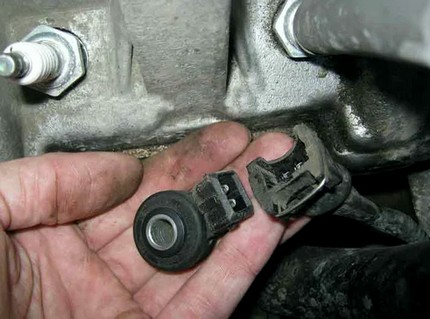
knock sensor failure
Content
knock sensor failure leads to the fact that the control unit ICE (ECU) ceases to detect the process of detonation during the combustion of the fuel mixture in the cylinders. Such a problem appears as a result of an outgoing signal that is too weak or, on the contrary, too strong. As a result, the “check ICE” light on the dashboard lights up, and the behavior of the car changes due to the operating conditions of the ICE.
in order to deal with the issue of knock sensor malfunctions, you need to understand the principle of its operation and the functions it performs.
How the knock sensor works
In ICE cars, one of two types of knock sensors can be used - resonant and broadband. But since the first type is already outdated and is rare, we will describe the operation of broadband sensors (DD).
The design of a broadband DD is based on a piezoelectric element, which, under mechanical action on it (that is, during an explosion, which, in fact, is detonation), supplies a current with a certain voltage to the electronic control unit. The sensor is tuned to perceive sound waves in the range from 6 Hz to 15 kHz. The design of the sensor also includes a weighting agent, which enhances the mechanical effect on it by increasing the force, that is, it increases the sound amplitude.
The voltage supplied by the sensor to the ECU through the connector pins is processed by the electronics and then it is concluded whether there is detonation in the internal combustion engine, and accordingly, whether the ignition timing needs to be adjusted, which will help eliminate it. That is, the sensor in this case is only a “microphone”.
Signs of a knock sensor breakage
With a complete or partial failure of the DD, a breakdown of the knock sensor is manifested by one of the symptoms:
- ICE shaking. With a serviceable sensor and control system in the internal combustion engine, this phenomenon should not be. By ear, the appearance of detonation can be indirectly determined by the metallic sound coming from the working internal combustion engine (knocking fingers). And excessive shaking and jerking during the operation of the internal combustion engine is the first thing by which you can determine the breakdown of the knock sensor.
- Decrease in power or “stupidity” of the internal combustion engine, which is manifested by a deterioration in acceleration or an excessive increase in speed at low speeds. This happens when, with an incorrect DD signal, spontaneous adjustment of the ignition angle is carried out.
- Difficulty starting the engine, especially “cold”, that is, at low temperatures after a long period of inactivity (for example, in the morning). Although it is quite possible this behavior of the car and at a warm ambient temperature.
- Increased fuel consumption. Since the ignition angle is broken, the air-fuel mixture does not meet the optimal parameters. Accordingly, a situation arises when the internal combustion engine consumes more gasoline than it needs.
- Fixing knock sensor errors. Usually, the reasons for their appearance are the signal from the DD going beyond the permissible limits, a break in its wiring, or a complete failure of the sensor. Errors will be indicated by the Check Engine light on the dashboard.
However, it should be borne in mind that such symptoms may indicate other breakdowns of the internal combustion engine, including other sensors. It is recommended to additionally read the ECU memory for errors that could occur due to incorrect operation of individual sensors.
knock sensor circuit failure
In order to more accurately identify damage to the DD, it is advisable to use electronic error scanners of the electronic control unit. Especially if the “check” control lamp lit up on the dashboard.
The best device for this task would be Scan Tool Pro Black Edition - an inexpensive Korean-made device with great functionality that works with the OBD2 data transfer protocol and is compatible with most modern cars, as well as programs for a smartphone and computer (with a Bluetooth or Wi-Fi module).
you need to consider whether there is one of 4 knock sensor errors and errors in the DMRV, lambda or coolant temperature sensors, and then view the real-time indicators for the lead angle and fuel mixture composition (an error for the DD sensor pops up with significant depletion).
Often, the error p0325 “Open circuit in the knock sensor circuit” indicates problems in the wiring. This may be a broken wire or, more often, oxidized contacts. It is necessary to carry out preventive maintenance of the connectors on the sensor. Sometimes the error p0325 appears due to the fact that the timing belt slips 1-2 teeth.
P0328 Knock Sensor Signal High is often an indication of a problem with the high voltage wires. namely, if the insulation breaks through them or the piezoelectric element. Similarly, the indicated error may also occur due to the fact that the timing belt has jumped a couple of teeth. For diagnostics, you need to check the marks on it and the condition of the washers.
Errors p0327 or p0326 are usually generated in the computer memory due to a low signal from the knock sensor. The reason may be poor contact from it, or weak mechanical contact of the sensor with the cylinder block. To eliminate the error, you can try to process both the mentioned contacts and the sensor itself with WD-40. It is also important to check the sensor mounting torque as this parameter is critical to its operation.
In general, it can be noted that the signs of a breakdown of the knock sensor are very similar to the symptoms characteristic of late ignition, because the ECU, for safety reasons for the motor, tries to automatically produce as late as possible, since this eliminates the destruction of the motor (if the angle is too early, then besides detonation appears, not only power drops, but there is a risk of valve burnout). So, in general, we can conclude that the main signs are exactly the same as with incorrect ignition timing.
Causes of knock sensor failure
As for the reasons why there are problems with the knock sensor, these include the following breakdowns:
- Violation of mechanical contact between the sensor housing and the engine block. As practice shows, this is the most common reason. Typically, the sensor itself has a round shape with a mounting hole in the middle, through which it is attached to its seat using a bolt or stud. Accordingly, if the tightening torque decreases in the threaded connection (the pressing of the DD to the ICE is weakened), then subsequently the sensor does not receive sound mechanical vibrations from the cylinder block. In order to eliminate such a breakdown, it is enough to tighten the mentioned threaded connection, or replace the fixing bolt with a fixing pin, since it is more reliable and provides a tight mechanical connection.
- Sensor wiring problems. In this case, there may be various problems, for example, shorting the supply or signal wire to ground, mechanical damage to the wire (especially in places where it is bent), damage to the internal or external insulation, breakage of the entire wire or its individual cores (supply, signal), shielding failure. In case the problem is solved by restoring or replacing its wiring.
- Bad contact at the connection point. This situation sometimes happens if, for example, the plastic latch is broken at the point where the sensor contacts are connected. Sometimes, as a result of shaking, the contact is simply broken, and, accordingly, the signal from the sensor or the power to it simply does not reach the addressee. For repair, you can try to replace the chip, fix the contact, or by another mechanical method try to connect two pads with contacts.
- Complete sensor failure. The knock sensor itself is a fairly simple device, so there is nothing special to break, respectively, and it rarely fails, but it happens. The sensor cannot be repaired, therefore, in the event of a complete breakdown, it must be replaced with a new one.
- Problems with the electronic control unit. In the ECU, as in any other electronic device, software failures can occur, which leads to incorrect perception of information from the DD, and, accordingly, the adoption of incorrect decisions by the unit.
What are the knock sensor failures?
Can I drive with a faulty knock sensor? This question is of interest to motorists who first encountered this problem. In general terms, the answer to this question can be formulated as follows - in the short term, you can use the car, but at the earliest opportunity, you need to carry out appropriate diagnostics and fix the problem.
Indeed, according to the principle of operation of the computer, when a breakdown of the fuel knock sensor occurs, it automatically delayed ignition is installed in order to exclude damage to the parts of the piston group in the event of real detonation during the combustion of the fuel mixture. As a result - fuel consumption goes up and significantly falling dynamics which becomes especially noticeable as the rpm increases.
What happens if you disable the knock sensor completely?
Some car owners even try to disable the knock sensor, since under normal operating conditions and refueling with good fuel, it may seem unnecessary. However, it is not! Because detonation is not only due to bad fuel and problems with spark plugs, compression and misfires. Therefore, if you disable the knock sensor, the consequences may be as follows:
- quick failure (breakdown) of the cylinder head gasket with all the ensuing consequences;
- accelerated wear of the elements of the cylinder-piston group;
- cracked cylinder head;
- burnout (full or partial) of one or more pistons;
- failure of the jumpers between the rings;
- connecting rod bend;
- burning of valve plates.
This is due to the fact that when this phenomenon occurs, the electronic control unit will not take measures to eliminate it. Therefore, in no case should you turn it off and put a jumper from the resistance, because this is fraught with expensive repairs.
How to determine if the knock sensor is broken
When the first signs of a DD failure appear, the logical question is how to check and determine if the knock sensor is broken. First of all, it must be said that checking the knock sensor is possible without removing it from the cylinder block, so after dismantling it from the seat. And at first it is better to perform several tests when the sensor is screwed to the block. Briefly, the procedure looks like this:
- set the idle speed to approximately 2000 rpm;
- with some metal object (small hammer, wrench) strike one or two blows weak (!!!) on the body of the cylinder block in the nominal vicinity of the sensor (you can lightly hit it on the sensor);
- if the engine speed drops after that (this will be audible), it means that the sensor is working;
- the speed remained at the same level - you need to make an additional check.
To check the knock sensor, a motorist will need an electronic multimeter capable of measuring the value of electrical resistance, as well as DC voltage. The best way to check is with an oscilloscope. The sensor operation diagram taken with it will clearly show whether it is operational or not.
But since only a tester is available to an ordinary motorist, it is enough to check the resistance readings that the sensor gives out when tapped. The resistance range is within 400 ... 1000 Ohm. it is also mandatory to carry out an elementary check of the integrity of its wiring - whether there is a break, insulation damage or short circuit. You can't do without the help of a multimeter.
If the test showed that the fuel knock sensor is working, and the error about the sensor signal going out of range, then it may be worth looking for the cause not in the sensor itself, but in the operation of the internal combustion engine or gearbox. Why? Sounds and vibration are to blame for everything, which DD can perceive as detonation of fuel and incorrectly adjust the ignition angle!
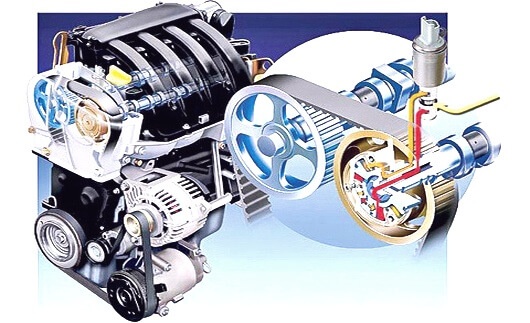
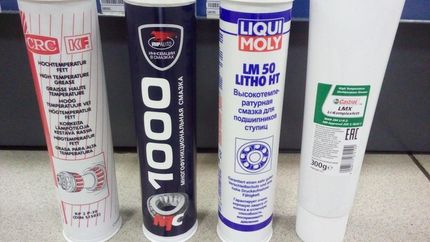