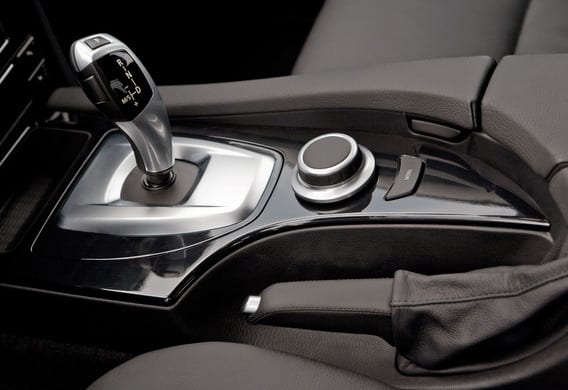
Manual transmission - robotic gearbox
Content
Any modern car cannot start and move smoothly if there is no transmission in its device. Today, there is a wide variety of all kinds of gearboxes, which not only allow the driver to choose an option that suits his material capabilities, but also make it possible to get maximum comfort from driving.
Briefly about the main types of transmission is described in separate review... Now let's talk in more detail about what a robotic gearbox is, its main differences from a manual gearbox, and also consider the principle of operation of this unit.
What is a robotic gearbox
The operation of the gearbox is almost identical to the mechanical analogue with the exception of some features. The robot's device includes many parts that make up the mechanical version of the box already familiar to everyone. The main difference between the robotic one is that its control is of a microprocessor type. In such gearboxes, gear shifting is performed by electronics based on data from sensors of the engine, gas pedal and wheels.

A robotic box can also be called an automatic machine, but this is an incorrect name. The fact is that automatic transmission is often used as a generalizing concept. So, the same variator has an automatic mode for switching gear ratios, so for some it is also an automatic. In fact, in terms of structure and principle of operation, the robot is closer to a mechanical box.
Outwardly, it is impossible to distinguish between automatic transmission and manual transmission, because they may have an identical selector and body. You can check the transmission only while the vehicle is driving. Each type of unit has its own characteristics of work.
The main purpose of a robotic transmission is to make driving as easy as possible. The driver does not need to switch gears on his own - this work is done by the control unit. In addition to comfort, automatic transmission manufacturers are striving to make their products cheaper. Today, the robot is the most budgetary type of gearbox after mechanics, but it does not provide such driving comfort as a variator or automatic.
The principle of a robotic gearbox
The robotic transmission can switch to the next speed either automatically or semi-automatically. In the first case, the microprocessor unit receives signals from the sensors, on the basis of which the algorithm programmed by the manufacturer is triggered.
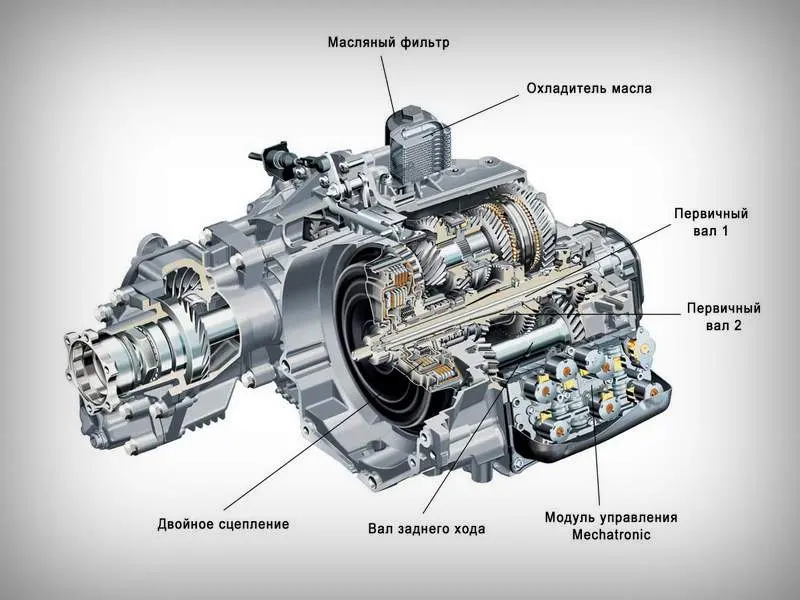
Most gearboxes are equipped with a manual selector. In this case, the speeds will still turn on automatically. The only thing is that the driver can independently signal the moment of switching on an up or down gear. Some automatic transmissions of the Tiptronic type have a similar principle.
To increase or decrease the speed, the driver moves the selector lever towards + or towards -. Thanks to this option, some people call this transmission sequential or sequential.
The robotic box works according to the following scheme:
- The driver applies the brake, starts the engine and moves the driving mode switch to position D;
- The signal from the unit goes to the box control unit;
- Depending on the selected mode, the control unit activates the appropriate algorithm according to which the unit will operate;
- In the process of movement, the sensors send signals to the "brain of the robot" about the speed of the vehicle, about the load of the power unit, as well as about the current gearbox mode;
- As soon as the indicators cease to correspond to the program installed from the factory, the control unit gives the command to change to another gear. This can be either an increase or a decrease in speed.
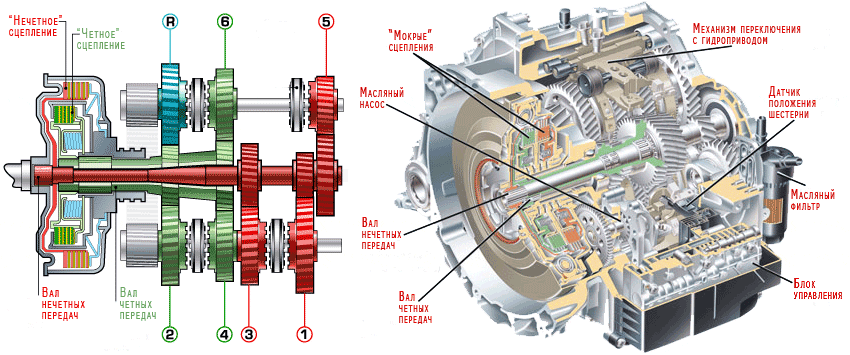
When a driver is driving a car with mechanics, he must feel his vehicle in order to determine the moment when to switch to another speed. In a robotic analogue, a similar process takes place, only the driver does not need to think about when to move the shift lever to the desired position. Instead, the microprocessor does it.
The system monitors all information from all sensors and selects the optimal gear for a specific load. So that the electronics can change gears, the transmission has a hydromechanical actuator. In a more common version, instead of hydromechanics, an electric drive or a servo drive is installed, which connects / disconnects the clutch in the box (by the way, this has some similarity with the automatic gearbox - the clutch is located not where it is in the manual transmission, namely near the flywheel, but in the housing itself transmission).
When the control unit gives a signal that it is time to switch to another speed, the first electric (or hydromechanical) servo drive is activated first. It disengages the clutch friction surfaces. The second servo then moves the gears in the mechanism to the desired position. Then the first one slowly releases the clutch. This design allows the mechanism to work without the participation of the driver, therefore, a machine with a robotic transmission does not have a clutch pedal.
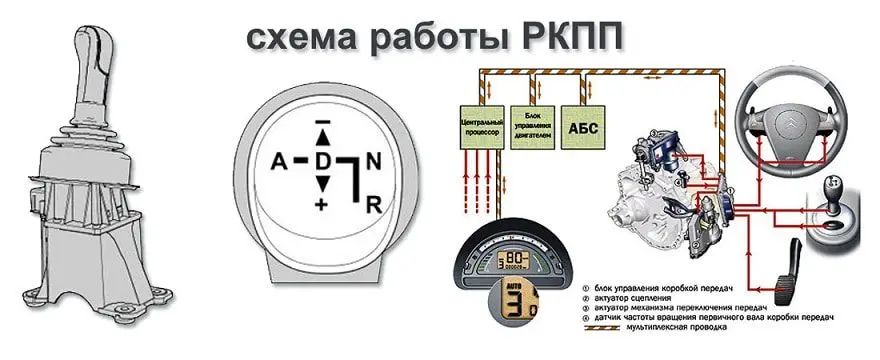
Many selector boxes have forced gear positions. This so-called tiptronic allows the driver to independently control the moment of switching to a higher or lower speed.
Robotic gearbox device
Today, there are several types of robotic transmissions for passenger cars. They may differ from each other in some actuators, but the main parts remain identical.
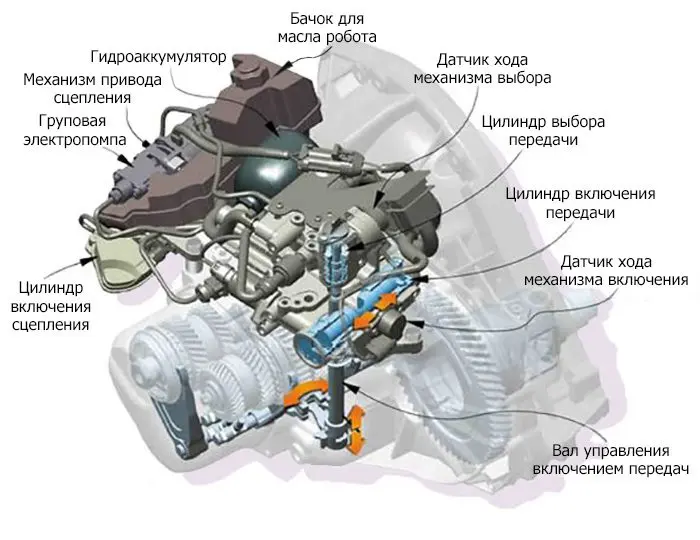
Here are the nodes included in the gearbox:
- Clutch. Depending on the manufacturer and the modification of the unit, this can be one part with a friction surface or several similar discs. Most often, these elements are located in the coolant, which stabilizes the operation of the unit, preventing it from overheating. The preselective or double option is considered more effective. In this modification, while one gear is engaged, the second set is preparing to turn on the next speed.
- The main part is a conventional mechanical box. Each manufacturer uses different proprietary designs. For example, a robot from the Mercedes brand (Speedshift) is internally a 7G-Tronic automatic transmission. The only difference between the units is that instead of a torque converter, a clutch with several friction discs is used. BMW has a similar approach. Its SMG gearbox is based on a six-speed manual gearbox.
- Clutch and transmission drive. There are two options - with an electric drive or a hydromechanical analogue. In the first case, the clutch is squeezed out by an electric motor, and in the second - by hydraulic cylinders with EM valves. The electric drive works slower than the hydraulics, but it does not require the maintenance of constant pressure in the line, from which the electro-hydraulic type operates. The hydraulic robot moves to the next stage much faster (0,05 seconds versus 0,5 seconds for the electric analogue). An electric gearbox is mainly installed on budget cars, and a hydromechanical gearbox is installed on premium sports cars, since gearshift speed is extremely important in them without interrupting the power supply to the drive shaft.
- Sensor. There are a lot of such parts in the robot. They monitor many different parameters of the transmission, for example, the position of the forks, the revolutions of the input and output shafts, in which position the selector switch is locked, the temperature of the coolant, etc. All this information is fed to the mechanism control device.
- ECU is a microprocessor unit, into which different algorithms are programmed with different indicators coming from sensors. This unit is connected to the main control unit (from there data on engine operation comes), as well as to electronic wheel locking systems (ABS or ESP).
- Actuators - hydraulic cylinders or electric motors, depending on the modification of the box.
The specifics of the work of the RKPP
In order for the vehicle to start smoothly, the driver must use the clutch pedal correctly. After he has included the first or reverse gear, he needs to smoothly release the pedal. Once the driver has a feel for the engagement of the discs, as he releases the pedal, he can add RPM to the engine to keep the car from stalling. This is how mechanics work.
An identical process occurs in the robotic counterpart. Only in this case a great skill is not required from the driver. He only needs to move the box switch to the appropriate position. The car will start to move in accordance with the settings of the control unit.
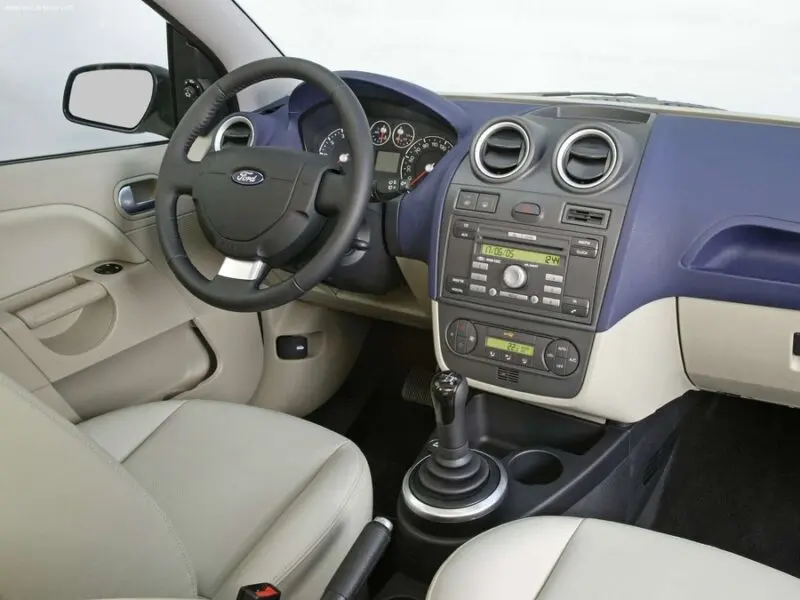
The simplest single-clutch modification works just like classic mechanics. However, at the same time, the presence of one problem is observed - the electronics do not record the feedback from the clutch. If a person is able to determine how smoothly it is necessary to release the pedal in a particular case, then the automation works more rigidly, so the movement of the car is accompanied by tangible jerks.
This is especially felt in modifications with an electric drive of the actuators - while the gear is shifting, the clutch will be in an open state. This will mean a break in the flow of torque, due to which the car begins to slow down. Since the speed of rotation of the wheels is already less consistent with the engaged gear, a slight jerk occurs.
An innovative solution to this problem was the development of a double-clutch modification. A striking representative of such a transmission is the Volkswagen DSG. Let's take a closer look at its features.
Features of the DSG robotic gearbox
The abbreviation stands for direct shift gearbox. In fact, these are two mechanical boxes installed in one housing, but with one connection point to the chassis of the machine. Each mechanism has its own clutch.
The main feature of this modification is the preselective mode. That is, while the first shaft is running with the gear engaged, the electronics already connects the corresponding gears (when accelerating to increase the gear, when decelerating - to lower) of the second shaft. The main actuator only needs to disconnect one clutch and connect another. As soon as a signal is received from the control unit to switch to another stage, the working clutch is opened, and the second one with gears already meshed is immediately connected.
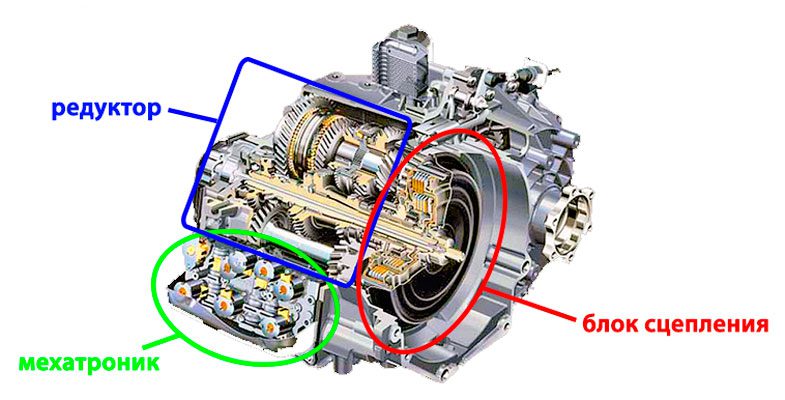
This design allows you to ride without strong jerks when accelerating. The first development of a preselective modification appeared in the 80s of the last century. True, then robots with double clutch were installed on rally and racing cars in which speed and accuracy of gear shifting are of great importance.
If we compare the DSG box with a classic automatic, then the first option has more advantages. First, due to the more familiar structure of the main elements (the manufacturer can take any ready-made mechanical analogue as a basis), such a box will be cheaper on sale. The same factor affects the maintenance of the unit - the mechanics are more reliable and easier to repair.
This enabled the manufacturer to install an innovative transmission on budget models of their products. Secondly, many owners of vehicles with such a gearbox note an increase in the economy of the car compared to an identical model, but with a different gearbox.
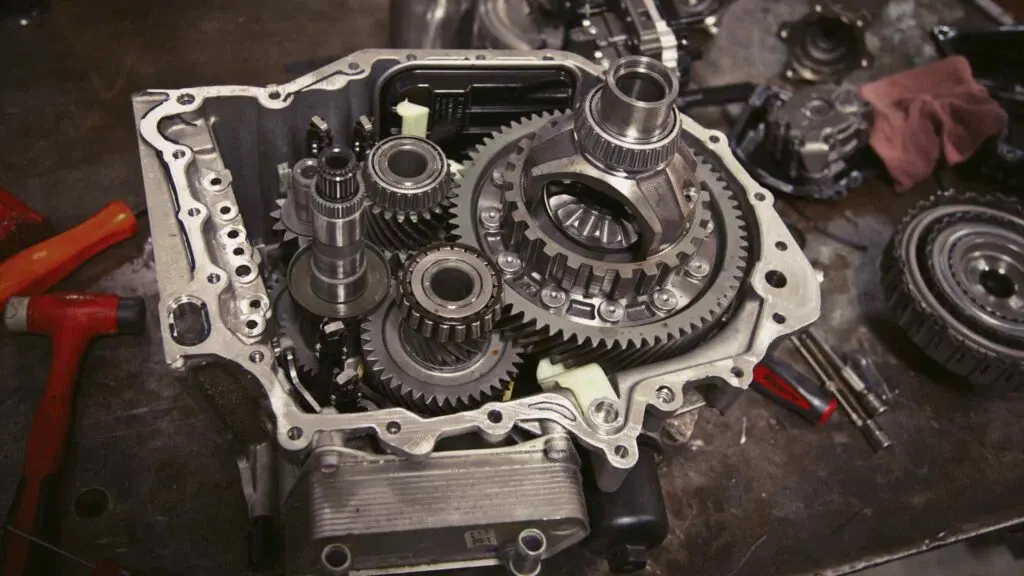
The engineers of the VAG concern have developed two variants of the DSG transmission. One of them is labeled 6, and the other is 7, which corresponds to the number of steps in the box. Also, a six-speed automatic uses a wet clutch, and a seven-speed analogue uses a dry clutch. In more detail about the pros and cons of the DSG box, as well as how else the DSG 6 model differs from the seventh modification, is described in separate article.
Advantages and disadvantages
The considered type of transmission has both positive and negative sides. The advantages of the box include:
- Such a transmission can be used in tandem with a power unit of almost any power;
- Compared to a variator and an automatic machine, the robotic version is cheaper, although this is a rather innovative development;
- Robots are more reliable than other automatic transmissions;
- Due to the internal similarity with mechanics, it is easier to find a specialist who will take on the repair of the unit;
- More efficient gear shifting allows the use of engine power without a critical increase in fuel consumption;
- By improving efficiency, the machine emits less harmful substances into the environment.
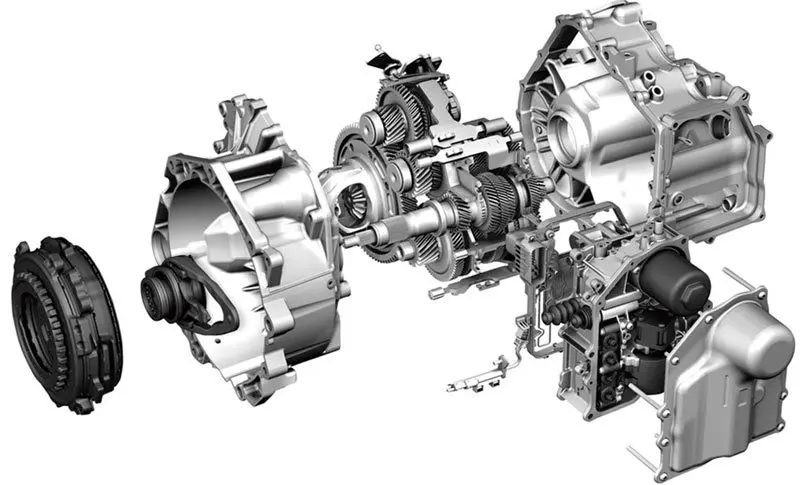
Despite the clear advantages over other automatic transmissions, the robot has several significant disadvantages:
- If the car is equipped with a single-disk robot, then the trip on such a vehicle cannot be called comfortable. When changing gears, there will be tangible jerks, as if the driver is abruptly throwing the clutch pedal on the mechanics.
- Most often, the clutch (less smoothness of engagement) and the actuators fail in the unit. This complicates the repair of transmissions, since they have a small working resource (about 100 thousand kilometers). It is rare that servos can be repaired and a new mechanism is expensive.
- As for the clutch, the disc resource is also very small - about 60 thousand. Moreover, approximately at half of the resource it is necessary to carry out the "connection" of the box under the condition of the friction surface of the parts.
- If we talk about the preselective modification of the DSG, then it proved to be more reliable due to less time for switching speeds (thanks to this, the car does not slow down so much). Despite this, the adhesion still suffers in them.
Taking into account the listed factors, we can conclude: as for the reliability and working life, mechanics have no equal yet. If emphasis is placed on maximum comfort, then it is better to choose a variator (what is its peculiarity, read here). It should be borne in mind that such a transmission will not provide an opportunity to save fuel.
In conclusion, we offer a short video comparison of the main types of transmissions - their pros and cons:
Questions and answers:
What is the difference between an automaton and a robot? The automatic transmission works at the expense of a torque converter (there is no rigid coupling with the flywheel through the clutch), and the robot is analogous to mechanics, only the speeds are switched automatically.
How to change gears on a robot box? The principle of driving a robot is identical to driving an automatic: the desired mode is selected on the selector, and the engine speed is regulated by the gas pedal. The speeds will switch on their own.
How many pedals are there in a car with a robot? Although the robot is structurally similar to a mechanic, the clutch is automatically disengaged from the flywheel, so a car with a robotic transmission has two pedals (gas and brake).
How to properly park a car with a robot box? The European model must be parked in A mode or in reverse gear. If the car is American, then there is a P mode on the selector.
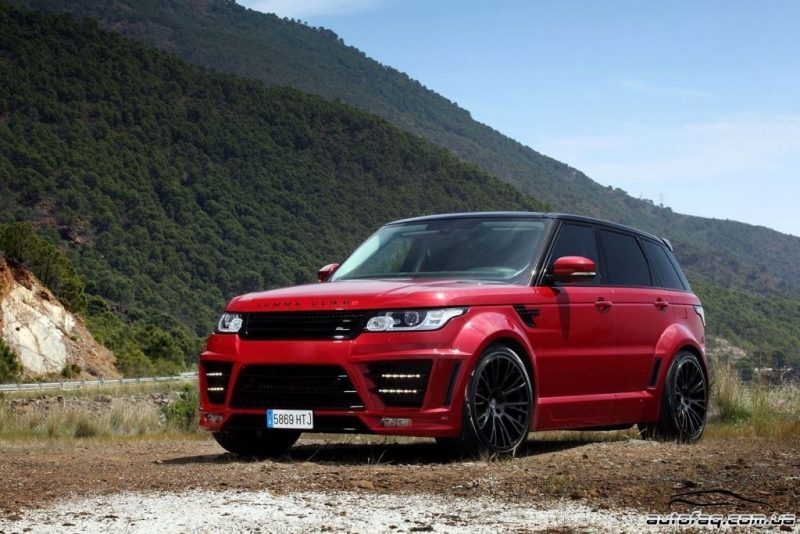

One comment
David
Hello, I need help, 203 coupes went into emergency mode, what can I do?