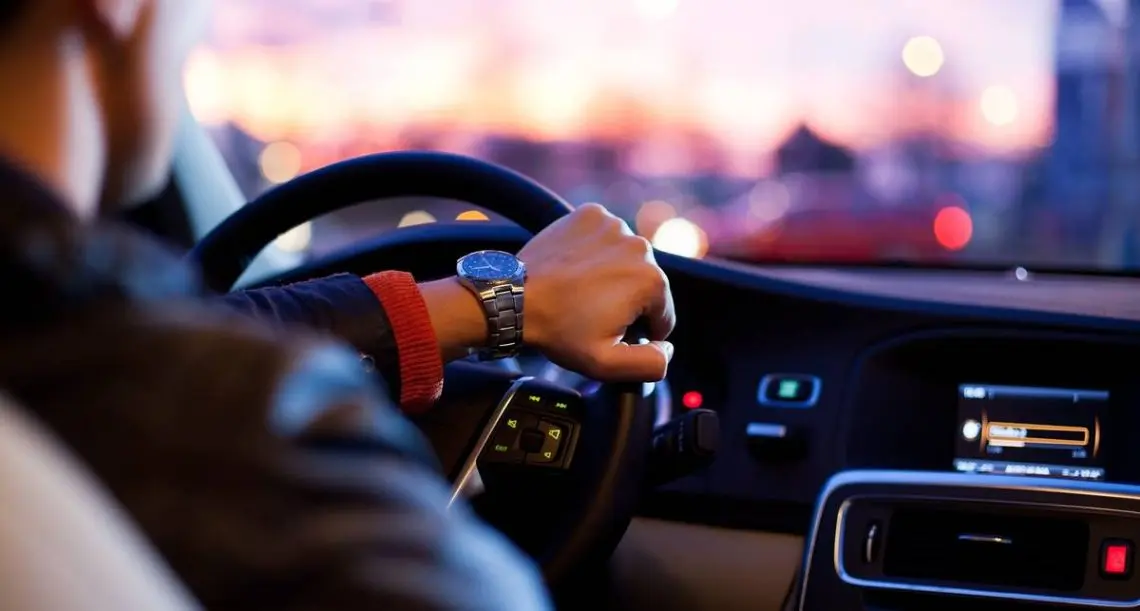
Fuel Injector Problems and Troubleshooting
Needle injectors… In modern engines, needle injectors are used mainly in gasoline engines, and more specifically in GDI (gas direct injection). As we have discussed in previous articles, GDI atomizes and atomizes fuel directly into the combustion chamber, on top of the piston. Due to the configuration of the pintal, carbon deposits form on the pintal cone, which disturb the spray pattern. As buildup increases, the uneven distribution of the jet will result in an uneven burn that will develop into misfiring or rattling...and possibly can create a hot spot on the piston or, in extreme cases, melt the hole in the piston. Unfortunately, this condition is corrected (possibly) by applying a "cleaning" fuel additive, mechanically flushing the injection system with special equipment and a concentrated solution, or removing the injectors for service or replacement.
Multi-hole injectors are the main injectors used in diesel engines. The biggest problem facing any modern diesel engine today is the quality and cleanliness of the fuel. As mentioned earlier, modern Common Rail systems reach pressures of up to 30,000 psi. In order to achieve such high pressures, the internal tolerances are much tighter than in previous versions of the nozzles (some rotational tolerances are 2 microns). Since the fuel is the only lubricant for the injectors and therefore the injectors, a clean fuel is needed. Even if you change the filters in a timely manner, part of the problem is the fuel supply... almost all underground tanks have contaminants (dirt, water or algae) settled on the bottom of the tank. You should NEVER refuel if you see a fuel truck delivering fuel (because the speed of the incoming fuel affects what's in the tank) - the problem is that the van could have just left and you didn't see it!!
Water in fuel is a huge problem as water raises the boiling point of the fuel, but even more so it negatively affects the lubricity of the fuel which is critical...especially since the sulfur that was there as a lubricant was removed by EPA decree. Water in fuel is the main cause of injector tip failure. If you have your own above ground storage tanks, the condensate that forms inside the tank above the fuel line (especially in rapidly changing temperatures) will form droplets and go straight to the bottom of the tank. Keeping these storage tanks full will reduce this problem… Reconnecting the storage tank is recommended if you have gravity feed at the bottom of the tank.
Dirty or algae fuel is also a problem with modern high pressure systems. You can usually tell if contamination is a problem on inspection... a few photos are attached to the letter.
Another problem we face in North America is the actual quality or flammability of the fuel itself. The cetane number is a measure of this. Diesel fuel contains more than 100 components that affect the cetane number (which is similar to the octane number of gasoline).
In North America, the minimum cetane number is 40... in Europe, the minimum is 51. It's worse than it sounds because it's a logarithmic scale. The only thing that can be done is to use an additive to improve both the cetane number and lubricity. They are readily available…just stay away from those with alcohol…they should only be used as a last resort when the fuel line is frozen or paraffin is present. The alcohol will destroy the lubricity of the fuel, causing the pump or injectors to seize.

