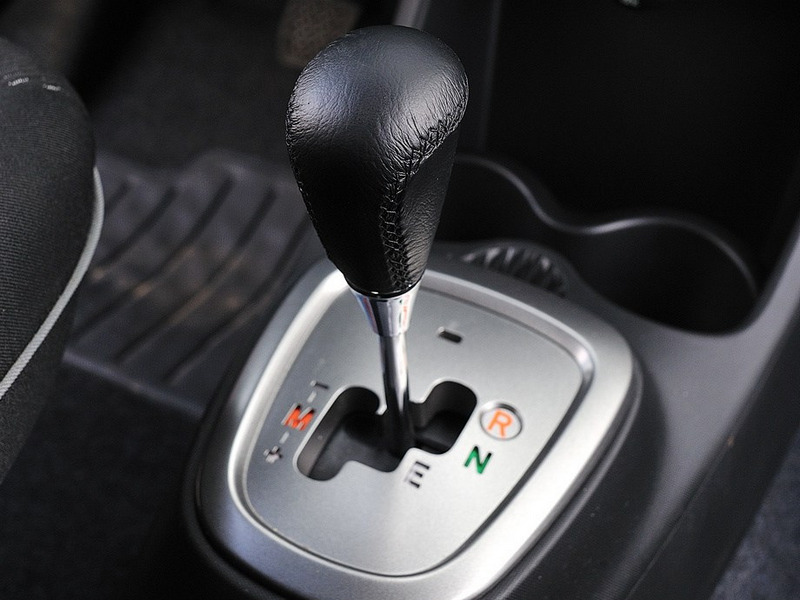
Manual transmission - robotic gearbox
Content
The robotic box is the "successor" of the time-tested "mechanics". The essence of her work is to free the driver from constant gear changes. In the manual transmission, this is performed by a “robot” - a special microprocessor control unit.
The robotic unit is arranged quite simply: it is a standard manual transmission (manual box), clutch and shift systems, as well as a modern microprocessor and a number of sensors. Many people believe that a manual transmission is an automatic transmission, however, according to the principle of operation and the general device, a robotic transmission is closer to “mechanics” than to an “automatic”. Although there is one constructive similarity with the automatic transmission - this is the presence of a clutch in the box itself, and not on the flywheel. In addition, the latest models of vehicles with manual transmission are equipped with two clutches at once.
The main components of the manual transmission
The first robotic boxes began to be installed on cars in the 1990s. In fact, such “robots” were ordinary manual transmissions, only the gears and clutch in them were switched by hydraulic or electric drives. Such units were installed on cars of many automakers and were a cheap alternative to a more expensive "machine". Such "robots" had one clutch disc and often worked with shift delays, which is why the car moved in a "ragged" mode of movement, it was difficult to complete overtaking and hardly joined the stream. In modern automotive industry, single-disk manual transmissions are practically not used.
Today, automakers around the world are using the second generation of robotic gearboxes - the so-called DSG gearboxes with two clutches (Direct Shift Gearbox). The specifics of the functioning of the DSG robotic box is that while one gear is running, the next one is already completely ready for change. Due to this, the DSG manual transmission works as quickly as possible, even a professional driver will not be able to switch gears so quickly on the “mechanics”. According to market analysts, in the future, the clutch pedal to control the vehicle will disappear, as it is easier and more convenient to control the car through the efforts of the robot.
The robotic gearbox with DSG is also assembled according to the mechanical principle, but is equipped with two drive shafts (rods), and not one. Moreover, these shafts are one in the other. The outer rod is hollow, the primary shaft is inserted into it. On each of them there are gears of different drives:
- on the outside - gears for drives of the 2nd, 4th and 6th gears;
- on the inside - gears for drives of the 1st, 3rd, 5th and reverse gears.
Each shaft of the DSG "robot" is equipped with its own clutch. In order to enable / disable the clutch, as well as move the synchronizers in the box, actuators are used - the clutch and gear shift system. Structurally, the actuator is an electric motor with a gearbox. Some car models are equipped with a hydraulic actuator in the form of a hydraulic cylinder.
The main node of the manual transmission with DSG is a microprocessor control unit. Sensors from the engine and electronic active safety systems are connected to it: ABS, ESP and others. For ease of maintenance, the microprocessor unit is located in the case of the on-board computer. The data from the sensors is promptly sent to the microprocessor, which automatically "makes a decision" on the up/downshift.
Advantages of a "robot"
Some drivers, tired of constantly shifting gears on cars with a manual transmission, want to buy a car with an automatic transmission. But this is a rather expensive version. For comparison: the models presented at the Favorit Motors showroom with the same power unit can be selected both with a “mechanics” and “automatic” gearboxes, but their cost will differ significantly. A car with automatic transmission will be more expensive than “mechanics” by 70-100 thousand rubles or more, depending on the make and model of the car.
In such cases, a vehicle with a DSG manual transmission can be a worthy solution: this is a kind of “budget” version of an automatic transmission. In addition, such a “robot” retains all the advantages of a manual transmission:
- economy in fuel consumption;
- ease of maintenance and repair;
- high efficiency even at maximum torque.
The specifics of the work of the RKPP
When starting off in a manual transmission, as in a manual transmission, it is necessary to smoothly engage the clutch. The driver only needs to press the switch lever, and then only the robot will work. Guided by the signal received from the actuator, the microprocessor starts to rotate the gearbox, as a result of which the first clutch is activated on the primary (internal) shaft of the car box. Further, as it accelerates, the actuator blocks the first gear and drives the next gear on the outer shaft - the second gear is engaged. And so on.
Specialists of Favorit Motors Group of Companies note that today, many major automakers, as new projects are implemented, bring their improvements and functionality to the operation of the manual transmission. Robotic gearboxes with maximum shifting speed and innovative developments are now installed on cars of many brands. For example, Favorit Motors has Ford Fiesta cars equipped with both a conventional manual gearbox and a 6-speed robotic one.
Features of the DSG robotic gearbox
Two independent clutches help to avoid jerks and delays during the operation of the "robot", improve the dynamic characteristics of the car and provide comfortable driving. Due to the presence of a dual clutch, the next gear is engaged while the previous gear is still engaged, which makes the transition to it smooth and maintains traction in full, as well as saves fuel. The first clutch includes even gears, and the second - odd.
Preselective robotic units appeared in the 1980s, but then they were used only in racing and rally cars Peugeot, Audi, Porsche. And today, the robotic DSG dual-clutch transmission is in fact the most ideal automatic transmission that is used on mass-produced cars. "Robot" with DSG provides increased acceleration compared to the traditional "automatic" box, as well as more economical fuel consumption (about 10% less fuel is spent). It is noteworthy that the gears on such a "robot" can also be switched manually using the Tiptronic system or the steering column paddle.
DSG "robots" have 6 or 7 gearshifts. They are also known by other trade names - S-tronic, PDK, SST, DSG, PSG (depending on the automaker). The first DSG box appeared in 2003 on a number of Volkswagen Group car models, it had 6 steps. Later, similar designs began to be used in the lines of almost all automakers in the world.
The six-speed DSG box operates on a wet clutch. She has a clutch block immersed in a coolant that has frictional properties. The clutches in such a “robot” are hydraulically controlled. DSG 6 have high wear resistance, they are installed on cars of class D and above.
The seven-speed DSG "robot" differs from the "six-speed" in that it has a "dry" clutch, which is controlled by an electric pump. The DSG 7 box requires much less transmission fluid and increases the efficiency of the motor. Such manual transmissions are usually installed on cars of small and medium class (B and C), the engine of which has a torque of more than 250 Hm.
Recommendations of Favorit Motors specialists on driving a car with a manual transmission
The DSG robotic box demonstrates optimal performance in combination with both powerful engines and budget motors. The similarity between a robotic gearbox and an automatic gearbox is only external, but according to the principle of operation of the manual transmission, this is a continuation of the best traditions of “mechanics”. Therefore, when driving a car with a “robot”, Favorit Motors car service masters recommend following some simple rules. This will make it possible to delay the repair work in the device as much as possible and, in general, reduce the current wear of the mechanisms.
- It is recommended to accelerate slowly, without depressing the gas pedal by more than half.
- If there is a long rise, then it is more advisable to switch the box to manual mode and select a lower gear.
- If possible, select driving modes in which the clutch is in the disengaged mode.
- When stopping at traffic lights, it is recommended to shift to neutral instead of holding the brake pedal.
- When driving around the city during rush hours with constant short stops, it is more advisable to switch to manual mode and drive only in first gear.
Professional drivers and service center specialists advise using these recommendations when driving a car with a manual transmission in order to maintain the long-term performance of the box itself and the clutch.
Nuances in the work of the RKPP
The robotic gearbox is a relatively new type of design, and therefore, in case of breakdowns or any shortcomings in the work, the car owner must know exactly where to turn for professional help.
Favorit Motors Group of Companies carries out computer diagnostics and the necessary repair of the “robot” box in case of the following defects in the control:
- when changing gears, jerks are felt;
- when shifting to a lower gear, shocks appear;
- the movement is carried out systematically, but the box malfunction indicator lights up on the panel.
Competent specialists carry out diagnostics of the robotic box, sensors, actuators, wiring and other elements, after which they eliminate existing defects in a short time. It is important to use the latest diagnostic equipment and narrow-profile tools in order to correctly carry out any operation. The price-quality ratio in Favorit Motors is optimal, and therefore owners of cars with manual transmission can trust professionals without a doubt.
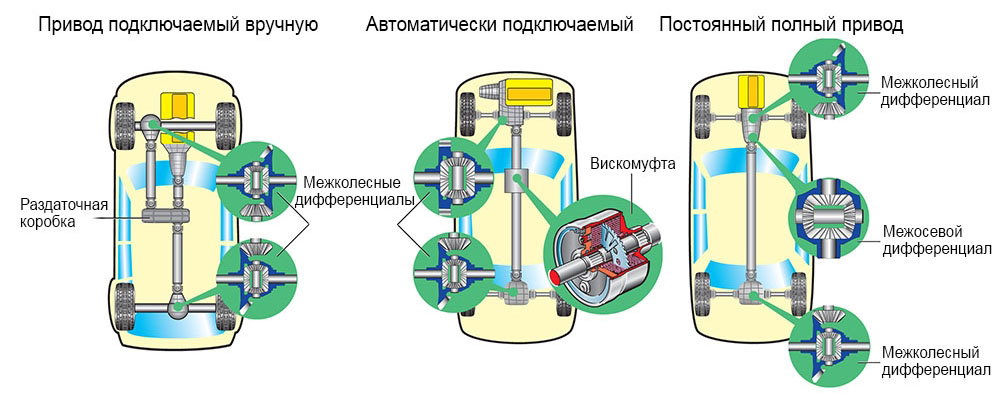
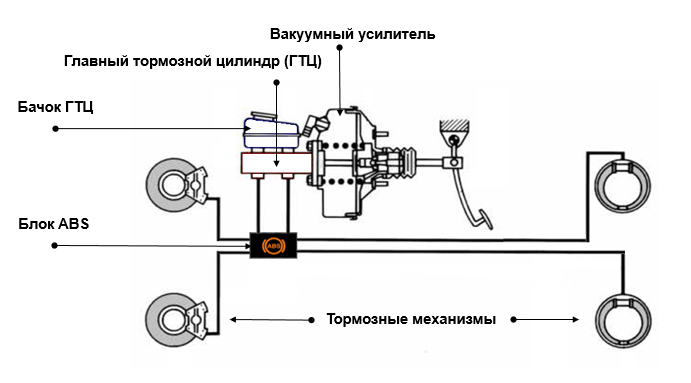