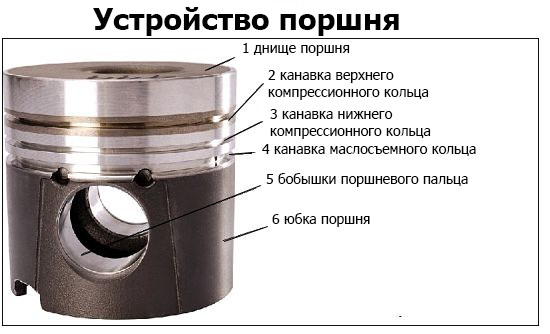
ICE piston. Device and purpose
Content
The fuel mixture that burns in the engine cylinder releases heat energy. Then it turns into a mechanical action that makes the crankshaft rotate. The key element of this process is the piston.
This detail is not as primitive as it might seem at first glance. It would be a big mistake to consider him as a simple pusher.
The piston is located in the cylinder, where it reciprocates.
As it moves toward top dead center (TDC), the piston compresses the fuel mixture. In a gasoline internal combustion engine, it ignites at a moment close to maximum pressure. In a diesel engine, ignition occurs directly due to high compression.
The increased pressure of the gases formed during combustion pushes the piston in the opposite direction. Together with the piston, the connecting rod articulated with it moves, which makes it rotate. So the energy of compressed gases is converted into torque, transmitted through the transmission to the wheels of the car.
During combustion, the temperature of the gases reaches 2 thousand degrees. Since combustion is explosive, the piston is subjected to strong shock loads.
Extreme loading and near-extreme operating conditions require special requirements for the design and materials used for its manufacture.
When designing pistons, there are a number of important points to consider:
- the need to ensure a long service life, and therefore, to minimize the wear of the part;
- prevent burnout of the piston in high-temperature operation;
- ensure maximum sealing to prevent gas breakthrough;
- minimize losses due to friction;
- ensure efficient cooling.
The piston material must have a number of specific properties:
- significant strength;
- maximum possible thermal conductivity;
- heat resistance and the ability to withstand sudden changes in temperature;
- the coefficient of thermal expansion should be small and be as close as possible to the corresponding coefficient of the cylinder in order to ensure good sealing;
- corrosion resistance;
- antifriction properties;
- low density so that the part is not too heavy.
Since the material that ideally meets all these requirements has not yet been created, one has to use compromise options. Pistons for internal combustion engines are made of gray cast iron and aluminum alloys with silicon (silumin). In composite pistons for diesel engines, it happens that the head is made of steel.
Cast iron is quite strong and wear-resistant, tolerates strong heat well, has anti-friction properties and small thermal expansion. But due to the low thermal conductivity, the cast iron piston can heat up to 400°C. In a gasoline engine, this is unacceptable, as it can cause pre-ignition.
Therefore, in most cases, pistons for automotive internal combustion engines are made by stamping or casting from silumin containing at least 13% silicon. Pure aluminum is not suitable, as it expands too much when heated, which leads to increased friction and scuffing. These can be fakes that you can run into when purchasing spare parts in dubious places. To prevent this from happening, contact the reliable ones.
The aluminum alloy piston is lightweight and conducts heat well, so that its heating does not exceed 250 ° C. This is quite suitable for internal combustion engines running on gasoline. The anti-friction properties of silumin are also quite good.
At the same time, this material is not without drawbacks. As the temperature rises, it becomes less durable. And because of the significant linear expansion when heated, additional measures must be taken to preserve the seal around the perimeter of the head and not reduce compression.
This part has the shape of a glass and consists of a head and a guide part (skirt). In the head, in turn, it is possible to distinguish the bottom and the sealing part.
Bottom
It is the main working surface of the piston, it is it that perceives the pressure of expanding gases. Its surface is determined by the type of unit, the placement of nozzles, candles, valves and the specific CPG device. For ICEs using gasoline, it is made flat or concave with additional cutouts to avoid valve defects. The convex bottom gives increased strength, but increases heat transfer, and therefore is rarely used. Concave allows you to organize a small combustion chamber and provide a high compression ratio, which is especially important in diesel units.
Sealing part
This is the side of the head. Grooves for piston rings are made in it around the circumference.
Compression rings play the role of a seal, preventing the leakage of compressed gases, and oil scrapers remove lubricant from the wall, preventing it from entering the combustion chamber. Oil flows under the piston through the holes in the groove and then returns to the oil sump.
The section of the lateral side between the edge of the bottom and the upper ring is called the fire or heat zone. It is he who experiences the maximum thermal effect. To prevent burnout of the piston, this belt is made wide enough.
Guide part
Does not allow the piston to warp during reciprocating motion.
In order to compensate for thermal expansion, the skirt is made curvilinear or cone-shaped. On the side, an anti-friction coating is usually applied.
Inside there are bosses - two influxes with holes for the piston pin, on which the head is put on.
On the sides, in the area of \uXNUMXb\uXNUMXbthe bosses, small indentations are made to prevent thermal deformations and the occurrence of scoring.
Since the temperature regime of the piston is very stressful, the issue of its cooling is very important.
Piston rings are the main way to remove heat. Through them, at least half of the excess thermal energy is removed, which is transferred to the cylinder wall and then to the cooling jacket.
Another important heat sink channel is lubrication. Oil mist in the cylinder, lubrication through the hole in the connecting rod, forced spraying with an oil nozzle and other methods are used. More than one third of the heat can be removed by circulating the oil.
In addition, part of the thermal energy is spent on heating the fresh portion of the combustible mixture that has entered the cylinder.
The rings maintain the desired amount of compression in the cylinders and remove the lion's share of the heat. And they account for about a quarter of all friction losses in the internal combustion engine. Therefore, the importance of the quality and condition of the piston rings for the stable operation of the internal combustion engine can hardly be overestimated.
Usually there are three rings - two compression rings on top and one oil scraper on the bottom. But there are options with a different number of rings - from two to six.
The groove of the upper ring in silumin It happens that it is done with a steel insert that increases wear resistance.
Rings are made from special grades of cast iron. Such rings are characterized by high strength, elasticity, wear resistance, low coefficient of friction and retain their properties for a long time. Additions of molybdenum, tungsten and some other metals give additional heat resistance to piston rings.
New ones need grinding in. If you have replaced the rings, be sure to run the internal combustion engine for some time, avoiding intense operating conditions. Otherwise, unlapped rings may overheat and lose elasticity, and in some cases even break. The result may be seal failure, loss of power, lubricant entering the combustion chamber, overheating and burnout of the piston.
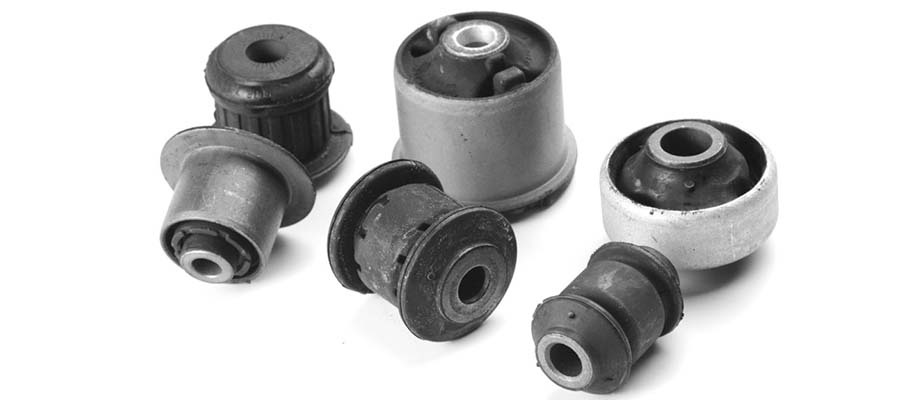
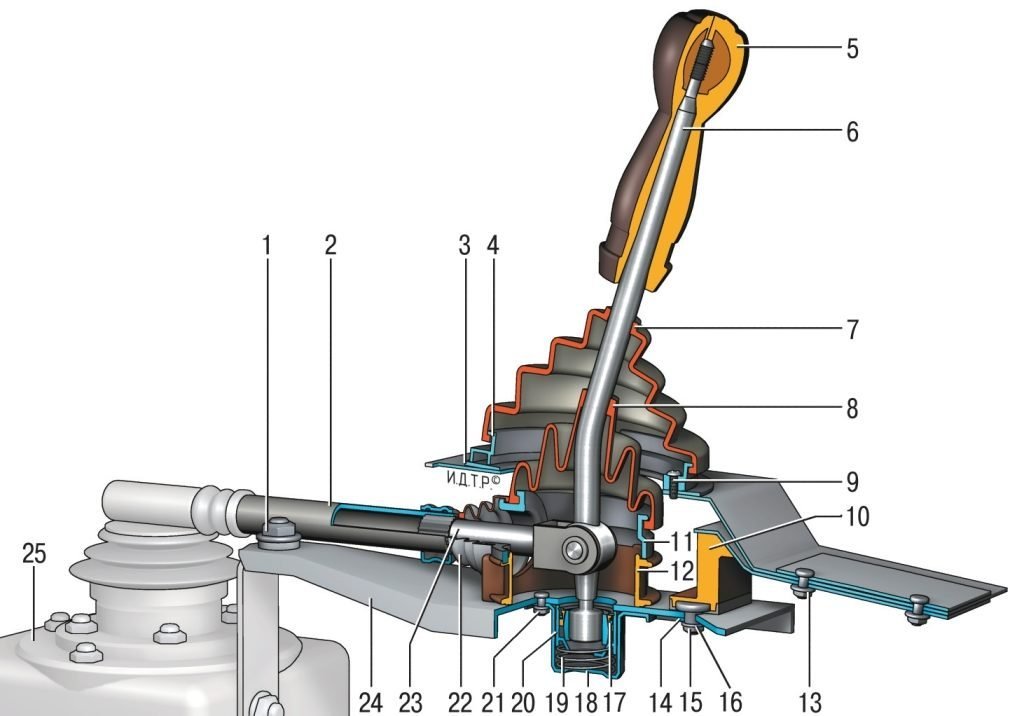