
Section: Workshop Practice - Development of wheel bearing modules and their friction properties
Patronage: Schaeffler Polska Sp. z oo FAG offers new bearing designs of the second and third generation, which, in accordance with market requirements, are characterized by a friction reduction of up to 30%. The share in fuel consumption of individual vehicle components is small and amounts to about 0,7%. However, every little refinement has a positive effect on the development of modern cars.
Faculty: Practice workshop
Patronage: Schaeffler Polska Sp. Mr. Fr.
Modern first, second and third generation modular wheel bearings have a similar internal structure, two rows of balls, to provide the necessary rigidity and absorb lateral forces. The weight of the vehicle and the corresponding bearing preload create a frictional moment between the raceway and the balls moving along it, which is approximately 45% of the total friction in the wheel bearing. The largest component of the total friction, approximately 50%, is the friction caused by the seal. Generally wheel bearings should be lubricated for life. Therefore, the purpose of the seal is to keep grease in the bearing and protect the bearing from external contaminants and moisture. The remaining friction component, i.e. about 5%, is a loss caused by a change in the consistency of the lubricant.
Friction optimization
Thus, optimization of the frictional properties of wheel bearings can only be carried out on the basis of the three factors mentioned. above points. It is difficult to reduce the friction associated with the movement of the balls along the raceway, since the bearing preload associated with the respective vehicle mass is constant. The work of developing the coating of the raceway and the material from which the balls are turned is costly and cannot bring tangible results compared to the costs. Another problem is the difficulty in achieving an improvement in the frictional properties of the lubricant.
3rd generation bearing seal
The optimal solution would be a bearing seal that is 100% efficient without causing frictional losses. FAG has developed designs for third generation wheel bearing modules. A metal shield is used at the drive end of the bearing and is pressed into the inner ring. It has no contact with the rotating parts of the bearing and therefore creates no friction. An additional protective cover is used on the wheel side, so that the required sealing on this side can only be limited by a lip seal. Thus, in a wheel bearing of this design, friction losses can be reduced by about 30%.
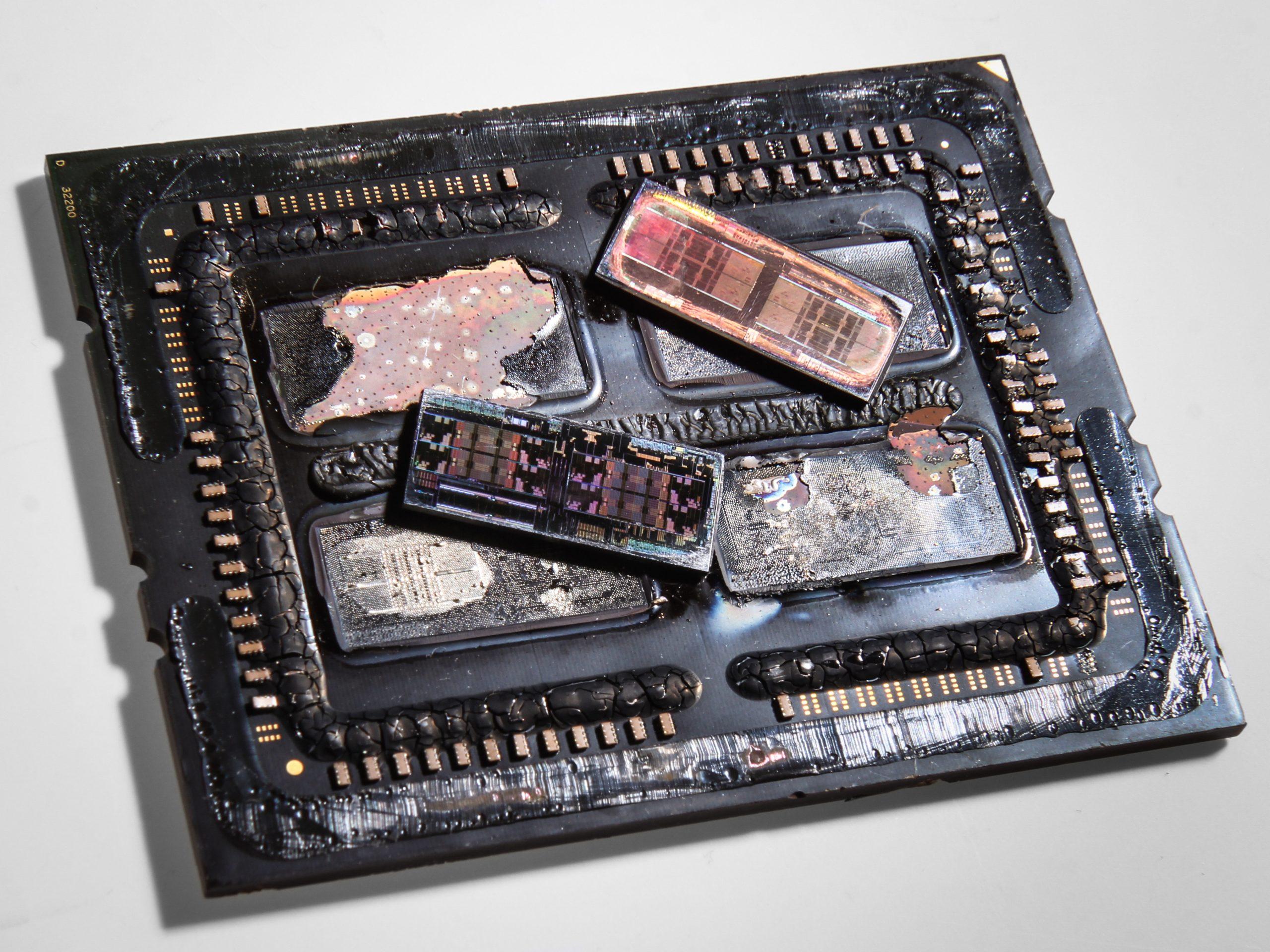
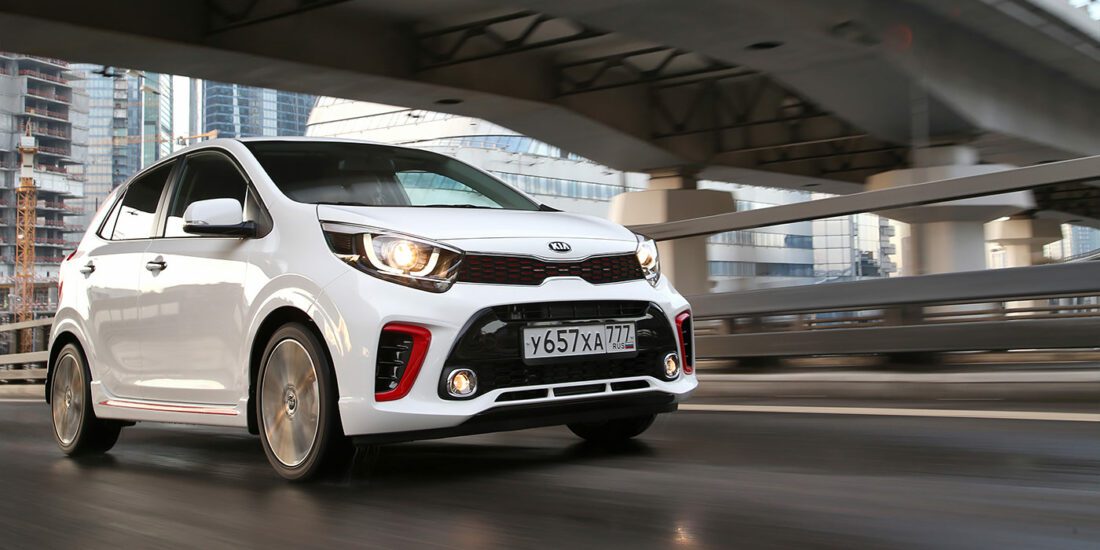