is limited by the viscosity of the working medium.
Gas (gas-filled)
They differ from oil ones in that after the piston cavity filled with oil in the working cylinder there is a chamber with compressed gas (nitrogen), separated from the oil by a floating piston. The nitrogen pressure reaches 30 MPa.

Longitudinal forces acting on the rod are transferred by oil to the floating piston, which changes the volume of the gas chamber.
Gas-hydraulic (gas-oil)
The volume free from oil is filled with nitrogen under pressure from 2 to 8 MPa. During the compression stroke, the piston displaces oil through the valves, compressing nitrogen. During the rebound stroke, the oil is returned to the piston cavity by nitrogen pressure.

According to the internal structure, they distinguish
- Two-pipe.
- Single-pipe.
It would be more correct to call one- and two-cylinder, but this terminology is used to avoid double meaning in the descriptions of the designs of damping devices and internal combustion engines.
Two-pipe
The housing consists of two coaxial cylinders - an internal working one, in which the rod and piston are located, and an external one, called a reservoir.
The oil displaced during the compression stroke is pumped into the rod end of the working cylinder and simultaneously forced into the reservoir cylinder.
All oil and gas-oil shock absorbers are of a two-tube design.
Single pipe
All single-tube shock absorbers are gas-filled. In the common housing, which is also a working cylinder, there is a piston rod, oil and gas chambers, separated by a floating piston.
The most massive type of shock absorber today.

Advantages and disadvantages
Two-pipe:
- simplicity of design and low cost;
- small length;
- low internal pressure and small oil leaks.
- soft damping of loads;
- resistance to mechanical damage.
According to the laws of thermodynamics, all liquids, flowing at high speed through small holes, heat up and lose their viscosity. Oil, moreover, is capable of foaming when heated.
The loss of working properties as a result of a decrease in the viscosity of the oil and its transformation into gas-oil foam after a long drive is the main drawback of two-pipe designs.
Single pipe:
- good damping and stability characteristics;
- longer service life;
- improved cooling;
- Possibility to install upside down.
Gas-filled single-pipe devices are more resistant to temperature rise and foaming of the working fluid and withstand continuous loads without damage.
Disadvantages:
- large dimensions in length;
- low resistance to hull damage;
- significant cost.
Adjustable (adaptive) devices
With manual adjustments.
Equipped with additional valves and a set of bypass pipes. Allows you to adjust the characteristics of the device depending on the position of the piston.
with controlled valves.
Devices with adjustment of damping properties and compression-rebound forces by changing the cross section of forward and reverse valves.

Two-pipe, the working cylinder communicates with the tank through electromagnetic valves controlled by an electronic unit.
The hydraulic resistance to the flow of liquid and, accordingly, the rigidity of the device depends on the magnitude of the opening and closing of the valves.
With magnetorheological fluid.
The working cylinder is filled with a suspension of oil and the finest magnetic powder. The viscosity of the suspension changes in a fraction of a second and depends on the strength of the magnetic field created by the annular electromagnets built into the piston.
The advantages of adaptive devices are the ability to change the properties of the suspension in accordance with driving conditions.
The main disadvantage: high cost.
Sports
Designed to work with high loads. The working fluid is temperature stable and does not lose viscosity when heated. To maintain constant grip, the wheels have increased compression force and a short rebound time, which ensures constant grip of the wheels with the road and good cornering control.

Service life and malfunctions
The "survivability" of shock absorbers, under average operating conditions, is about 100-125 thousand kilometers. The front shock absorbers last less than the rear ones.
It is difficult to single out signs of malfunctions of damping devices from a complex of other flaws in a worn-out undercarriage. The devices themselves are quite reliable, with a slow appearance and increase of defects, so the owner may not notice the deterioration of their work for a long time.
Wear and destruction of elastic bushings (liners) and silent blocks in attachment points is the most common problem on our roads. Corrected by the usual replacement of parts.
Sudden failure is a rather rare phenomenon, most often it is a break in the fastening lugs of the outer case.
Hidden problems - wear of seals, leakage of liquids and gases - are difficult to find in general vehicle diagnostics. It is necessary to dismantle the "suspicious" node and check its performance for compression and rebound.
In oil and gas-oil structures, leaks and wear of seals are detected by oil smudges on the outer surface and the appearance of free play of the rod when it is moved to its extreme positions.
In the era of the mass use of oil shock absorbers, their repair consisted in replacing cuffs, springs and piston valves and updating the working fluid.
Repair and restoration of modern gas, gas-oil, adjustable and adaptive structures is almost impossible. In case of failure, they are replaced as an assembly.
After repair (replacement) of the front suspension units, it is necessary to check and adjust the camber, toe-in and other wheel alignment angles.
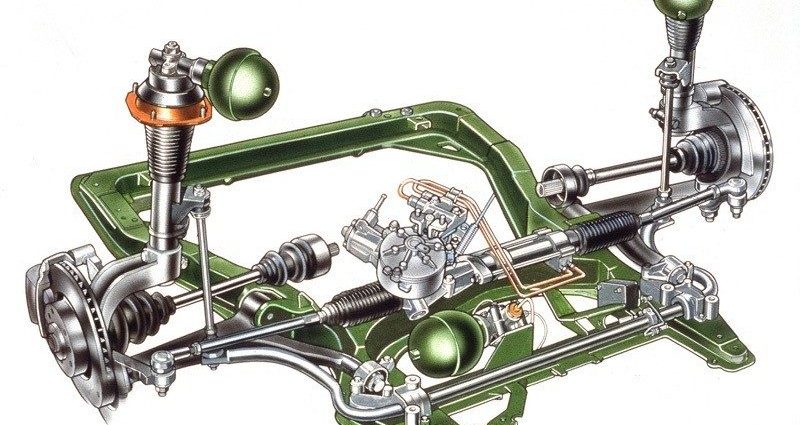
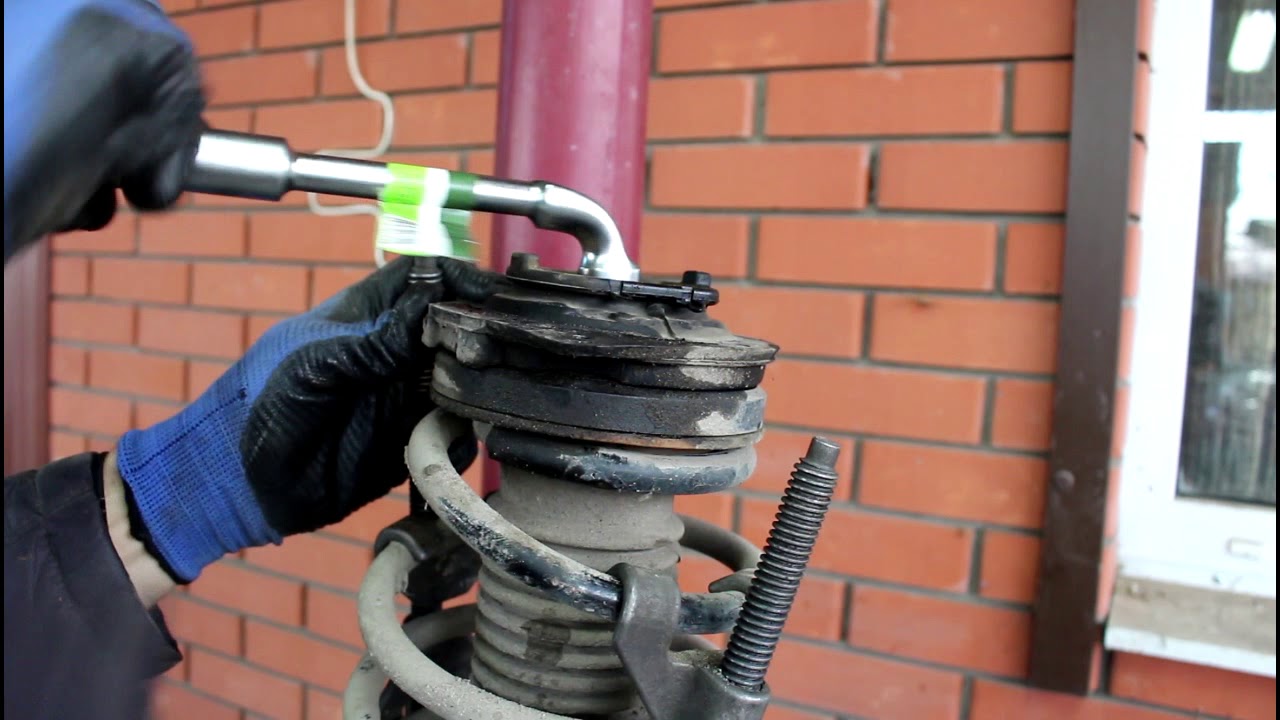