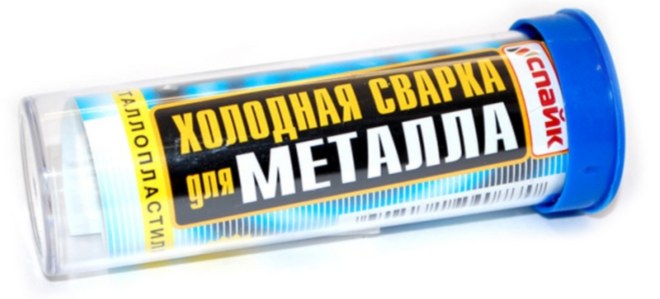
Cold welding for metal - instructions for use
"Cold welding" or "Fast steel" is a tool for gluing metal, plastic, wood and other surfaces. It should be noted that it has nothing to do with welding, since cold welding is a technological process in which metals are firmly connected to each other as a result of directed pressure and deformation without increasing temperature. Connection occurs at the level of molecular bonds. Well, “cold welding” glue has long been called that because of the fact that seams remain on the surface, as after hot welding.
Thus, "Cold welding" is a composite adhesive, which includes:
- epoxy resins;
- hardener;
- modifying additives.
Epoxy resins do not form a strong bond when cured, and therefore plasticizers are added to them to help withstand shock and vibration loads, which is very important when it comes to repairing body elements or the bottom of a car. In addition, the strength of the joint is increased by adding metal fillers based on aluminum or steel.
This tool is sold either in the form of tubes, one of which contains an adhesive base, and the other contains a hardener. Or in the form of putty - two-layer cylindrical bars.
Instructions for using cold welding
Before gluing metal parts, their surface must be completely cleaned of any dirt and dust. After that, they need to be degreased by any available means - solvent, alcohol, cologne.
If cold welding is in tubes, then you need to squeeze the required amount of glue from each tube into one container and mix well until a homogeneous mass is formed.
It is necessary to prepare the mixture in ventilated areas, since epoxy resin vapors can irritate the mucous membranes of the throat and nose.
It is necessary to use the resulting mass as quickly as possible - depending on the manufacturer, within 10-50 minutes. That is, if a large amount of repair work is to be carried out, then it is better to use welding in small batches, otherwise it will dry out and be unusable.
Then you simply apply putty to both surfaces, squeeze them a little and remove excess glue. The surfaces stick together very well and do not need to be pressed against each other with all the force. Just leave the part to be repaired until the adhesive sets. This may take ten minutes to an hour.
The glue completely hardens in a day, so leave the part alone until it completely hardens.
Putty "Cold welding"
Cold welding, which comes in the form of bars, it is also called putty, is used to seal cracks and seal holes. In its consistency, it resembles plasticine, so it is ideal for such work.
You need to work with it as follows:
- completely clean and degrease the surfaces to be glued;
- cut off the required amount of putty with a clerical knife;
- knead the putty well until a homogeneous plastic mass is obtained (do not forget to wear rubber gloves);
- the putty may heat up during kneading - this is normal;
- apply to the part;
- to level the layer, you can use a spatula, it must be moistened so that the putty does not stick to it;
- leave the part alone until the putty hardens.
Some craftsmen recommend pressing the surfaces to be glued together with a clamp or vice.
Whatever it was, but after solidification, the grease becomes hard as a stone. Please note that it is very easy to remove glue or putty with a heated soldering iron or a hot knife.
Recommendations for the use of cold welding
As we can see, cold welding is sold either in the form of a two-component adhesive, or in the form of a putty, which resembles plasticine in its consistency, which quickly hardens. For the best result, you need to take into account the manufacturer's recommendations, so the glue is used for joining or laying surfaces on top of each other, but the putty is suitable for tee or corner joints. It is also very good to close up various holes and cracks.
To enhance the effect or when it comes to a large area of repaired surfaces, the putty is used with a reinforcing mesh or fiberglass patches.
In the case of crack processing, their ends must be drilled so that the cracks do not grow further. They also do the same when repairing cracks on the windshield of a car, which we have already talked about on our website Vodi.su.
Please note that cold welding putty can also be used to smooth out dents. You can also fill the dent with glue, wait for it to dry, and smooth it out with a small spatula.
Cold welding manufacturers
If we talk about specific manufacturers and brands, we would recommend the following brands.
I open Steel - American product of the highest class. Sold in the form of bars of two-component putty, packed in plastic cylindrical containers. The weight of one tube is 57 grams. The composition of the epoxy adhesive includes, in addition to plasticizers and a hardener, also metal fillers, so Abro Steel can be used to repair:
- fuel tanks;
- cooling radiators;
- oil pans;
- mufflers;
- block heads and so on.
It can also be used in everyday life, for example, for sealing holes in metal-plastic or metal pipes, gluing aquariums, repairing tools and much more. Glue provides excellent connection at temperatures from minus 50 degrees to plus 150 degrees. It must be used according to the instructions above.
Poxypol - glue putty, which can be used in many ways. It hardens very quickly and provides the strongest possible adhesion. Repaired parts can be drilled and even threaded.
Diamond Press - Specially designed for car repair. They can repair cracks in the tank, muffler, cylinder block. In addition, it is used to secure nameplates - emblems of the manufacturer. It consists of epoxy resins and fillers on a natural or metal basis.
You can also name several popular brands: Blitz, Skol, Monolith, Forbo 671. All of them provide a reliable connection, even under water. If you are repairing parts in this way, and you want the connection to last as long as possible, follow these simple rules:
- when heated, the glue will dry much faster and provide good adhesion, so use a building hair dryer;
- surfaces that warm up during operation over 100 degrees are not recommended to be repaired in this way - the glue can withstand up to 150 degrees of heat for a short time, but it collapses with prolonged exposure;
- use at temperatures below five degrees Celsius is not recommended;
- store cold welding preferably at room temperature away from direct sunlight.
If you buy cold welding for industrial needs, then you can find a more voluminous packaging. For example, Metalox cold welding comes in half-liter cans and one such can is enough to repair 0,3 square meters. surfaces. There is also a more voluminous packaging - in metal buckets of 17-18 kilograms.
As the practice and experience of many drivers testifies, cold welding provides a reliable connection. But do not forget that this is one of the types of epoxy glue, albeit with the addition of metal fillers. Therefore, we would not recommend cold welding for the repair of key vehicle components and assemblies.
Video with recommendations and the principle of operation of cold welding.
Loading…
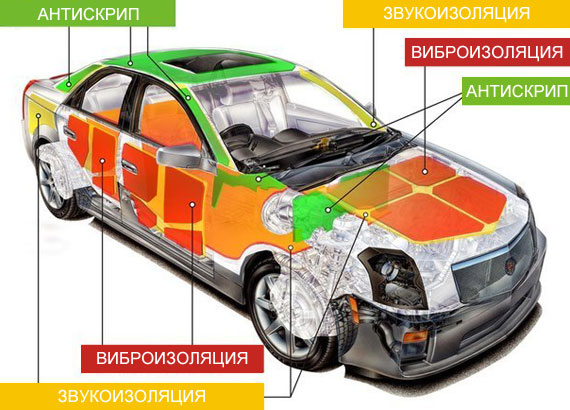
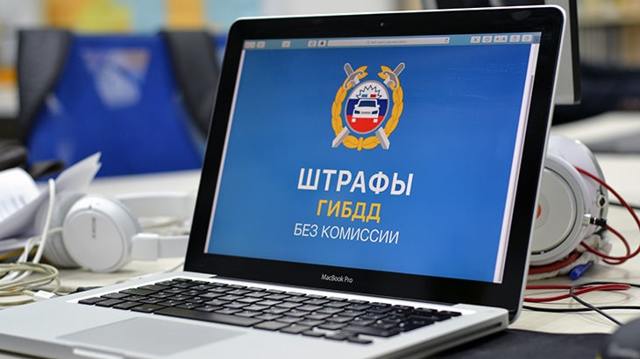