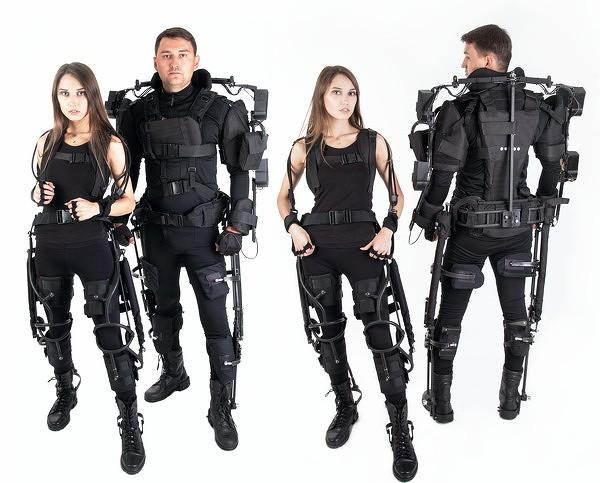
Exoskeletons
Although more and more has been heard about exoskeletons lately, it turns out that the history of this invention goes back to the nineteenth century. Find out how it has changed over the decades and what the turning points in its evolution looked like.
1. Illustration from the patent of Nikolai Yagn
1890 – The first innovative ideas for creating an exoskeleton date back to the 1890th century. In 420179, Nicholas Yagn patented in the United States (patent No. US XNUMX A) "A device for facilitating walking, running and jumping" (1). It was an armor made of wood, the purpose of which was to increase the speed of a warrior during a many-kilometer march. The design became a source of inspiration for further search for the optimal solution.
1961 - In the 60s, General Electric, together with a group of scientists from the University of Comell, began work on the creation of an electro-hydraulic suit that supports human exercise. Collaboration with the military on the Man Augmentation project led to the development of the Hardiman (2). The aim of the project was to create a suit that mimics the natural movements of a human, allowing him to lift objects weighing almost 700 kg. The costume itself weighed the same, but the tangible weight was only 20 kg.
2. General Electric prototype heat exchanger
Despite the success of the project, it turned out that its usefulness was negligible, and the initial copies would be expensive. Their limited mobility options and complex power system eventually rendered these devices unusable. During testing, it turned out that Hardiman can only lift 350 kg, and with prolonged use has a tendency to dangerous, uncoordinated movements. From further development of the prototype, only one arm was abandoned - the device weighed about 250 kg, but it was just as impractical as the previous exoskeleton.
70-s years. “Due to its size, weight, instability, and power problems, the Hardiman never went into production, but the industrial Man-Mate used some technology from the 60s. The rights to the technology were bought by Western Space and Marine, founded by one of the GE engineers. The product has been further developed and today exists in the form of a large robotic arm that can lift up to 4500 kg using force feedback, making it ideal for the steel industry.
3. Exoskeletons built at the Mihailo Pupin Institute in Serbia.
1972 – Early active exoskeletons and humanoid robots were developed at the Mihailo Pupin Institute in Serbia by a group led by prof. Miomir Vukobratovich. First, leg movement systems have been developed to support the rehabilitation of people suffering from paraplegia (3). When developing active exoskeletons, the institute also developed methods for analyzing and controlling human gait. Some of these advances have contributed to the development of today's high performance humanoid robots. In 1972, an active pneumatic exoskeleton with electronic programming for paralysis of the lower extremities was tested in an orthopedic clinic in Belgrade.
1985 “An engineer at Los Alamos National Laboratory is building an exoskeleton called the Pitman, power armor for infantrymen. The control of the device was based on sensors that scan the surface of the skull, placed in a special helmet. Given the capabilities of the technology of the time, it was too complex a design to manufacture. The limitation was primarily the insufficient computing power of computers. In addition, processing brain signals and converting them into exoskeleton movements remained technically practically impossible at that time.
4. Exoskeleton Lifesuit, designed by Monty Reed.
1986 — Monty Reed, US Army soldier who fractured his spine while skydiving, develops a survival suit exoskeleton (4). He was inspired by the descriptions of mobile infantry suits in Robert Heinlein's science fiction novel Starship Troopers, which he read while recuperating in the hospital. However, Reed did not begin work on his device until 2001. In 2005, he tested a prototype 4,8 rescue suit in the St. Patrick's Day race in Seattle, Washington. The developer claims to have set a walking speed record in robot suits, covering 4 kilometers at an average speed of 14 km/h. The prototype Lifesuit 1,6 was able to go 92 km fully charged and allowed to lift XNUMX kg.
1990 - present - The first prototype of the HAL exoskeleton was proposed by Yoshiyuki Sankai (5), prof. University of Tsukuba. Sankai spent three years - from 1990 to 1993 - identifying the neurons that control leg movement. It took him and his team another four years to prototype the equipment. The third HAL prototype, developed in the early 22nd century, was connected to a computer. The battery itself weighed almost 5 kg, which made it very impractical. In contrast, the later model HAL-10 weighed only 5 kg and had the battery and control computer wrapped around the user's waist. HAL-XNUMX is currently a four-limb medical exoskeleton (although a lower-limb-only version is also available) manufactured by the Japanese company Cyberdyne Inc. in collaboration with the University of Tsukuba.
5. Professor Yoshiyuki Sankai presents one of the exoskeleton models.
Works approximately 2 hours 40 minutes both indoors and outdoors. Helps to lift heavy objects. The location of the controls and drive in containers inside the case made it possible to get rid of the "backpack" so characteristic of most exoskeletons, sometimes resembling a large insect. People with hypertension, osteoporosis, and any heart condition should consult a physician before using HAL, and contraindications include, but are not limited to, a pacemaker and pregnancy. As part of the HAL FIT program, the manufacturer offers the possibility of using treatment sessions with an exoskeleton for both sick and healthy people. HAL's designer claims that the next stages of the upgrade will focus on creating a thin suit that will allow the user to move freely and even run.
2000 - prof. Homayoun Kazeruni and his team at Ekso Bionics are developing a Universal Human Cargo Carrier, or HULC (6) is a wireless exoskeleton with a hydraulic drive. Its purpose is to help warring soldiers carry loads weighing up to 90 kg for a long time, with a maximum speed of 16 km / h. The system was unveiled to the public at the AUSA Winter Symposium on February 26, 2009, when a licensing agreement was reached with Lockheed Martin. The dominant material used in this design is titanium, a lightweight but relatively expensive material with high mechanical and strength properties.
The exoskeleton is equipped with suction cups that allow you to carry objects weighing up to 68 kg (lifting device). Power is supplied from four lithium-polymer batteries, which ensure the normal operation of the device at optimal load up to 20 hours. The exoskeleton was tested in various combat conditions and with various loads. After a series of successful experiments in the fall of 2012, he was sent to Afghanistan, where he was tested during an armed conflict. Despite many positive reviews, the project was put on hold. As it turned out, the design made it difficult to perform certain movements and actually increased the load on the muscles, which contradicted the general idea of its creation.
2001 – The Berkeley Lower Extremity Exoskeleton (BLEEX) project, originally intended mainly for the army, is underway. Within its framework, promising results have been achieved in the form of autonomous solutions of practical importance. First of all, a robotic device was created, attached to the lower body to give the legs extra strength. The equipment was funded by the Defense Advanced Research Projects Agency (DARPA) and developed by the Berkeley Robotics and Human Engineering Laboratory, a division of the University of California, Berkeley Mechanical Engineering Department. The Berkeley exoskeleton system gives soldiers the ability to carry large payloads with minimal effort and over any type of terrain, such as food, rescue equipment, first aid kits, communications and weapons. In addition to military applications, BLEEX is currently developing civil projects. The Robotics and Human Engineering Laboratory is currently investigating the following solutions: ExoHiker - an exoskeleton designed mainly for expedition members where there is a need to transport heavy equipment, ExoClimber - equipment for people climbing high hills, Medical Exoskeleton - an exoskeleton for people with disabilities physical capabilities. lower limb mobility disorders.
8. Prototype Sarcos XOS 2 in action
текст
2010 – XOS 2 appears (8) is a continuation of the XOS exoskeleton from Sarcos. First of all, the new design has become lighter and more reliable, allowing you to lift loads weighing up to 90 kg in static. The device resembles a cyborg. The control is based on thirty actuators that act like artificial joints. The exoskeleton contains several sensors that transmit signals to the actuators via a computer. In this way, smooth and continuous operation takes place, and the user does not feel any significant effort. XOS weight is 68 kg.
2011 - present – The US Food and Drug Administration (FDA) approves the ReWalk medical exoskeleton (9). It is a system that uses strength elements to strengthen the legs and allows people with paralysis to stand up straight, walk and climb stairs. Energy is provided by a backpack battery. The control is carried out using a simple hand-held remote control that detects and corrects the user's movements. The whole thing was designed by Amit Goffer of Israel and is being sold by ReWalk Robotics Ltd (originally Argo Medical Technologies) for around PLN 85. dollars.
9 People Walk In ReWalk Exoskeletons
At the time of release, the equipment was available in two versions - ReWalk I and ReWalk P. The first is used by medical institutions for research or therapeutic purposes under the supervision of a medical professional. ReWalk P is intended for personal use by patients at home or in public areas. In January 2013, an updated version of ReWalk Rehabilitation 2.0 was released. This improved the fit for taller people and improved the control software. ReWalk requires the user to use crutches. Cardiovascular diseases and bone fragility are mentioned as contraindications. The limitation is also growth, within 1,6-1,9 m, and body weight up to 100 kg. This is the only exoskeleton in which you can drive a car.
10. Ex Bionics eLEGS
2012 Ekso Bionics, formerly known as Berkeley Bionics, unveils its medical exoskeleton. The project started two years earlier under the name eLEGS (10), and was intended for the rehabilitation of people with varying degrees of paralysis. Like ReWalk, the construction requires the use of crutches. The battery provides energy for at least six hours of use. Exo set costs about 100 thousand. dollars. In Poland, the project of the exoskeleton Ekso GT, a medical device designed to work with neurological patients, is known. Its design allows walking, including people after strokes, spinal cord injuries, patients with multiple sclerosis or with Guillain-Barré syndrome. The equipment can operate in several different modes, depending on the degree of dysfunction of the patient.
2013 – Mindwalker, a mind-controlled exoskeleton project, receives funding from the European Union. The design is the result of a collaboration between scientists from the Free University of Brussels and the Santa Lucia Foundation in Italy. The researchers tested different ways to control the device - they believe that the brain-neuro-computer interface (BNCI) works best, which allows you to control it with thoughts. Signals pass between the brain and the computer, bypassing the spinal cord. Mindwalker converts EMG signals, that is, small potentials (called myopotentials) that appear on the surface of a person's skin when muscles are working, into electronic movement commands. The exoskeleton is quite light, weighing only 30 kg without batteries. It will support an adult weighing up to 100 kg.
2016 – The ETH Technical University in Zurich, Switzerland, hosts the first Cybathlon sports competition for people with disabilities using assistive robots. One of the disciplines was the exoskeleton race on an obstacle course for people with paralysis of the lower extremities. In this demonstration of skills and technology, exoskeleton users had to perform tasks such as sitting on a couch and getting up, walking on slopes, stepping on rocks (like when crossing a shallow mountain river), and climbing stairs. It turned out that no one was able to master all the exercises, and it took the fastest teams more than 50 minutes to complete the 8-meter obstacle course. The next event will take place in 2020 as an indicator of the development of exoskeleton technology.
2019 – During summer demonstrations at the Commando Training Center in Lympston, UK, Richard Browning, inventor and CEO of Gravity Industries, showed off his Daedalus Mark 1 exoskeleton jet suit, which made a huge impression on the military, and not only the British. Six small jet engines - two of them are installed at the back and two in the form of additional pairs on each arm - allow you to climb to a height of up to 600 m. So far, there is only enough fuel for 10 minutes of flight ...
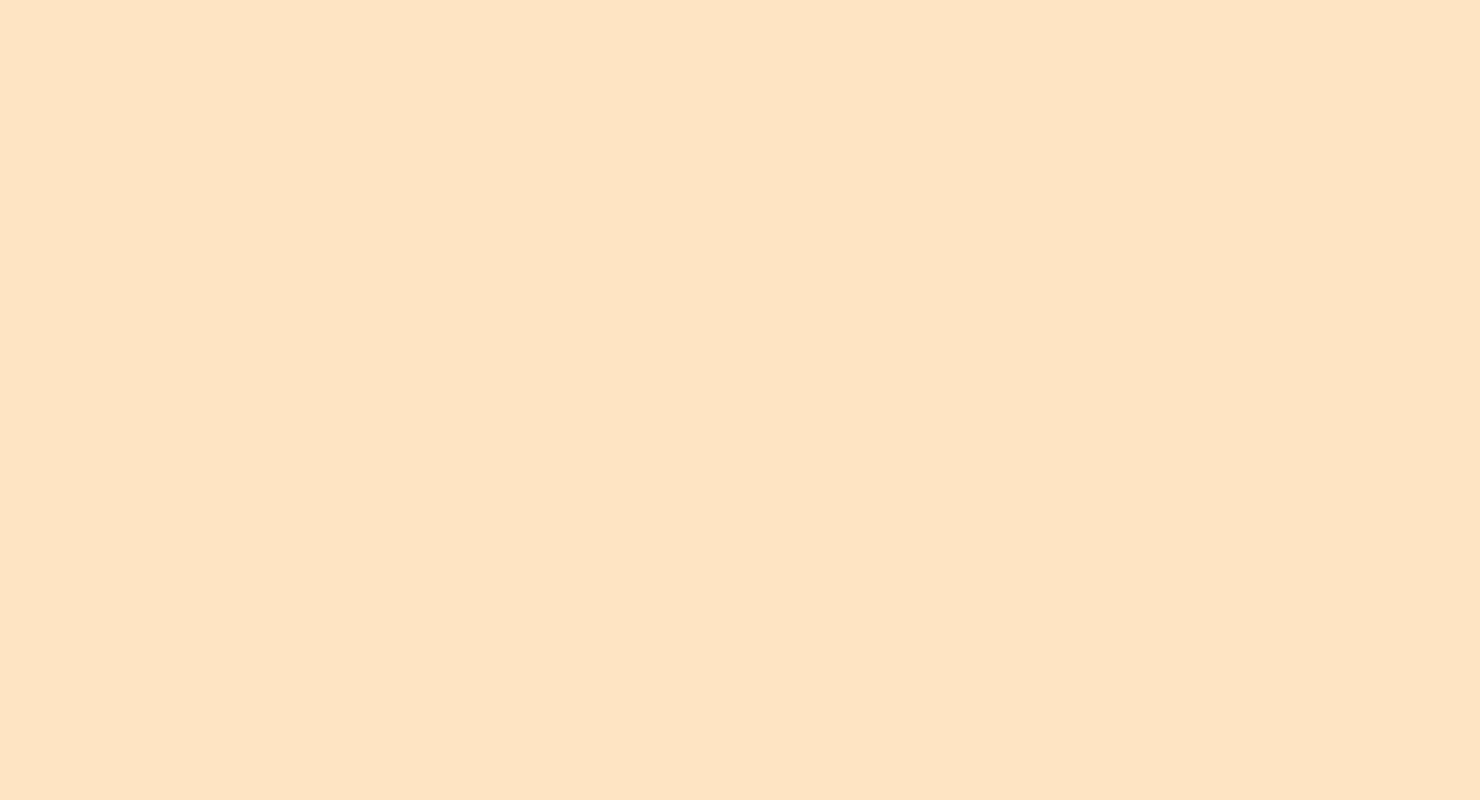
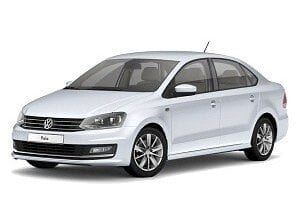