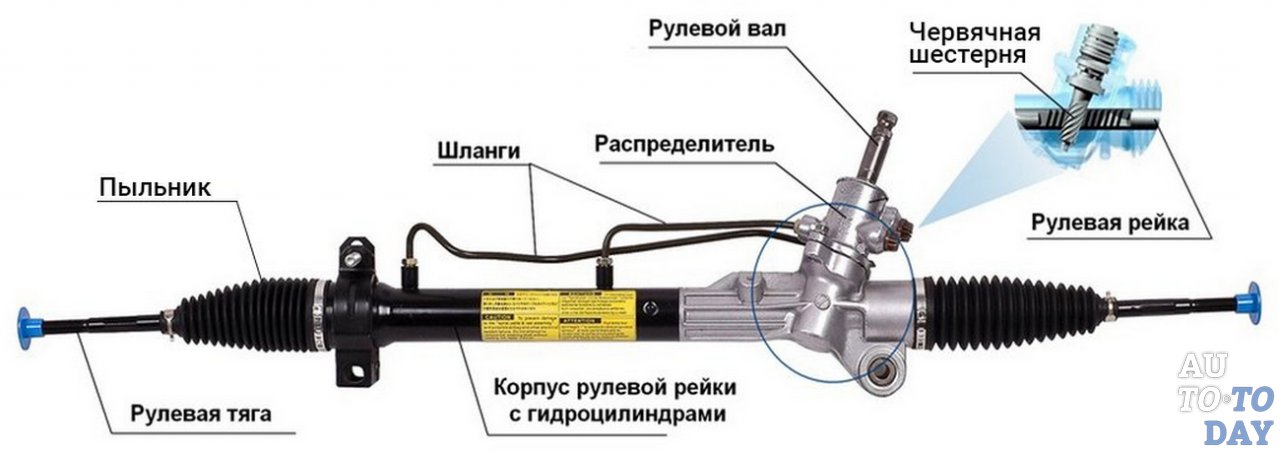
Steering rack - principle of operation and design
Content
Among all types of steering gearboxes, rack and pinion occupies a special place, if only because it is most common in passenger car designs. Possessing a number of advantages, the rail, and that is how it is commonly called briefly on the basis of the use of the main part, has practically supplanted all other schemes.
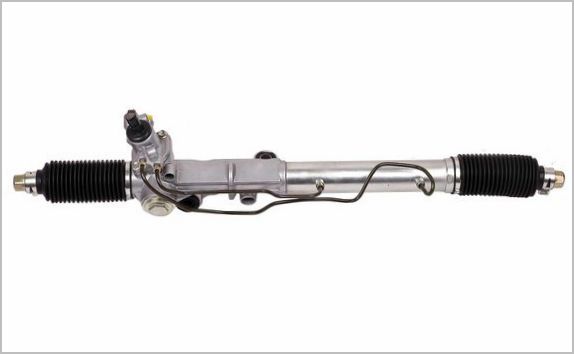
Features of using rails
The rail itself is a sliding steel rod with a toothed notch. From the side of the teeth, a drive gear is pressed against it. The steering column shaft is splined to the pinion shaft. Helical gearing is usually used, as it is silent and capable of transmitting significant loads.
When the steering wheel is rotated, the driver, acting in conjunction with the power steering, moves the rack in the desired direction. The ends of the rail through the ball joints act on the steering rods. In the section of the rods, threaded couplings for toe adjustment and steering ball tips are installed. Ultimately, the driving force is transmitted through the pivot arm to the knuckle, hub, and steered wheel on each side. The configuration is designed in such a way that the rubber does not slip in the contact patch, and each wheel moves along an arc of the desired radius.
The composition of the rack and pinion steering
A typical mechanism includes:
- a housing where all parts are located, equipped with lugs for fastening to a motor shield or frame;
- toothed rack;
- sleeve-type plain bearings on which the rail rests when moving;
- input shaft, usually placed in roller (needle) rolling bearings;
- a device for adjusting the gap in engagement from a spring-loaded cracker and an adjusting nut;
- tie rod boots.
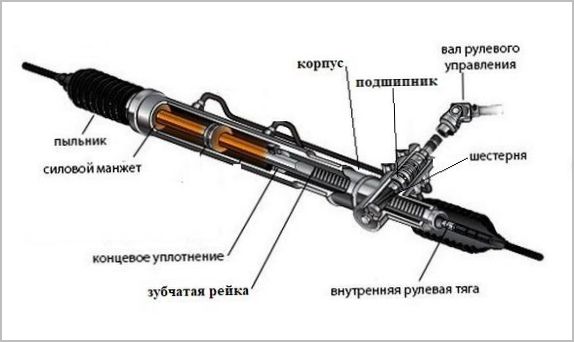
Sometimes the mechanism is equipped with an external damper, designed to minimize one of the drawbacks of the rack and pinion mechanism - an excessively strong transmission of shocks to the steering wheel from wheels falling on uneven wheels. The damper is a horizontally mounted telescopic shock absorber, similar to that installed in suspensions. At one end it is connected to the rail, and at the other end to the subframe. All impacts are damped by the shock absorber hydraulics.
The simplest mechanisms used on the lightest cars are devoid of power steering. But most rails have it in their composition. The hydraulic booster actuator is integrated into the rack housing, only the fittings for connecting the hydraulic lines on the right and left sides of the piston come out.
The distributor in the form of a spool valve and a section of the torsion bar is built into the housing of the input shaft of the rack and pinion mechanism. Depending on the magnitude and direction of the effort applied by the driver, twisting the torsion bar, the spool opens towards the left or right hydraulic cylinder fittings, creating pressure there and helping the driver move the rail.
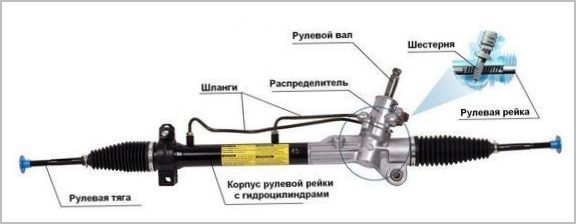
Sometimes elements of an electric amplifier are also built into the rack mechanism if it is not located on the steering column. Direct rail drive is preferred. In this case, the rack has an electric motor with a gearbox and a second drive gear. It works in parallel with the main one along a separate gear notch on the rail. The direction and magnitude of the force are determined by the electronic control unit, which receives a signal from the input shaft torsion twist sensor and generates a power current to the electric motor.
Advantages and disadvantages of a mechanism with a rail
Among the advantages are:
- high precision steering;
- ease of ensuring the transparency of the steering wheel, even equipped with an amplifier;
- the compactness of the assembly and the simplicity of the design layout in the area of the motor shield;
- light weight and relatively low cost;
- good compatibility with both aging hydraulic boosters and modern EUR;
- satisfactory maintainability, repair kits are produced;
- undemanding to lubrication and frequent maintenance.
There are also disadvantages:
- fundamentally high transparency of the steering wheel in case of use on rough roads, in the absence of dampers and high-speed amplifiers, the driver may be injured;
- noise in the form of knocks when working with an increased gap, when wear occurs unevenly, the gap cannot be adjusted.
The combination of pros and cons in the operation of the rack and pinion mechanism determines its scope - these are cars, including sports cars, operated mainly on good roads at high speeds. In this case, the rack performs in the best way and is ahead of all other steering schemes in terms of consumer qualities.
Maintenance of the mechanism is sometimes carried out in order to reduce the gap when knocks appear. Unfortunately, for the reasons for uneven wear described above, this is not always possible. In such cases, the mechanism will be replaced as an assembly, often with a factory restored one. The use of repair kits eliminates only knocks in bearings and support bushings, but not wear of the gear pair. But in general, the service life of the mechanism is quite high, and the cost of new parts is quite acceptable.
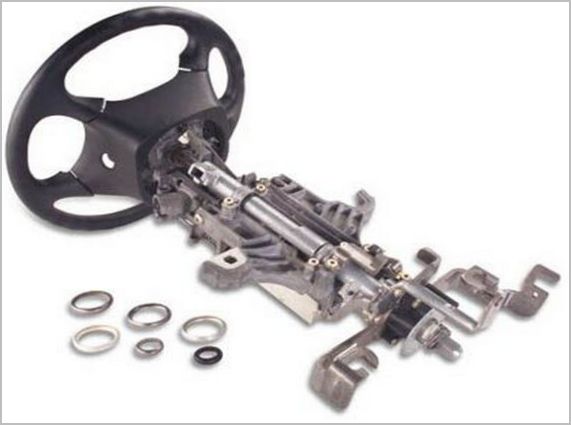
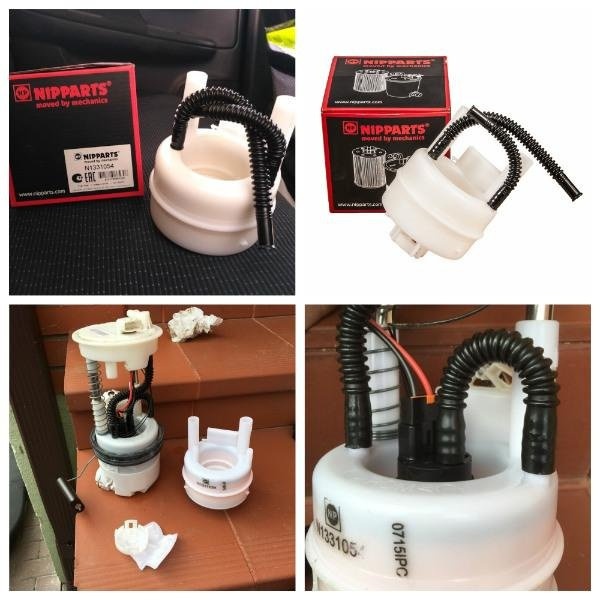